Parts made of these materials can help solve some common pumping problems.
Sims Pump Valve Company, Inc.
06/27/2017
In a market full of product choices at different prices and quality levels, structural composite engineered aftermarket solutions can offer end users value-added alternatives to some imports. Engineered aftermarket parts can provide longer life, lower operating costs, reductions in energy costs with a healthy return on investment (ROI). Instead of repairing a pump, or replacing the old pump with a new pump of the same type or quality, many aftermarket engineering companies offer the end user better solutions in the form of longer-lasting products and parts.
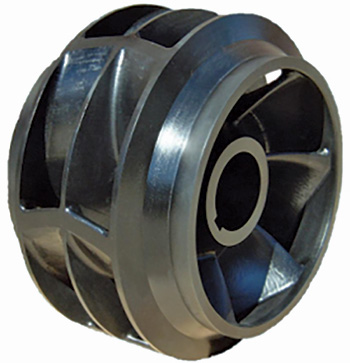