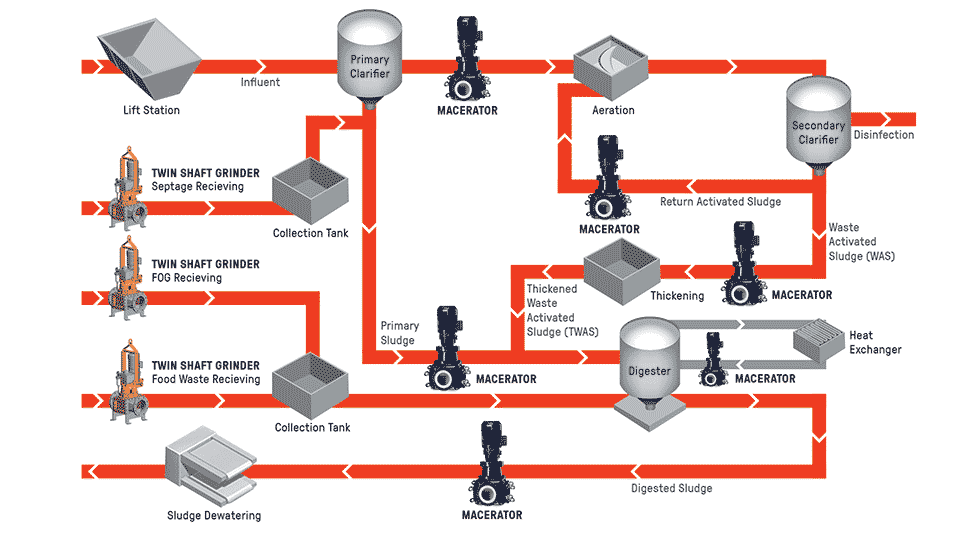
There are two main grinder types found in wastewater and industrial plants: twin-shaft grinders and macerators. Each is engineered for different performance characteristics. Determining where the grinder will be in the flow stream is key to selecting which style will yield the most favorable results for the process. In most cases, both types of grinders are used to properly reduce particles as they flow throughout treatment systems.
Twin-Shaft Grinders
Twin-shaft grinders are designed for both inline pipe installations and channels. In many cases, these units will run partially or completely dry and can handle medium-to-large solids. They are often used to protect downstream pumps and other equipment from damage.
Twin-shaft grinder basics:
- There are two designs: inline, for pipe installation, and channel, for open flow sources.
- They operate at low speed with one shaft running slower than the other, typically 40 and 60 revolutions per minute (rpm).
- One shaft holds the material as the other shaft tears the solids apart.
- Internal rotating cutter blades pull solids into cutting elements.
- Wet or dry solids can be cut; fluid must be present to move material horizontally.
- They can be set up with a solids separator or “rock trap.”
- They can perform coarse to medium-coarse grinding.
- The typical pressure is rated to 90 pounds per square inch (psi) for the inline version.
- The drive components experience a high shock load.
- The controller is set to reverse the cutter rotation if a jam occurs.
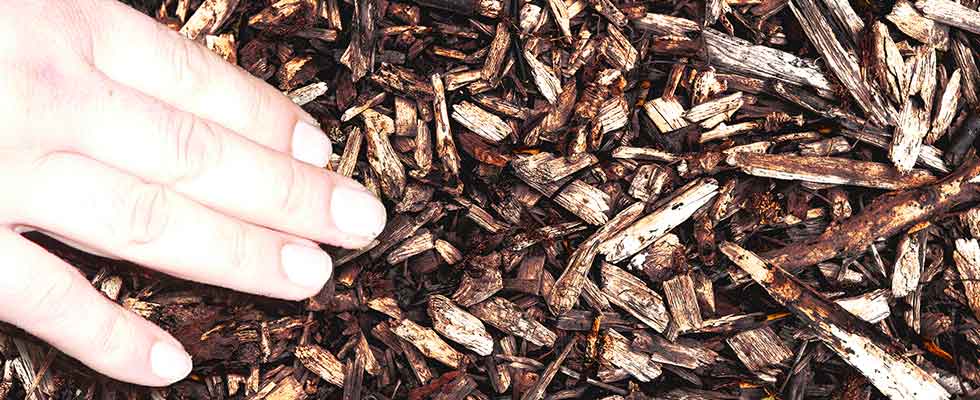
Macerators
Macerators, or single-shaft grinders, are designed for inline pipe installations. They require liquid flow through the cutter assembly to operate. Macerators are considered conditioners as they condition the sludge into small, manageable particles, keeping pumps and downstream equipment safe. Solids such as hair, wipes and rags are finely cut allowing them to easily pass through downstream equipment without reconstituting. Macerators are best suited for refined cutting after the headworks of a wastewater treatment plant.
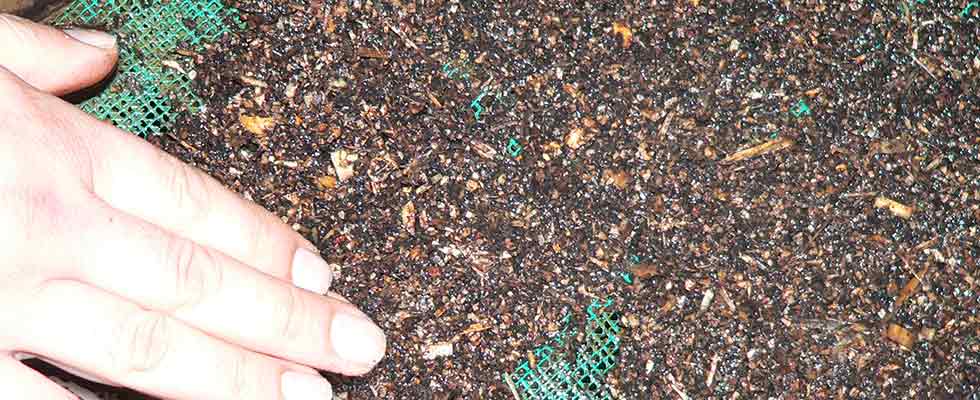
Macerator grinder basics:
- They have a defined, scissor-like cut.
- They operate at a high speed, typically 300 rpm or greater.
- Cutting is performed by shear plates with small holes and a high-speed cutter head to reduce particles to defined sizes.
- The liquid stream moves solids through the cutting element.
- Solids must be suspended in the liquid stream for cutting.
- They are capable of heavy solids separation (built-in “rock trap”).
- They perform medium-coarse to fine cutting.
- The operating pressure is up to 90 psi.
- Lower torque is required compared to twin-shaft grinders.
The treatment process diagram (top image) identifies where each style of grinder is most commonly used. As previously outlined, each style of grinder is suited for different grinding requirements. Twin-shaft grinders are not designed to finely cut rags, hair and fibrous material to the point where they are harmless downstream.
In some cases, fiber can pass through a twin-shaft grinder without being cut at all. Conversely, macerators are not designed to cut up large wood boards, metal bands or shoes but can take these particles after a twin-shaft grinder and make them more manageable for downstream equipment.
The following summarizes typical areas where each grinder is best suited for optimal performance.
Twin-shaft grinders—influent side of the plant:
- headworks
- pump/lift stations
- influent channels
- septage receiving
Macerators—inside plant after screening or twin-shaft grinding:
- primary scum
- fats, oils and grease (FOG) receiving
- grease receiving
- primary and secondary sludge
- return-activated sludge (RAS), waste-activated sludge (WAS), thickened waste-activated sludge (TWAS)
- before dewatering equipment, heat exchangers or pumps