Modern continuous monitoring technologies are streamlining maintenance programs and improving plant operations.
03/31/2016
While revolutionary technology changes have transformed the world of health care, entertainment and retail, the industrial marketplace has also been impacted by the digital era. The Internet of Things (IoT) is a hot topic most people have heard of—but what does it actually mean?
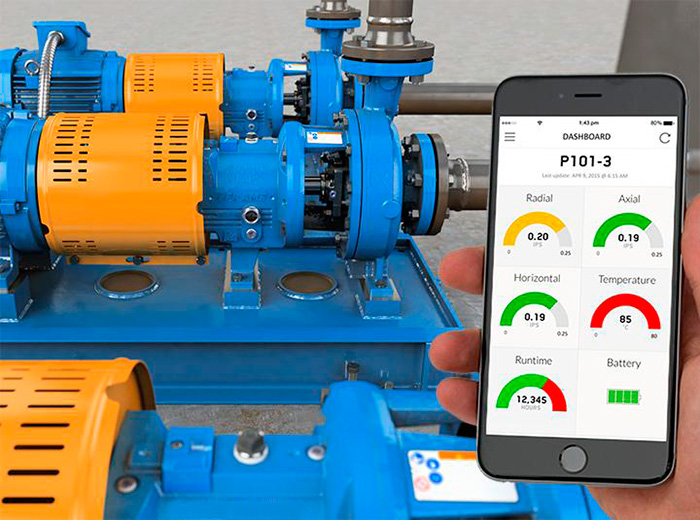
What Is Smart Pumping?
For decades, the pump industry has been slowly converting from taking a reactive approach to pump and equipment failures to embracing a proactive strategy to dealing with detectable problems. Smart pumping and the IIoT are speeding that transition. Unlike conventional pumping systems that require manual maintenance and checkups on pump performance, smart pumping uses computer technology and sensors to operate, control and protect pumps and their systems. Smart pumping technology offers early detection and real-time diagnostic processes to troubleshoot equipment failures and unusual operating conditions. Common causes of equipment failure include continuous operation below minimum flow; dry-running caused primarily by closed suction valves; insufficient net positive suction head available (NPSHA) causing cavitation; and heat buildup and subsequent liquid vaporization resulting from a closed discharge valve. Smart pumping systems and monitoring technologies can protect against and offer early warning signs for these and other conditions. This modern system tracks any changes in equipment health without manual intervention. By tracking vibration levels, temperature, run-time hours and battery life, these predictive maintenance devices provide real-time updates about equipment health and collect data that plant managers can use for the future. As most industry professionals are aware, excessive vibration can quickly cause wear and decrease pump equipment life. If a breakdown occurs as a result of improper operating conditions, plant managers will have a continuous record of high vibration or temperature levels and will be able to examine why the breakdown occurred. This shift in the industry has significantly reduced pump operating costs and life-cycle costs. Predictive maintenance programs can reduce overall maintenance costs by up to 30 percent and eliminate breakdowns by 70 percent. When most companies manage hundreds and sometimes thousands of machines, effectively collecting and analyzing data can be difficult. This challenge can limit the ability of plant operators to monitor their equipment continuously and in real time, causing a reactive approach to equipment monitoring. Using a proactive approach, on the other hand, significantly reduces downtime, extraneous costs and safety concerns in any pump-operating facility, no matter the amount of equipment. In the past, the number and types of machines that were continuously or periodically monitored were limited. In a smaller organization where people wear multiple hats, the proactive approach of monitoring is ideal because it can quickly be deployed to as many machines as necessary. Self-diagnostic features that detect pump failures give users the time to schedule maintenance and prioritize a problematic piece of equipment before a breakdown or the next visit from a pump specialist.Make the Data Meaningful
As aspects of smart pumping, such as sensor technology, become more advanced and economized, multiple sensors are being incorporated into predictive maintenance devices.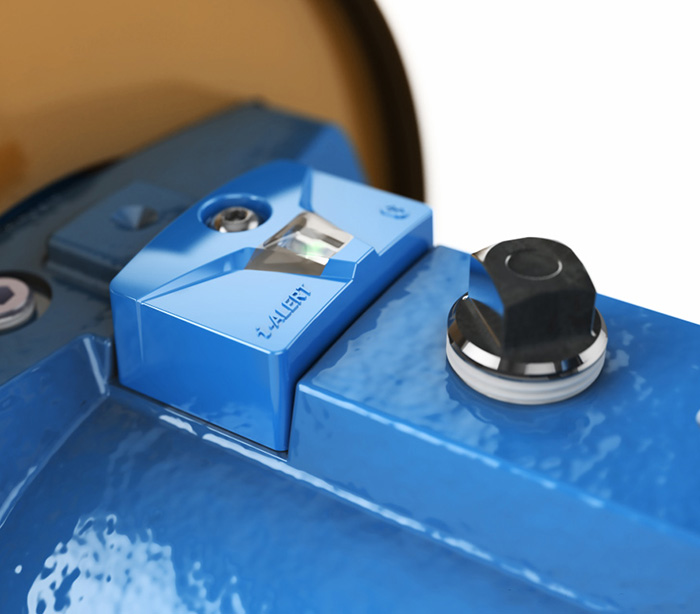
What Does the Future Hold?
By making operations safer, faster and more efficient, data trends taken from smart pumping systems can be used for further industry growth. As the IoT expands in every industry, a clear shift in the way businesses are transacted and services are provided will occur. From streaming music to making travel reservations online to arranging a ride through an app, many industries are shifting to a mobile user experience. As these technologies develop, the pump industry must recognize a shift in the traditional service model and rise to these technological advances. Any successful maintenance program requires several layers of support, including top-level management, reliability, maintenance, engineering and operations. As the industry begins to experience a large turnover of highly skilled and knowledgeable talent, the IoT can help fill the skills gap created by personnel leaving the plant. Intuitive, actionable information from equipment health monitors can be used to help buffer the influx of workers who may not know the industry as well as seasoned professionals. The pump industry can leverage this emerging technology to ease that transition. With more time available after streamlining inspection and maintenance practices, industrial plants can incorporate more innovative pumping solutions to move the industry even further forward.
See other Maintenance Minders articles here.