The decline in oil prices has forced operators to produce oil more efficiently and cost-effectively—particularly offshore, where costs and breakeven points remain high. Over the last few years, a number of innovations have helped to improve efficiency. Sensors and communications technologies simplify maintenance. Smart assets such as drones lower labor costs and make it easier to inspect flaring towers and areas below deck. These innovations save money by helping operators detect anomalies and make repairs before the issues become costly. But other technologies in offshore environments remain unchanged and serve as a standard component, mainly because they are trusted and proven to perform critical tasks. One such technology is the metering pump, which delivers a wide range of chemicals to provide flow assurance and equipment integrity, as well as protection, for highly reliable oil and gas production. Hydraulically actuated diaphragm (HAD) metering pumps are widely embraced in the industry, being deployed on almost every major offshore platform in the Gulf of Mexico over the last 15-plus years including Atlantis, Thunder Horse, Shenandoah, Mad Dog and Olympus—and eventually Appomattox.
Selection Criteria
Each deepwater offshore operating environment has distinct requirements for selecting a metering pump. Flow rate: A common thread in these offshore environments is the depths at which each platform operates. Massive amounts of power are needed to deliver flow-assurance chemicals to the wellhead, which sits in depths often exceeding 6,000 feet, plus the additional 20,000 to 25,000 feet beyond the wellhead to where the oil and gas reserves remain below the seabed.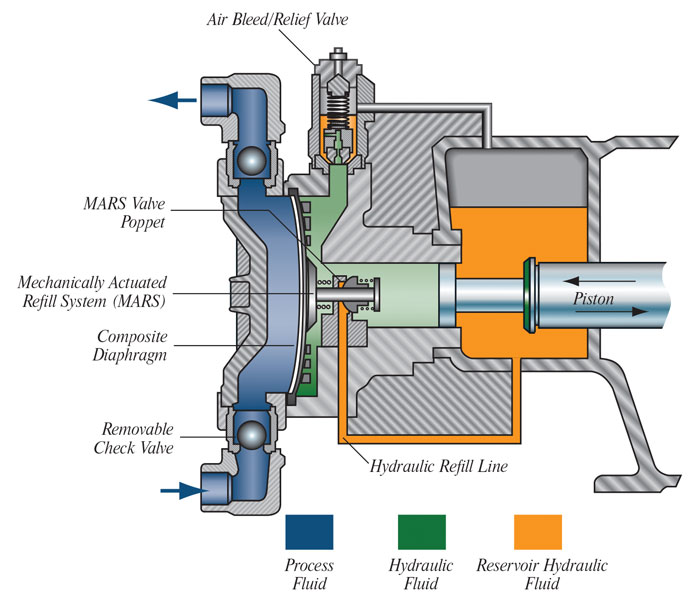
Setting the Design Standard
When operators started working in ultra-deep environments in the 1990s, very few metering pump companies had any experience addressing pressures exceeding even 10,000 psi. One of the limiting factors for pumping equipment was the diaphragm. It was understood that metal diaphragms were required to handle the required pressures, but pump manufacturers had yet to discover how to flex a metal diaphragm in a manner that could withstand the pressure without failing. Through innovative engineering and extensive trial and error with application-specific metal alloys, the HAD was developed that continues to set the standard today. The HAD acts as a barrier between the piston and the process fluid. The piston’s pumping motion is applied to hydraulic fluid, causing the diaphragm to flex back and forth with the piston’s reciprocating action. The HAD is designed to operate with equal pressure between the hydraulic and process fluids, eliminating diaphragm stress. This pressure-balanced design contributes to the unmatched longevity of HAD pumps.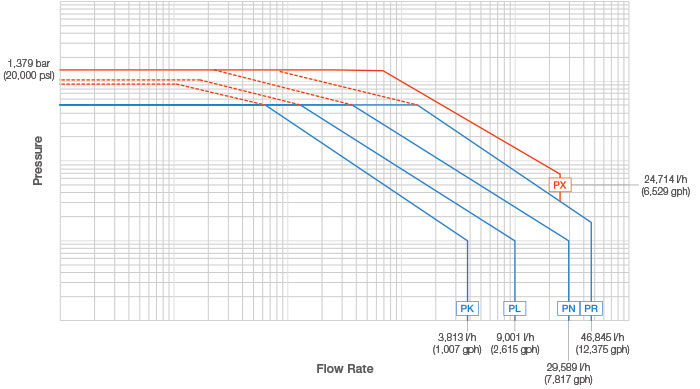
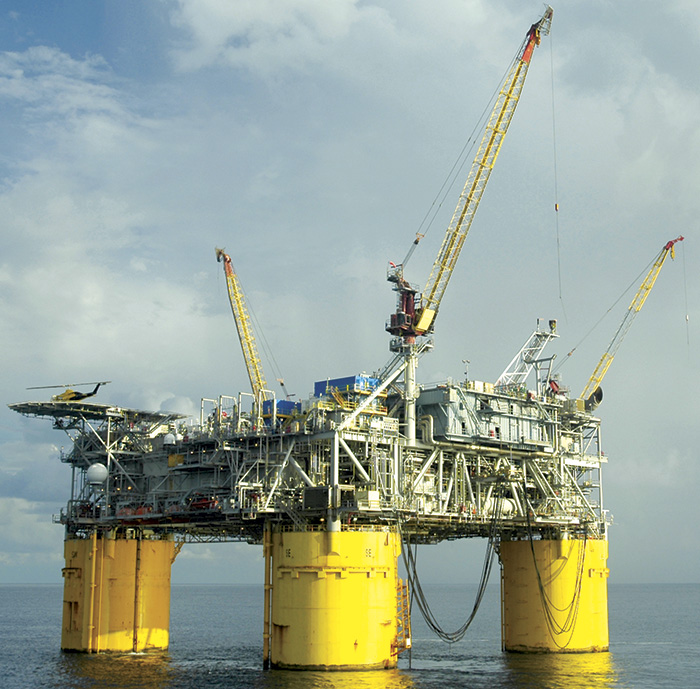