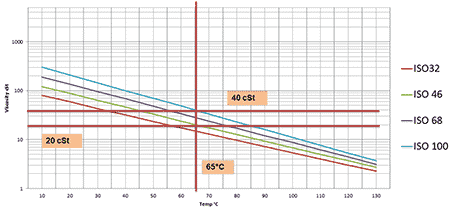
Lubrication is one of the leading causes of pump failure. In fact, it has been estimated that wrong lubricant selection accounts for as much as 20-25% of all pump failures. Like any other application, lubricant selection for pumps starts with the correct viscosity of oil. As a rule of thumb, if the pump is running at a lower speed or is more heavily loaded, a higher viscosity oil should be chosen, while if the pump is running faster or is more moderately loaded, a lower viscosity should be used. Based on this, viscosity selection for pumps typically ranges from ISO VG 32 to ISO VG 100. But is there a more scientific way to determine what the optimum lubricant viscosity should be? The answer is yes—by following the guidelines embodied in ISO 281:2007, typically referred to as the roller bearing dynamic load rating and bearing life calculation.
ISO 281 has its origins in the pioneering work of two engineers, Gustaf Lundberg and Arvid Palmgren, in the late 1940s. They first proposed a theory to explain the fatigue life of a rolling element bearing in terms of the dynamic load rating of the bearing, the applied load and the speed of rotation (Image 1).
Over the course of the next 75-80 years, scientists and engineers refined the original equation to the point where today, the latest version of ASTM D 281 (published in 2007) includes the original load rating equation modified by a multivariable scalar—aISO—which accounts for the effects of lubricant film thickness as defined by Greek letter Kappa (K), fluid cleanliness defined by a fluid cleanliness factor ec. bearing material load limits and shaft alignment (Reference: ISO 281:2007 and ISO 16281:2025) (Image 3).
The Importance of Kappa to Bearing Life
Per ISO 281, Kappa is the ratio of the actual viscosity of the lubricant in use compared to the minimum required to separate the bearing surfaces (Image 2). When Kappa is less than 1, there is incomplete separation of the bearing surfaces.
Under these conditions, asperities from one surface will impact asperities from the opposing surface and wear rates will be high. While Kappa values less than 1 should be avoided, in some circumstances it is unavoidable—for example, the output shaft of a gear reducer with a large reduction ratio. Any system operating with a Kappa value less than 1 requires the use of extreme pressure (EP) additives. For pump bearing lubrication, an ideal Kappa value is in the range of 2.0-4.0. Under these conditions, there will be a complete oil film separating the bearing surfaces, meaning wear rates should be very low.
So how can a user choose the most appropriate lubricant viscosity to achieve a Kappa value above 2.0? Conveniently, the answer lies in the ISO 281:2007 standard, which provides an equation that allows users to determine the minimum viscosity to support a dynamic load, based on bearing size and speed.
Based on this equation, a simple nomograph can be created to determine the minimum viscosity based on bearing size and speed of rotation. As the chart in Image 4 suggests, as bearing dimensions increase or speed increases, the minimum viscosity required to support the dynamic load decreases, meaning a lower viscosity lubricant can be used to achieve an optimum Kappa in the 2.0-4.0 range. Choosing an oil with too high a viscosity (i.e., Kappa >4) can cause internal churning, fluid friction and elevated operating temperatures. By way of an example, a 6313 deep grove ball bearing with a 65 millimeter (mm) (2 ½ inch) bore/shaft diameter would require a minimum viscosity of 10 centistokes (cSt) when operating at approximately 1,500 rotations per minute (rpm).
Once the minimum viscosity has been established, selecting the correct lubricant viscosity is relatively straightforward. First, the operating temperature of the pump must be determined or estimated. Once this has been done, standard oil-viscosity temperature plots can be used to select an oil that will have sufficient viscosity at operating temperature to yield an optimum Kappa. In this example, the 6313 bearing with a calculated minimum viscosity from 10 cSt from Image 4 requires an ISO VG 46, 68 or 100 to achieve a Kappa between 2.0 and 4.0 when operating at 150 F (65 C) (Image 5).
The Importance of Fluid Cleanliness
In addition to optimizing Kappa, aISO also include a term ec, defined in the ISO 281:2007 standard as the ratio of the inverse of the Hertzian stress concentration caused by the load across the rolling contact when the oil is clean, compared to stress that is focused and localized by the presence of a dynamic clearance sized particle in the rolling contact. Per ISO 281 and the related standard ISO 16281, ec and hence bearing life expectancy ranges from 0.1 for a severely contaminated lubricant to 1.0 for ideal, lab-like conditions (Image 6).
When Kappa is greater than 2.0, bearing life increases exponentially as the cleanliness of the fluid increases.
For companies that rely on pumps, lubrication is a critical success factor for extending pump mean time between failure (MTBF). In particular, selecting a lubricant to help ensure the kappa value never falls below 2.0 and that the lubricant is kept free of contamination—both particles and moisture—is perhaps the biggest deciding factor between a pump that is running and one that is shut down and waiting for repair.