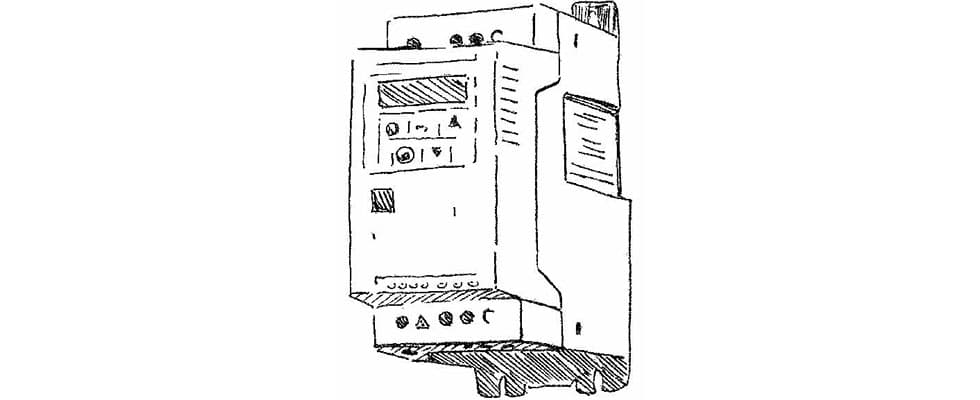
Variable frequency drives (VFDs) are used widely for pump control in a wide range of industries and applications—from drinking water supplies and wastewater to irrigation and large-scale industries using water during production processes.
VFD technology has made an impact on the water pumping industry by reducing energy and maintenance costs for end users. It can also improve pump reliability and extend equipment life.
The use of drives designed specifically for pump control can help achieve energy savings of 20 to 30 percent in some pump control applications.
Use a VFD for Pump Control
The demand for water can vary throughout a day or process depending on the application. For example, the demand for water in a hotel will be high in the morning and daytime, but low during the middle of the night.
It is the same in the water and wastewater treatment process—demand peaks in the morning and evening. In an industrial situation, the flow could alter throughout a specific application process. And yet, in many cases the water pumps are working at a constant maximum capacity regardless of demand.
Be Energy Efficient With Smart Pumping
By controlling the speed of a pump, or multiple pumps, the flow can be altered to suit the demand. This is done when the VFD varies the motor input frequency.
Some VFD manufacturers use intelligent technology that senses the demand for water and controls the water pump accordingly.
By doing this, the pump is never working at full capacity. This can considerably reduce energy use. It also can result in less wear and tear on the pump and any associated maintenance that might be required. As a result, this cuts downtime.
Some VFDs use technology that detects burst pipes and blockages. Again, this can prevent downtime or damage to the pump, system or property.
VFDs are often easy to maintain and service. Some use Bluetooth and Near Field Communication (NFC) technology to allow access via smartphones, computer or portable devices to set up, commission, monitor or update VFD parameters. This can also allow remote monitoring of drives used in the field, making it easier to predict problems as well as having real-time information.
Optimize Temperature & Energy Supply
A chain of gas stations in Pennsylvania had two fans supplying cold air 24 hours a day, regardless of demand. This placed pressure on the fans working at full capacity.
The introduction of VFD technology has seen a reduction in energy use of up to 30 percent. Two three-horsepower (hp) and two five-hp three-phase VFDs were installed to control the four fans. The drives use intelligent cascade technology that detects system air flow usage and controls the fans accordingly to maintain the perfect temperature for food and cold beverage products. When the outside temperature is low, it automatically reduces the number of fans required to ensure a consistent ambient.
Detect Demand With Intelligent Technology
The intelligent technology also allows more than one drive working together to ensure an optimized flow.
The first drive is the primary and the other three are secondaries. The primary controls and commands the secondaries with their speeds and run times. The system is controlled based on demand using the internal proportional-integral-derivative (PID) function. The output temperature is continuously measured and sent to the primary drive. The primary drive will then intelligently set the on and off condition and speed of all drives based on the internal PID functions.
The system is never under stress mechanically, ensuring savings on reduced wear and tear or downtime.
The temperature of the system is also secure. If a drive or fan is out of service, primary operation transfers to the next VFD in line. The drives also detect fan belt breakage and set off a system alarm to alert maintenance.