The Internet of Things (IoT) is a phrase in the limelight. The concept of IoT is extremely appealing, in all forms, to commercial industry. The technology of IoT has been implemented in various industries globally and it is finally approaching the rotating equipment industry. To fully explain and understand how IoT technology can be implemented to increase mechanical seal reliability, a description of maintenance philosophies is needed. There are three main types of maintenance philosophies in industry today: reactive, preventative and predictive. Currently in the pump industry, and more specifically with mechanical seals, most of the maintenance is either in the reactive or preventative ideologies. This is where the current model of IoT comes into play. IoT is a powerful tool that will enable the industry to progress to a predictive maintenance model. This is accomplished by using advanced technology in several key areas such as device connectivity, data storage and cutting-edge analytics.
Pitfalls of Reactive Maintenance
Reactive maintenance, at first glance, seems like a great idea. The old saying “if it ain’t broke don’t fix it” comes to mind when thinking about this maintenance strategy. The main practice of this maintenance strategy is that users do not replace equipment until it is damaged or broken. This practice creates an environment where a failure of the mechanical seal can result in secondary damages to the pump and support systems, resulting in an unplanned shutdown of the equipment. This forced shutdown can create less-than-ideal situations for the teams in charge of the equipment. An example is a mechanical seal damaged beyond simple repair that now allows dangerous process fluids to leak to the environment. After decades of implementing this maintenance strategy and gaining better insight into industrial equipment, most modern facilities shifted to a maintenance philosophy that is preventative rather than reactive.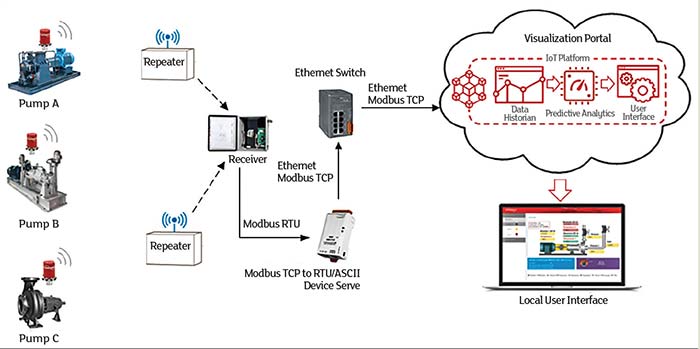