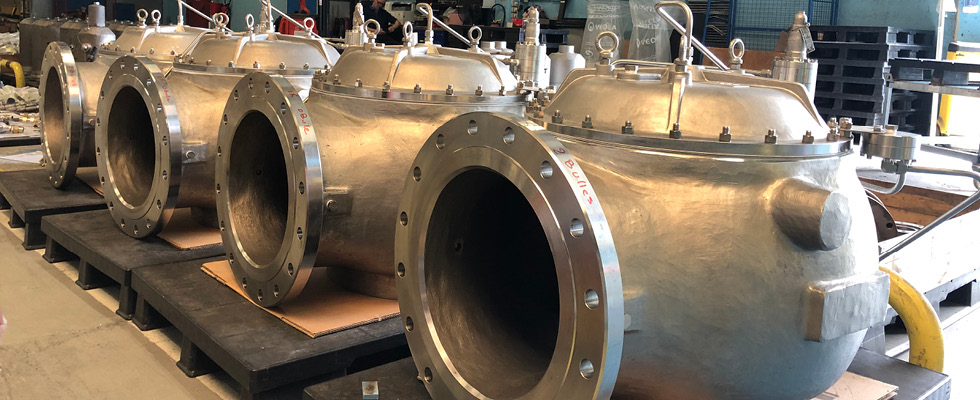
As industries worldwide shift toward cleaner and more sustainable energy sources, natural gas has emerged as a key player in the energy transition due to its cleaner-burning fuel status. Consequently, the demand for natural gas is on the rise, with projections predicting an increase at an average annual rate of 0.9% between 2018 and 2035.
The main challenge, however, lies in its efficient transportation and storage across global markets. Liquefied natural gas (LNG) is often the preferred solution because it dramatically reduces the volume of natural gas and enhances ease of transport. When methane is cooled to a liquefied state at -258 F (-161 C), its volume is reduced by approximately 600 times. This efficiency has led to anticipation of a 3.6% annual growth rate for LNG over the same period. To meet this rising demand, LNG infrastructure must prioritize safety, reliability and efficiency—areas in which high-performance valve technology plays a crucial role.
The Role of Valves in LNG Operations
Valves are integral to every stage of the LNG supply chain, from gas processing and liquefaction to storage, transportation and regasification. The extreme operating conditions of LNG—particularly the cryogenic temperatures required for storage and transport—necessitate the use of highly specialized valve designs that can maintain tight shutoff, prevent leaks and withstand severe thermal stresses.
Regulatory compliance is also critical, as the LNG industry is governed by a stringent framework of international, national and regional codes and standards designed to ensure the safe and sustainable development of the sector. Valves must comply with standards from bodies such as the International Organization for Standardization (ISO), which outline, for instance, requirements for fugitive emission control, and the American Petroleum Institute (API), which include requirements related to pressure containment and performance in extreme environments.
Controlling Methane Emissions in LNG Applications
Controlling methane emissions in LNG applications is a critical operational and environmental challenge for operators. Although methane remains in the atmosphere for a shorter period than CO2—around 12 years compared to the centuries-long life span of carbon dioxide—it is a far more potent greenhouse gas, absorbing much more energy while it exists in the atmosphere. Methane’s warming potential is more than 80 times that of CO2 in the first 20 years after its release into the atmosphere.
Methane emissions in LNG operations occur due to various factors such as leaks from valve packing glands (fugitive emissions) and routine venting processes during natural gas production, processing and transportation. Other factors include venting from storage tanks and dehydrators and depressurization equipment during maintenance. Industry studies estimate vented emissions per venting event are at 2.6% (by mass) of the initial liquid volume in storage tanks.
Leakage from valve packing glands is a common issue in various industrial applications. The packing gland is responsible for sealing the valve stem, preventing the process fluid from escaping. However, over time, the packing material can degrade, leading to leaks. This can be caused by factors such as frequent stem actuation, high temperatures and aggressive fluids.
One way for manufacturers of isolation and control valves to address this issue is to adhere to ISO 15848-1, a global standard that outlines testing methodologies for evaluating external leakage in valve stem seals and body joints of these valve types. This compliance ensures suitability for use in handling volatile air pollutants and hazardous fluids. For venting from storage tanks, pilot-operated pressure relief valves (PORVs) offer more stability near the set pressure than other valve types, as they operate under a straightforward principle: the higher the pressure, the better the bubble-tight seal. The modulating pilot flow adjusts the main valve lift, which limits the time the valve remains open.
The Importance of Manufacturing & Testing Standards
Manufacturing quality is a crucial factor in the LNG sector, where precision and reliability are essential. Critical components of high-performance valves undergo comprehensive inspections to ensure their integrity. Sensitive areas, such as machined functional surfaces of castings, including hard-faced or lapped components, are subject to liquid penetrant examinations carried out by qualified professionals (Cofrend Level II or SNT-TC-1A, in the OEM’s case). This nondestructive testing method involves applying a liquid across the surface, followed by the application of a chalk-like developer to highlight any potential defects. After drying, the surface is examined under specific lighting conditions (1,076 lux [lx]), detecting cracks as fine as 150 nanometers, where the liquid may have remained trapped.
The LNG purification process also demands the use of clean, high-quality equipment, beginning with the selection of materials like stainless steel to prevent rust. However, maintaining cleanliness is not limited to material choice; it also extends to the entire assembly process. Manufacturers implement rigorous procedures to manage and control potential contaminants throughout production. At the manufacturer in question, for instance, pressure relief valves for LNG applications are assembled in the sterile environment of a dedicated white room following specific protocols to minimize the risk of cross-contamination. Before assembly, parts undergo degreasing and are treated with specialized lubricants to ensure optimal performance.
Testing processes are also stringent, using oil-free air to maintain the required level of cleanliness. Additionally, the technicians working in these controlled environments adhere to strict hygiene protocols, wearing sanitized gear, including lint-free overalls, Charlotte fleece and protective overboots.
The testing capabilities of a manufacturer also play a pivotal role in meeting LNG industry requirements. At the OEM’s facilities, for example, fugitive emission testing is performed according to the ISO 15848-1 standard to ensure the assembled pressure-containing parts and seat maintain tightness. Leak tightness is measured using pure helium at more than 99%, and the acceptance criteria, based on calibrated mass spectrometer analysis, are stringent at less than 10-8 Pascal
cubic meters per second (Pa.m3/s).
As LNG is cooled to the point of liquefaction, cryogenic testing is also critical to ensure valve performance at actual operating conditions. At the manufacturers’ sites, valves are tested in line with the EN 13648-1 standard, using 100% pure nitrogen. This time, leak tightness at the outlet flange is measured according to API Standard 527 (Kellogg test)
Overcoming Supply Chain & Project Execution Challenges
LNG projects often involve complex logistical challenges, particularly when operating in remote locations with extreme environmental conditions. Harsh weather, supply chain disruptions and tight project timelines necessitate close collaboration between engineering, procurement and construction (EPC) contractors, OEM valve manufacturers and end users to ensure timely project execution.
For example, a major LNG plant operating in subzero ambient temperatures required the delivery of over 500 critical-service safety valves within a compressed timeline. By leveraging advanced manufacturing processes and in-house cryogenic testing facilities, the OEM manufacturer successfully met the project’s tech specifications while ensuring compliance with stringent safety standards. Approximately one-third of the valves were completed and delivered within a 22-week period, aligning with the installation and startup schedules.
In another instance, the manufacturer supplied a range of control valves for the receiving terminal and regasification
plant of the first LNG terminal of an Asian country. The scope included large-diameter butterfly valves for seawater flow regulation in the LNG vaporizers, cryogenic globe valves for LNG handling and high-pressure gas let-down valves. The successful execution of this project underscored the importance of technical expertise, manufacturing agility and robust supply chain management and led to the assignment of orders for cryogenically tested control valves, up to 16 inches in size, for similar LNG projects across the country.
Future Trends in LNG Valves
As the LNG market continues to expand, new challenges and opportunities are emerging in valve technology. The push for greater automation and digitalization is leading to the adoption of smart valve solutions equipped with sensors and predictive maintenance capabilities. These advancements enable operators to monitor valve performance in real-time, reducing unplanned downtime and improving overall system reliability.
Furthermore, the transition to hydrogen as a clean energy carrier is influencing the development of next-generation cryogenic valves. Since hydrogen must be stored at even lower temperatures than LNG, valve manufacturers are exploring new materials and sealing technologies to accommodate the properties of this emerging energy source.
The LNG industry presents challenges that demand innovative valve solutions to ensure safety, efficiency and environmental compliance. By leveraging advanced materials, cutting-edge design and manufacturing technologies and stringent testing methodologies, OEM valve manufacturers are playing a crucial role in supporting the industry’s evolving needs. As global energy demands shift, continued innovation in valve technology will remain essential to achieving sustainability goals and operational excellence in LNG applications.
References
Global Gas & LNG Market Outlook to 2035, McKinsey & Company.
Ursan, M. (2011), “What Is Boil-Off?” Brussels. November 3. unece.org/fileadmin/dam/trans/doc/2011/wp29grpe/lng_tf-02-06e.pdf