11/29/2012
This article will discuss a case of how measuring vibration can help detect cavitation issues. It will also show how this can relate to a bigger problem at the plant. Sometimes a proposed change of pump type is too drastic. Instead, detailed analysis and thinking should occur before replacement.
Background
A chemical plant in the southeastern U.S. used six horizontal split case cooling water pumps to provide cooling water to a production facility. These six pumps operated in banks of two units taking suction from three cooling towers and feeding it to three plant processes:- Process A (cooling tower A, feeding pumps A and B)
- Process B (cooling tower B, feeding pumps C and D)
- Process C (cooling tower C, feeding pumps E and F)
Performance
As shown in Figure 1, a best efficiency point (BEP) was at 4,800 gallons per minute (gpm) for the 11.4-inch impeller. The flow varied between 2,800 gpm and 5,000 gpm, depending on the process demand. This corresponded to power consumption between approximately 130 horsepower (at 69 percent efficiency) to 140 horsepower (at 83 percent efficiency). The required variation of flow was accomplished by the main process (its piping and valving), while the pump isolation valves always remained fully open and were operated only when the pump was removed for maintenance, or as in this example, as a temporary method of performance reconstruction during the pump field test.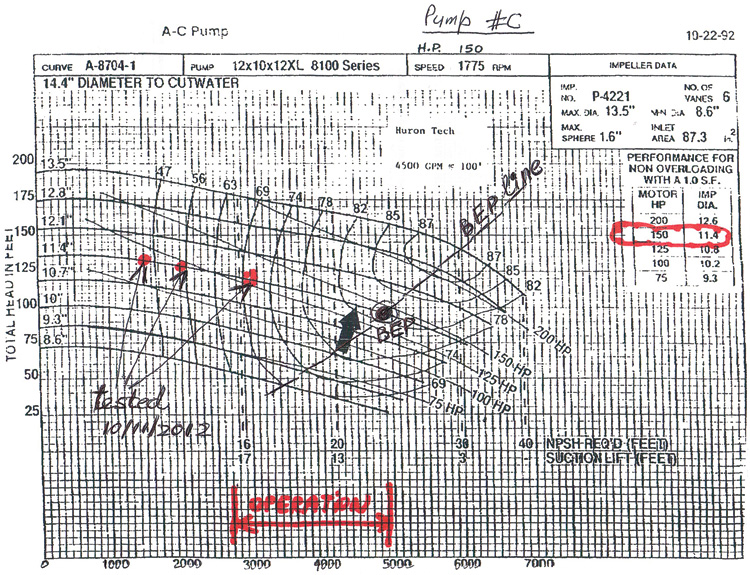
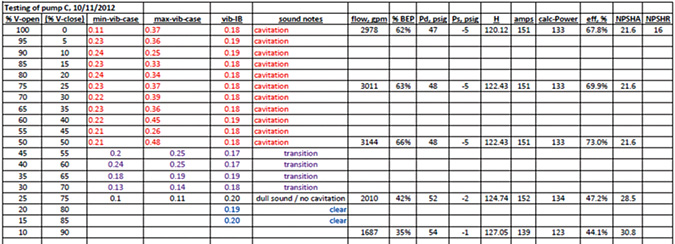
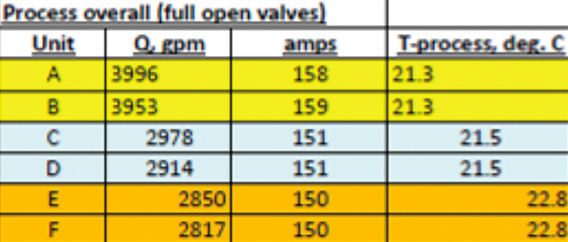
Suction Performance
The main indicator of reliability degradation—typically indicating a need for repair or overhaul—is an increased level of vibration. To assess that, the overall level of vibration was measured at two locations—the pump’s inboard bearing housing and the suction/inlet portion of the casing housing. Vibration data (also tabulated in Figure 2) are plotted as a function of flow in Figure 4 (discharge valve was closed in 5 percent increments). Vibration measurements taken at the bearing housing remained steady at approximately 0.18 to 0.19 inches per second, which was below the warning level (field criteria for the warning level was 0.30 inches per second and 0.50 inches per second). While this level was elevated compared to what would be expected from the new installation, it was low and acceptable for a typical field case example.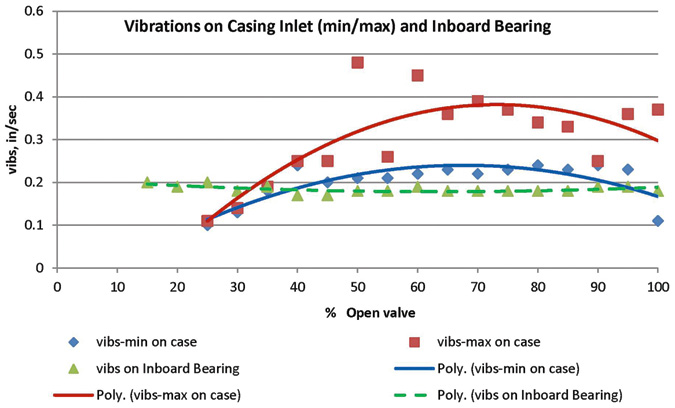
Reliability
The need for action is usually determined by measurable economic impact on the pump life and satisfaction—or lack of—with overall plant performance. If pump performance fails to deliver the required flow for the process, a repair or change to the pump or the system should be considered. In this example, the pump flowed close to its original curve and operated in the expected operating region. The pumps satisfied the plant’s flow requirements. From the energy/efficiency perspective, no significant degradation of performance occurred. Based on a computerized program estimating pump performance (www.mj-scope.com/pump_tools/pump_efficiency.htm), such a pump should theoretically have approximately 85 percent efficiency at 5,000 gpm and 100 feet of head (see Figure 5 on page 24).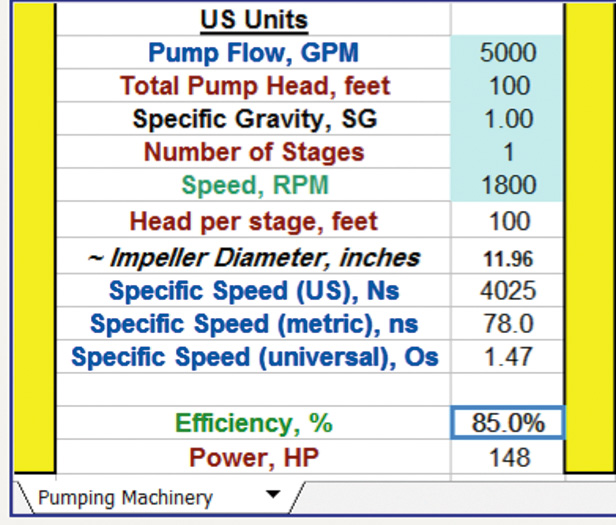