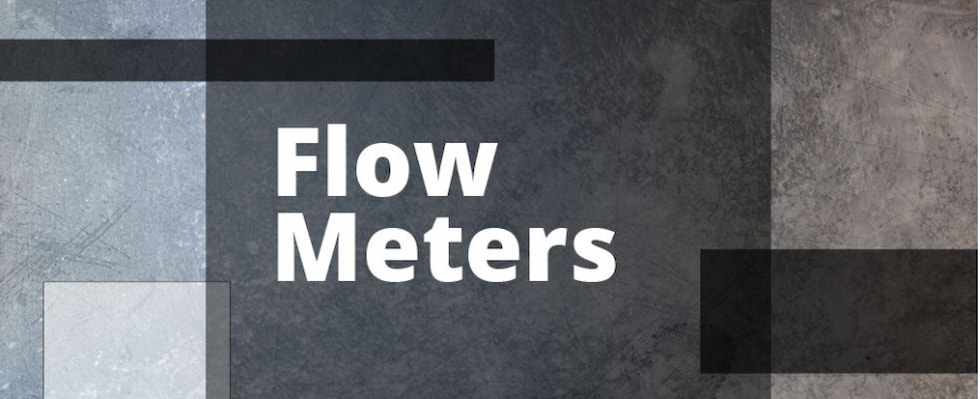
Pump systems are a crucial component of water and wastewater operations. They must be consistently operated within manufacturer specifications to ensure utmost performance and reliability to reduce their long-term life cycle costs.
Ultrasonic clamp-on flow meter technology can ensure the reliable operation of crucial pump equipment. Specifically, employing an ultrasonic transit time clamp-on flow meter paired with a variable frequency drive (VFD) to control the flow rate through pumps can help save energy and extend equipment life.
Most water and wastewater plants have positive displacement and/or dynamic displacement pumps in place for their demanding operations. Typical applications range from water intake, filtration and booster pumping to chemical injection and sewage lift stations.
Many pump systems are original to their site and were designed when there were fewer operating concerns and regulatory requirements than there are today. Some facilities have added new pumping resources or switched to larger capacity pumps to address increased operational demands. Plant personnel are focused on protecting pump assets from a variety of operating hazards.
For example, if centrifugal pumps have too little flow for an extended period of time while their motor is running at full speed, excessive wear and internal damage can occur. When no fluid enters the pump impeller, it will churn the same volume of fluid as it rotates. Friction will lead to increased fluid temperature. If sustained, this can cause excessive pump wear and failure.
Pumps also consume large amounts of electricity. As such, they should run at the required speed and no faster. Pumps are subject to failure and downtime if not properly monitored and maintained.
Issues With Flow Rate
Flow meters used to monitor flow readings in water and wastewater treatment systems are essential to properly monitoring the process, diagnosing system errors and ensuring pump performance. Almost all pumps have a specified performance window of operating curves. Deviating from this may produce stress that damages a pump. Installing proper instrumentation helps identify problems before the pump is damaged or maintenance and operation resources impacted.
A key requirement for plant operators is staging pumping equipment based on variable demand. Flow meters are commonly used to stage pumps off, since it is difficult to determine the right time to begin pump shedding based on pressure readings alone. The meters also assist with putting pumps to “sleep” at certain intervals to save energy and minimize excessive wear and tear. They provide a milliamp signal back to the VFD to initiate this action.
Minimum continuous safe flow is the flow at which a pump can operate continuously without excessive wear from hydraulic anomalies and temperature rise associated with low-flow conditions.
At reduced flow, pumps can experience a flow reversal where the fluid turns and flows back upstream. This results in internal recirculation, which is often referred to as suction recirculation, and subsequent heat buildup. Internal recirculation occurs at reduced flow rates when more liquid approaches the eye of the impeller than can pass through the pump.
Identifying the Right Solution
Accurate flow rate data is vital in understanding pump health and efficiency. Flow meters already in line with the pump may provide performance data to compare with pump power and speed information over time. If no such flow measurement device is in place, ultrasonic flow meter technology can be an effective option.
Experience has shown ultrasonic transit time clamp-on flow meters can serve as an alternative to traditional choices such as electromagnetic flow meters in water and wastewater applications. In-line devices require a system shutdown for installation, whereas ultrasonic clamp-on flow meters can be retrofitted to existing piping while pumps are in operation.
Unlike orifice plates, which cause a permanent pressure drop in the system, ultrasonic meters provide a high turndown ratio over the full operating range of pumps.
Ultrasonic transit time flow meters measure flow rate by propagating ultrasound waves into liquid-filled pipes and measuring the time of flight. With clamp-on technology, the meter is nonintrusive—a design that provides a number of key advantages:
- reduced installation costs
- uninterrupted production
- application flexibility across a wide range of pipe sizes
- no pressure head loss
- no contact with internal liquid
- no moving parts to maintain
- easily maintained without having to cut into piping
Ultrasonic clamp-on flow meters measure volumetric flow rates in clean liquids as well as liquids with small amounts of suspended solids. They are easy to use and have helpful diagnostics to take guesswork out of programming. In some cases, the flow meters support an encoder output for use with cellular endpoints for connecting to advanced metering infrastructure (AMI) cloud-based software.
Many water and wastewater plants use a pump control package consisting of an ultrasonic transit time flow meter that provides flow rate information to a VFD. This control solution prevents pumps from running with too little flow for an extended period of time. It controls pump operation to closely match system demand—resulting in energy costs savings.
Within the pump control package, a duplex VFD panel and a single ultrasonic flow meter work in tandem to control the pump speed and run time. In automatic mode, the master pump will run at the selected speed to meet desired pressure until the flow meter has signaled a low-flow condition for a length of time, which will slow the pump to a minimum speed or stop the system entirely.
Advantages for End Users
Protecting investments in pump system assets goes hand in hand with improved process reliability, fewer equipment replacements, a decrease in pump reconditioning expenses, reduced energy costs and less disruption in normal operations. Ultrasonic transit time clamp-on flow meters employ robust diagnostics to accurately measure flow, help identify potential pump operating issues and initiate preventative maintenance programs, thus extending the life of assets while reducing cost of ownership.
Plant operators have seen that an ultrasonic flow measurement solution with a VFD to control flow rate and automate pump startup/shutdown also helps to reduce energy consumption and has a positive impact on the bottom line.
Pumps are vital systems that consume a great deal of energy and are expensive to rebuild or replace. As such, it is important to make this equipment run more efficiently and discover problems before they can escalate.
For water and wastewater facilities, the use of a state-of-the-art control package for pump systems enables plant personnel to focus on operating demands and spend less time dealing with equipment reliability issues.