Modern software provides plants with the data they need to improve reliability while empowering pump operators to make well-informed decisions.
09/21/2015
Read part 1 of this series here. Instrumentation and monitoring technologies have become instrumental in improving plant productivity and efficiency. While these tools provide great value to the industry, the importance of the field workforce in the overall effectiveness of a plant's reliability strategy cannot be dismissed. Instrumentation and remote monitoring software must be combined with tools that empower employees to manage and maintain systems reliably and efficiently. This comprehensive strategy can help field workers increase their knowledge of system processes, analyze equipment data, and make well-informed decisions.
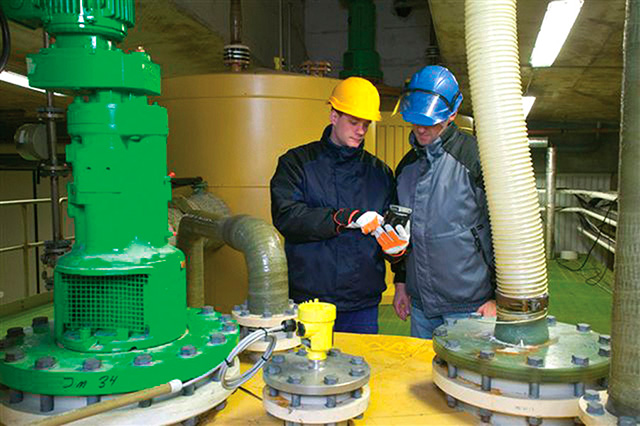
- Failure history
- Condition monitoring history
- Vendor recommendations
- Industry specific best practices
- Regulatory requirements (commitment tasks)
- Asset specific design and/or operating parameters
- Planned outages (to asset, system, operating area)
- Accessibility to the asset
- Field worker's ability to execute task
- PdM monitoring
- Environment that asset is installed in
- Process historians
- Manually collected data is sent back to the process historian where it is made available to trend along with instrumented data.
- Centralized maintenance management systems (CMMS)
- Mobile work order execution (preventive maintenance and corrective)
- Automatic updates to work order history, time and status
- Laboratory information management systems (LIMS)
- Positive sample identification and accurate sample times are sent back to the LIMS system. This ensures samples were not mislabeled.
- Reliability management systems (RMS)
- Manually collected data is sent back to the RMS where it can be used to analyze and predict failures.
- Other systems including custom built applications.
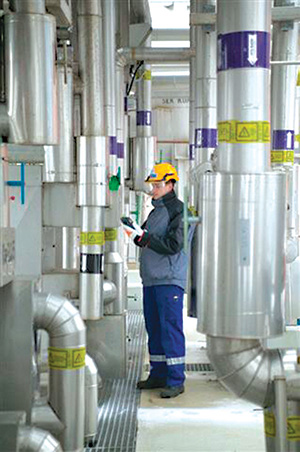
Read part 1 of this series here.