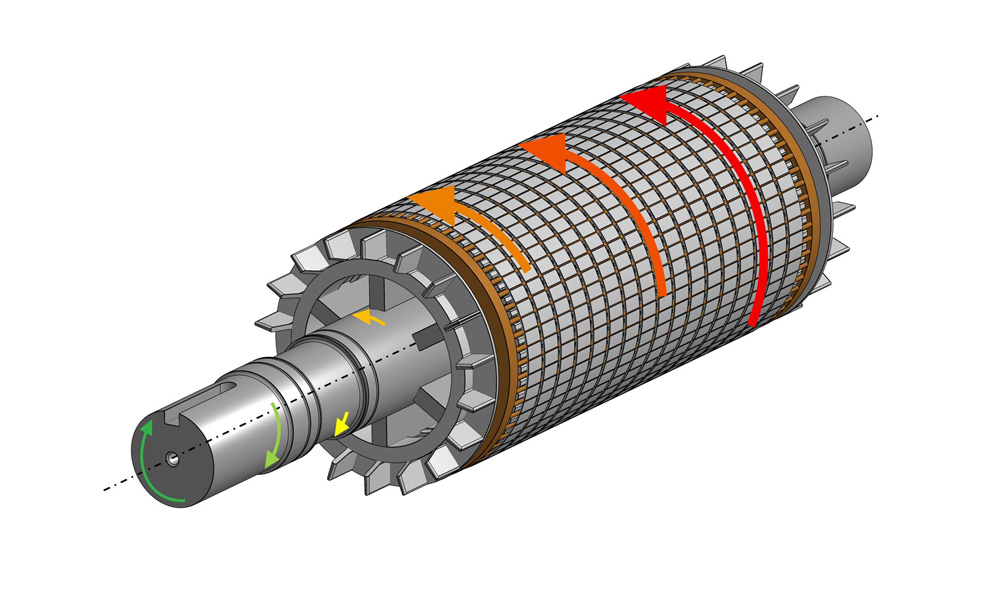
In industrial reliability circles, motor vibration is a well-documented and much-discussed topic. The usual suspects include things that go wrong on installation, get damaged or show up as a motor is operated over time, leading to issues that can be rectified without design changes to the system. But what about when there are vibration problems upon startup and nothing is broken? When a motor cannot be shimmed, realigned, repaired or otherwise to solve a vibration problem, users may analyze the structures of a drivetrain. For users in those situations, this article will provide an overview of the most common mechanical motor application analyses industry requires, all centering around resonance issues inherent to the motor or driven equipment’s design.
All three topics discussed in this article are issues of mechanical resonance and are studied through some form of modal analysis (analyzing a system to obtain its various natural frequencies). Resonance is a condition created when a periodic exciting force interacts with a mechanical body that has some natural frequency near an exciting force frequency. Think of the difference in height your child goes on a trampoline when you give them regular, well-timed bounces versus poorly timed ones. Exciting forces in motor-operated applications include electromagnetically induced harmonics, load-related mechanical forces or are a result of mechanical imbalance in the rotor system. Spring constant is another common phrase used in these analyses and is meant to quantify a body’s ability to resist a force over a unit distance (for example, pound inch per radian for angular systems or pounds per inch for linear systems).
Stiffening and damping are phrases typically used when finding solutions to vibration problems, with stiffening indicating some increase in a body’s ability to resist deflection and damping indicating some method of absorbing the energy produced by vibrations. One could think of stiffening as using thick steel to make a slinky instead of plastic and damping as trying to use a slinky under water instead of in air. Note that a motor can be perfectly designed and manufactured, show flawless operation during factory tests and still have resonance issues in operation. This is often due to unforeseen excitations interacting with drivetrain characteristic natural frequencies that can only be solved through design changes.
Torsional Analysis
Most common in reciprocating pump and compressor applications, a torsional analysis is intended to characterize a drivetrain’s dynamic responses to the oscillating torques of reciprocating loads. This analysis is performed in a radial reference frame, looking down the central axis of shafts, with an aim to avoid torsional resonant conditions that lead to excessive vibration and/or motor current pulsations. Imagine a slinky being twisted and released at multiple points and the springlike responses it would have as it returns to its original orientation. As this analysis depends mostly on the reciprocating equipment’s characteristics, the driven equipment manufacturer carries out the full analysis. The analyst will characterize the equipment’s torque requirements through a full crankshaft revolution (resulting in a crank effort curve similar to Image 2) and then characterize the driven equipment’s rotating components to determine a torsional spring constant for the assembly, which is then modeled with the motor OEM’s provided motor shaft torsional spring constant. These spring constants enable the analyst to characterize the radial location of lengthwise shaft portions as the shaft dynamically responds to the oscillating torques, with shaft step diameter, length and radii between steps being the main determinants for how much a shaft twists.
To carry out this study, an analyst needs complete motor shaft dimensions/material details, the inertia and weight of the motor rotor assembly, a calculated torsional spring constant of the motor shaft, and expected motor operating speeds. Results are presented in a report that outlines the calculated torsional natural frequencies of the drivetrain at various modes and the corresponding excitation frequencies arising from the motor’s speed, the driven equipment or both. The report will summarize areas of concern for torsional resonance and recommends methods to increase separation margins between excitations and natural frequencies.
If modifications are needed, an application will be impacted by either stiffening the drivetrain components, damping vibrations with equipment modifications or moving natural frequencies through drivetrain inertia modifications (typically through a flywheel assembly). A related investigation to torsional resonance is that of motor current pulsation, which involves the same excitation forces as torsional vibrations but with an aim to characterize the interaction of the electromagnetic stiffness of a motor (i.e., a synchronous motor’s synchronizing power) to the reciprocating torques imposed on it. Typically, a result of this study will be to determine a compressor factor that will limit stator currents to a maximum of +/- 66% of their rated value by the addition of inertia in the drivetrain, again through a flywheel.
Lateral Critical Speed Analysis
An analysis typically reserved for high-speed (usually greater than 1,800 rotations per minute [rpm]) motors is the lateral critical speed analysis. Often referred to as just critical speed analysis, this is a study similar to a torsional analysis but is performed axially looking at the bending (instead of twisting) modes of a drivetrain. Imagine horizontally holding a slinky at both ends, then pulling down in the center and releasing to watch the vertical springlike response it has as it returns to its original orientation. The basic goal of a critical speed analysis is to determine if the natural frequencies of a shaft system (typically the first and sometimes second modes) land at frequencies close enough to operating speeds to produce mechanical resonance. The analysis requires characterizing the lateral spring constant of a shaft system to determine deflection of the motor’s rotor body at various axial locations due to the weight of the rotor itself along with forces such as unbalanced magnetic pull (between motor rotor and stator) and those resulting from mechanical imbalance (i.e., residual imbalance).
To carry out this study, the same data on the motor shaft, rotor assembly and motor speed range needed for a torsional analysis is required, except for the torsional spring constant. For accurate results, values for unbalanced magnetic pull, residual imbalance and bearing spring constants are also required. Results will include the calculated lateral critical speed(s) of the rotor system, typically given as a single rpm value and sometimes as a speed map, showing separation margins between operating speed excitations and the calculated critical speeds. Additionally, through impact hammer testing (or bump testing), natural frequency spectrums for rotor assemblies can be verified. Application impacts include possible changes to the shaft dimensions/material to mechanically stiffen it or change its mass, as well as modifications to the stationary motor components such as the frame or bearing brackets that will dampen expected vibrations. Finally, certain speed ranges might be designated as keep-out zones where operation within 15% to 25% of a critical speed is not recommended.
Reed Critical Frequency Analysis
A reed critical frequency (RCF) or reed frequency analysis is meant to characterize the natural frequency at which a flange-mounted motor will oscillate to determine if resonance issues due to operating speeds or other excitations might cause excessive vibration. For this, imagine holding a slinky vertically from the bottom end, flicking the top of it and watching its springlike response as it returns to its resting position. The most common analysis method involves calculating the static deflection for a motor due to its own mass at its center of gravity in a flange-mounted, horizontal position. Using this deflection and the expected mechanical spring constants of the motor flange and body, an estimated natural frequency for the motor can be found using the formula in Equation 1 from The National Electrical Manufacturers Association (NEMA) MG-1, Part 20.23.
To perform this study, an analyst requires dimensional and material details on the motor components to determine total mass, center of gravity and individual components’ resistance to deflection. This data is maintained by the motor manufacturer as well as calculated values for a motor’s static deflection, center of gravity and RCF. According to separation between operating speed excitations and the calculated RCF, application impacts might include stiffening the motor support structure, moving natural frequencies via the addition of mass or the damping of vibrations through elastic flange mounts. Like a lateral critical speed analysis, the RCF of a flange-mounted motor can be verified through impact hammer testing.
With proper analysis, resonant vibration problems inherent to a drivetrain design can be resolved.