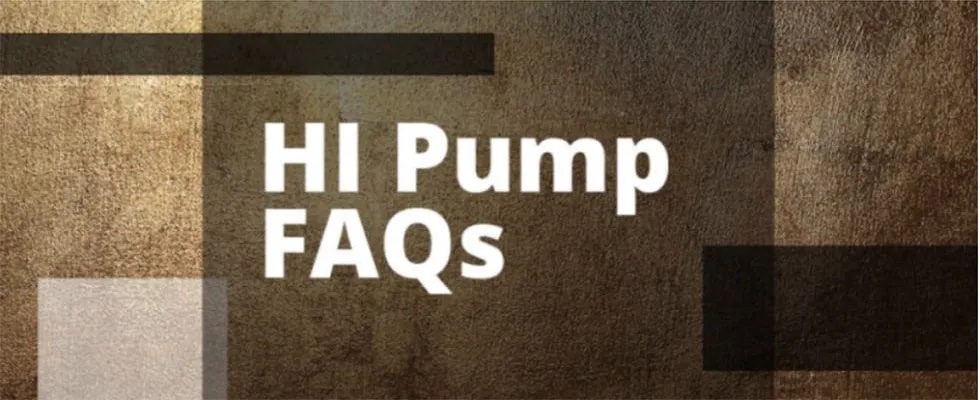
The impeller in a slurry pump is designed to optimize the passage of abrasive solids while considering erosive wear that will affect performance. Therefore, they are designed compared to more conventional impellers used with clear liquids. Both closed and semi-open impellers can be used for slurry applications. “Clearing” or “expelling” vanes on the impeller shroud(s) and close axial clearances are used to control leakage. Due to normal wear from slurry abrasion, the design incorporates a method to easily adjust the axial clearances. Close radial clearances cannot be easily adjusted externally and therefore will only be considered for low concentrations of fine slurries. Finally, an easy to overlook factor is impeller attachment. Impeller attachment methods vary by manufacturer and the severity of the service. For highly abrasive applications, the impeller attachment should be protected from wear to optimize the service life. This is often accomplished by an internally threaded connection, which protects the threaded area from the abrasive slurry.
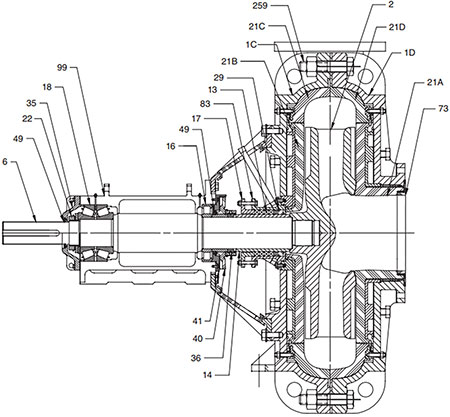
Image 1 depicts an overhung slurry pump with elastomer lined casing. Item 2 is the pump impeller. As discussed above, it has an internal threaded connection to the pump shaft and clearances are controlled axially between the liner (21A and 21B) and the impeller (2).
For more information on slurry pumps, refer to HI standard, Rotodynamic Centrifugal Slurry Pumps for Nomenclature, Definitions, Applications, and Operation (ANSI/HI 12.1-12.6) at pumps.org.