The Industrial Internet of Things (IIoT) has the capacity to reshape plant operations. The IIoT serves to connect the digital and physical worlds through the latest technology in order to improve the quality and speed of critical information. That information can be shared and used to make better-informed decisions. Many factories use a preventive maintenance (PM) program to check critical equipment with portable tools to find signs of degradation. These essential methods for discovering system glitches often miss intermittent problems. If a maintenance technician does not capture critical information at the right time, intermittent unnoticed faults can escalate into complete failure. This is where the latest portable condition monitoring devices and software enter the picture. Plants often deal with underperforming motors, and it is crucial to figure out the root cause of the motor’s failure. In this common scenario, technicians may discover the motor is running hot because of insufficient insulation in the windings. Narrowing down the reason can be difficult.
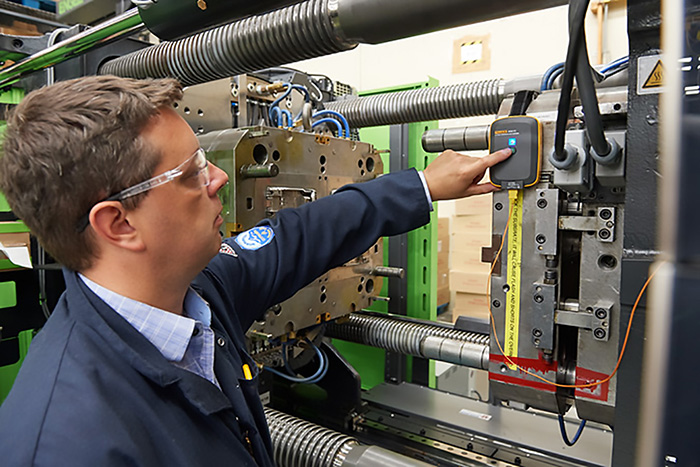
Detecting Glitches
Some plants have at least one multimillion-dollar machine, also known as a tier one asset, that is powered by smaller equipment down the line. Often, these tier one machines are equipped with monitoring sensors by design, so plant managers can keep tabs on these machines’ performance. A step down leads to second tier assets, which are often worth many thousands of dollars and are process-critical. These assets rarely have fixed sensors, so plant operators are often in the dark when it comes to raw data. For example, if a circuit is tripping intermittently and shorting a motor, and the conditions revert to normal by the time a technician arrives at the panel to troubleshoot, there is not much to do other than wait for the next circuit trip. With portable condition monitoring sensors mounted on panels of this second tier equipment, managers and technicians can see intermittent faults as they happen or over time from their desktop, mobile phone or tablet. The equipment condition data allows “eyes” into what is going on with operating equipment, leading to better decision making on repairs, adjustments or replacement. Portable condition monitoring sensors, for example, can simultaneously measure all three legs of three-phase power. A technician can attach one current sensor to each phase or use the power monitor and then view the results on a smartphone. Since all three phases can be viewed simultaneously in real time, it is easy to quickly see differences between phases.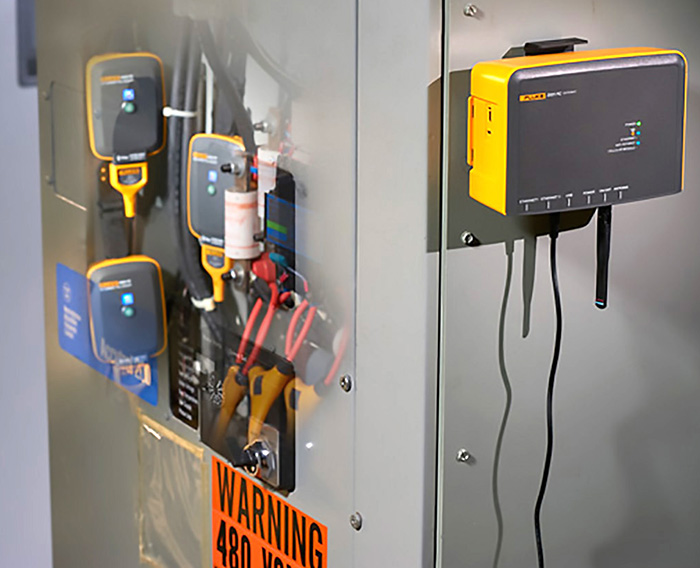