As a volumetric fluid handling technology, two- and three-screw rotary positive displacement pumps create flow and are insensitive to system pressure changes. They deliver a nearly constant volume of liquid over a range of discharge pressures. This is why two- and three-screw pumps are often the pump technology of choice for demanding hydrocarbon applications where flow or pressure demands change frequently, or even occasionally, on any given day. In designing a positive displacement pump for this application, one of the most important, but commonly overlooked, data inputs from users is detailed characteristics of their process fluid. Whether the specific fluid properties are proprietary, variable or just not known, this information must be determined and relayed to the manufacturer to ensure provision of a pump that will perform as desired in the specific application.
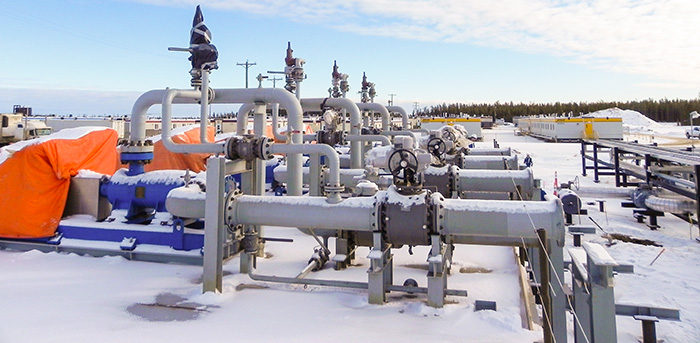
Viscosity Calculation Is Vital
The viscosity of a fluid is a key element in sizing and developing any pump, and the effects of viscosity on a positive displacement pump are much different than those on a centrifugal pump. The more viscous a fluid, the higher the flow rate will be for a positive displacement pump at a constant pressure and input speed—an advantage when handling heavy liquid hydrocarbons. For a user to ensure that they will receive a pump that will perform as desired in their application, specific detail on viscosity is critical. If a user is unsure of their fluid’s viscosity range, it is recommended to send a fluid sample to a qualified lab for evaluation. One of the widely accepted methods used in determining a fluid’s viscosity is ASTM D445: Standard Test Method for Kinematic Viscosity of Transparent and Opaque Liquids. The time it takes for a volume of fluid to flow through a calibrated viscometer under a known pressure and temperature is measured. After recording twice at two different temperatures, the kinematic viscosity of the fluid can be calculated. With the kinematic viscosity known at two temperatures, ASTM D341: Standard Practice for Viscosity-Temperature Charts for Liquid Petroleum Products can be used to develop a plot of kinematic viscosity over a range. Using this chart, the viscosity of a fluid at any temperature in the associated range can be determined. In this process, off-design conditions such as startup should also be considered, as well as seasonal changes for applications that are affected by outdoor temperatures. For these and other reasons, it is acceptable to provide a range of viscosities that represent the fluid at varying conditions so the manufacturer can establish operating limitations where required.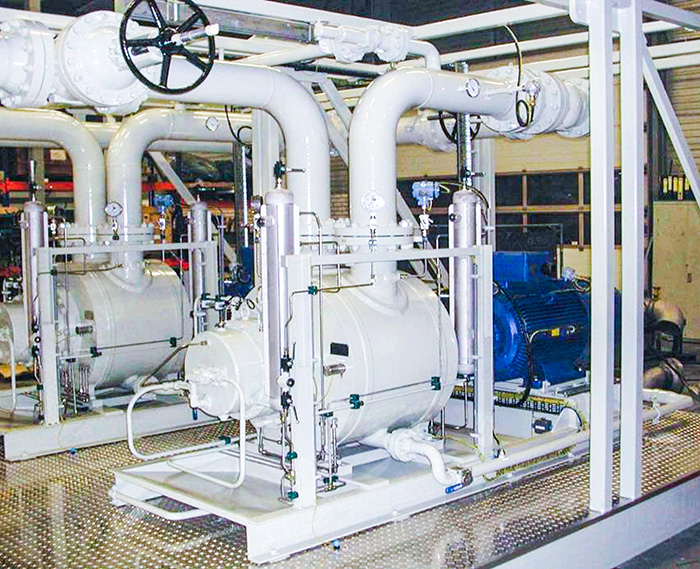
The Consequences of Inaccurate Data
Sometimes data is provided to a manufacturer during the quotation phase, but it is incorrect or incomplete. This can have a major impact on the pump, the system or both. A positive displacement pump designed or selected for a fluid where the viscosity is lower than predicted will produce less flow than expected. Low flow may lead to reduced output in a crude oil pipeline, which translates into lower throughput per day, and ultimately a financial loss. In a lubricating system, the consequences of lower flow than predicted may lead to oil starvation of bearings. On the other hand, a pump that is selected for a fluid where viscosity is higher than predicted could also have negative impacts on a system. The higher flow produced by the disparity in viscosity will draw more power from an electric motor and could potentially trip the motor’s protection circuit. In a lubricating oil system, excess flow that is dumped back to a holding tank can aerate the oil and increase its operating temperature. In extreme cases, the pump may not function properly due to inadequate suction pressure to fill the suction end pumping elements. This can lead to cavitation and excess vibration.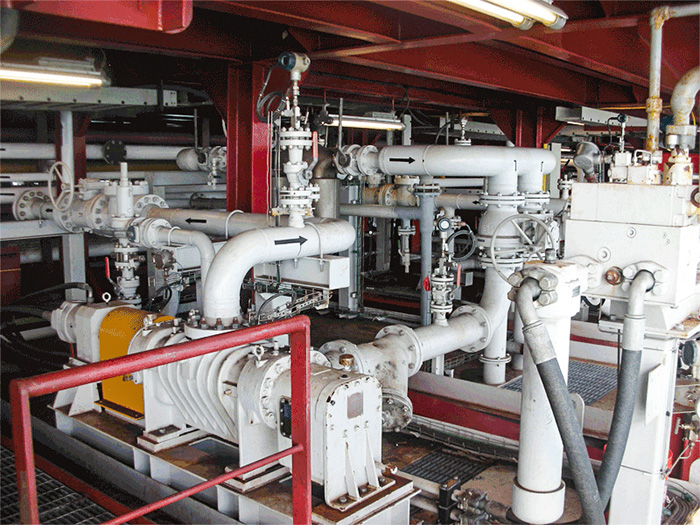