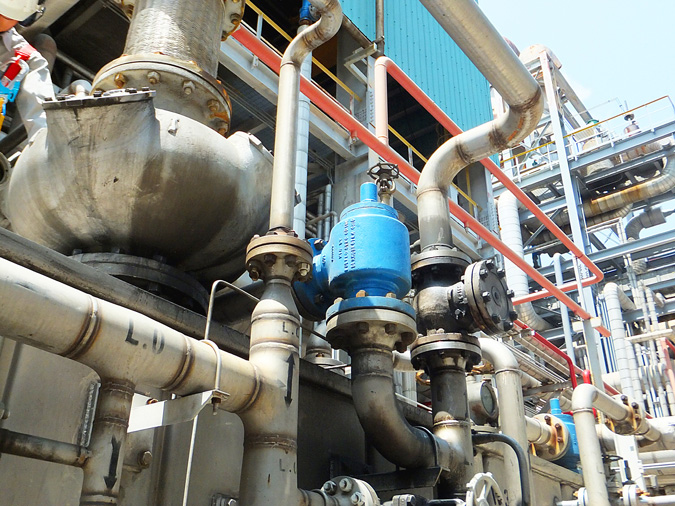
When selecting components for fluid systems used in oil and gas applications, the type of hydraulic valve chosen can make a critical difference in the consistent operation of that equipment. Whether installed to manage oil pressure to compressors or lubrication to bearings, guided piston valves offer certain flow and stability characteristics for reliable performance without chatter. Understanding the relative advantages of guided piston valves will ensure long service life of pumps and other oil and gas process equipment.
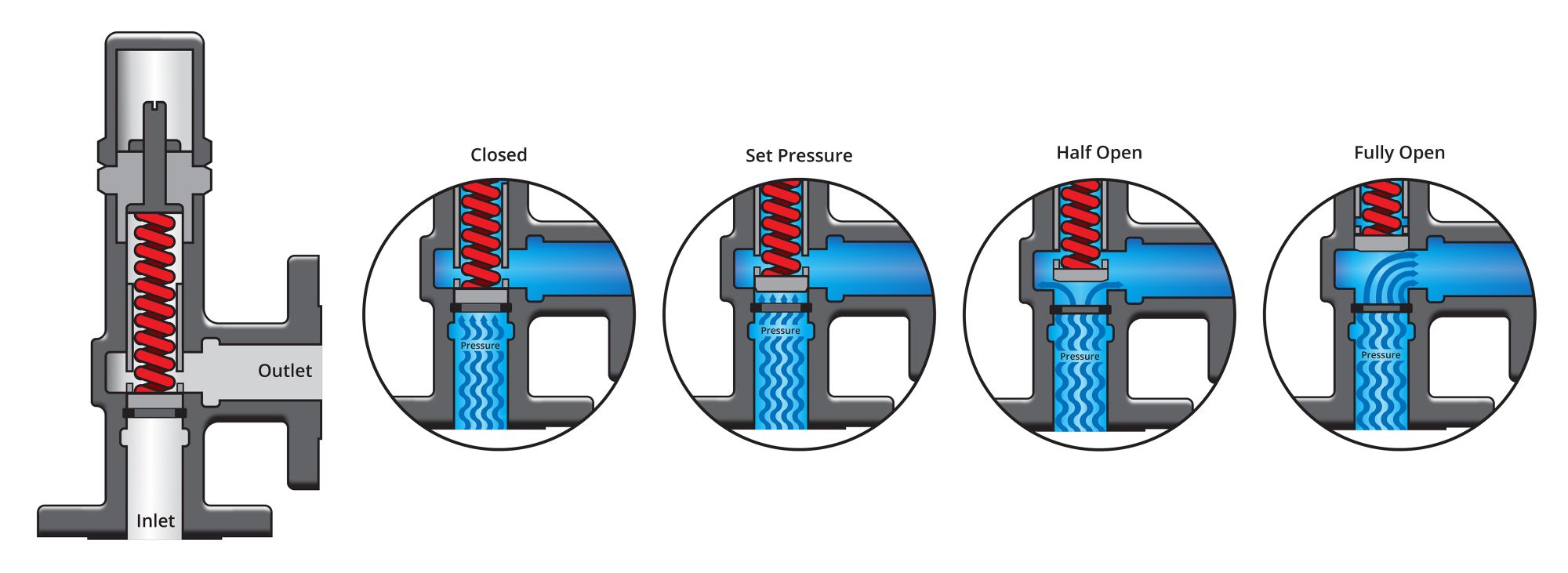
One advantage of guided piston valves is the provision of a constant line pressure unaffected by transient pressure surges. In every part of the oil and gas processing life cycle, from fracking rigs to refinery fill operations, there is potential for system pressure to fluctuate. An auxiliary pump activating to supply additional oil to motor fan bearings on a lubrication system, or a valve shutting once an oil drum is filled, can both alter the pressure up and down the line.
These fluctuations are hard on equipment, particularly pumps and mechanical seals. As pressure and friction build inside a pump, temperature rises and creates vapor that results in cavitation that can damage the impeller and casings. Increased temperatures also compromise the integrity of mechanical seals and bushings. This cracks and scores the seal’s face and burns up the seal’s elastomers. The culmination of this component damage is pump failure.
A pressure relief valve reduces strain on downstream equipment by mitigating this inevitable system pressure fluctuation. Guided piston valves are particularly suited to this type of pressure management. They reduce velocities through all but the controlling interface of the valve, thereby minimizing system power loss and even preventing system shutdown. The valves operate reliably at pressures as low as 3 pounds per square inch (psi) and as high as 1,000 psi and are, therefore, suited to a wide range of oil and gas equipment applications.
As a flow-modulating device, the pressure flow characteristics of a guided piston valve are different from spring loaded poppet or ball check valves. While a typical hydraulic valve has two operating settings—totally closed or fully open—a piston-guided valve fluctuates on a spring to maintain the set pressure. As pressure on the line increases, the valve opens a corresponding amount to maintain the set pressure. As pressure on the line decreases, the valve closes to the degree needed to maintain the set pressure. The valve returns to the closed position when the pressure on the line normalizes. Image 1 illustrates this self-modulating operation. The guided piston valve functions consistently and modulates at any degree of opening and closing. This operation does not require any external sensing or control systems for operation. The valve’s self-modulation is pressure actuated and self-powered. This modulation prevents pressure drops that might normally trigger low oil pressure alarms.
The simplicity of the guided piston valve’s mechanics results in reliable performance. With fewer moving parts, there are fewer opportunities for valve breakdown. These valves have long service life, even in extreme conditions.
Guided piston valves operate effectively with all types of liquids in the full range of viscosities, including hydraulic oils, water, solvents and chemicals. For equipment destined for outdoor use, temperature can play a large role. Lubricants thicken on cold days and become less viscous on warm days. Oxidation, moisture and ordinary wear can also contribute to changes in viscosity over time. The guided piston valve’s immunity to viscosity ensures consistent operation regardless of viscosity fluctuation. Guided piston valves can also be mounted in any position during installation, without affecting performance.
In almost all oil and gas settings, from offshore platforms to mobile fracking rigs, space is at a premium. The guided piston valve’s mounting flexibility, coupled with the ability to handle large flows without excessive bulk, enables more compact equipment footprints. This allows guided piston valves to be easily designed into original equipment or retrofit to replace underperforming valves.
A final benefit of the guided piston valve is its quiet operation. Ordinary direct acting relief valves can pound, squeal or chatter as they pop suddenly open or closed in response to transient pressure surges.
As the guided piston valve floats open and closed on a spring, it operates smoothly and quietly, not contributing any additional noise pollution to already loud jobsites.
Guided piston valves merit consideration for use in oil and gas applications. Their operational and performance advantages better protect downstream pumps and systems from ongoing damage. This protection prevents failure, downtime and the associated repair and operational costs.
Use Case: Tanker Unloading
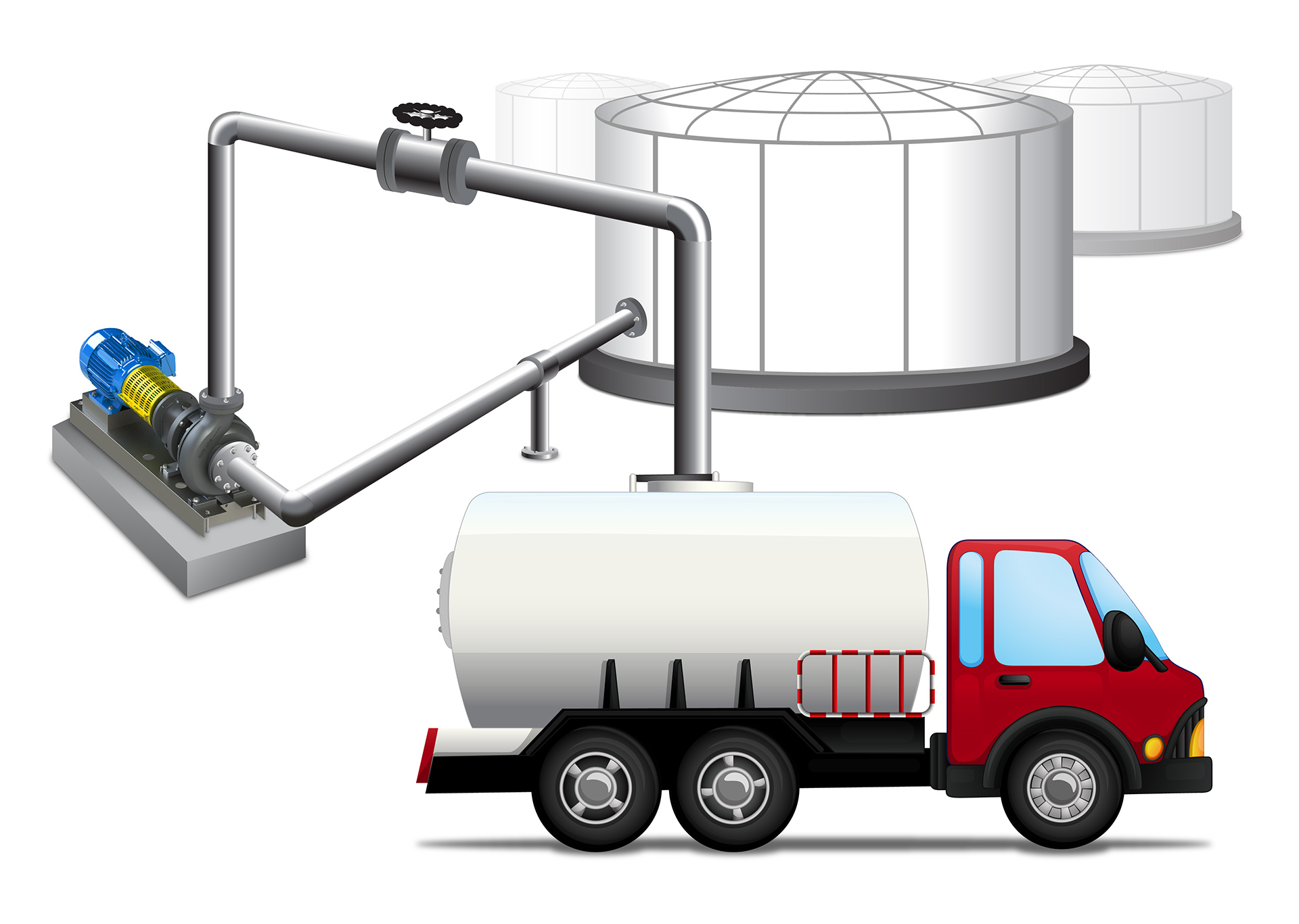
In Image 2, a typical truck loading process using either a centrifugal or positive displacement pump has a manual shutoff installed at the point of tanker loading. When the loading operation closes this valve without warning, considerable pressure builds in the line leading back to the pump, creating strain on the pump and risk for failure.
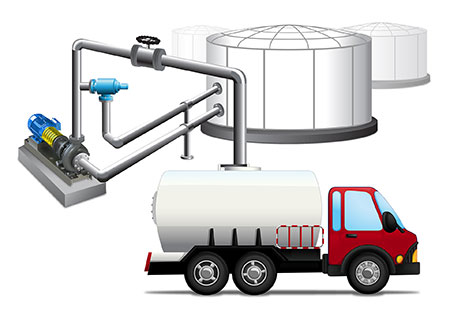
The solution is to add an external pressure relief valve to protect the pump and systems. The self-modulating guided piston valve is ideal for this type of installation as it requires no additional controls.
A new recycle line with a guided piston pressure relief valve is installed between the pump and the loading line. When the tanker truck is full and the loading valve is closed, the pressure back to the pump begins to build. The valve then activates automatically, diverting flow back to the tank and relieving pressure on the line to the pump.
When the next truck lines up and the valve is reopened, and the pressure on the line returns to normal, the pressure relief valve returns to the closed position automatically.
As this is a guided piston relief valve, the orientation of the valve does not impact the valve operation or set pressure. It can be mounted upright, sideways or even upside down—however space permits. This characteristic of the guided piston valve provides design flexibility in retrofitting problem processes.