There is a reason thermoelectric (coal, nuclear or natural gas) power plants are located near rivers, lakes or oceans. It is because they need tremendous quantities of water to generate power. More than 90 percent of electricity generated globally comes from thermoelectric plants. These plants boil water by burning a fossil fuel (or using a nuclear reaction) to create steam that spins turbines. Steam must be cooled back into water before it can be reused to produce more electricity. Colder and cleaner water cools steam more effectively and allows for more efficient electricity generation. Legacy coal-fired plants, relying on once-through cooling processes, need about 30,000 gallons of water for every megawatt of electricity produced, and nuclear plants need even more. Modern natural gas combined cycle (NGCC) plants can produce the same megawatt of electricity with 5 percent as much water (which is still about 1,500 gallons per megawatt). Water quality is almost as important as quantity when it comes to plant efficiency. The turbidity of incoming water can vary depending on storms or man-made interactions, so incoming plant water must be treated before it can be used.
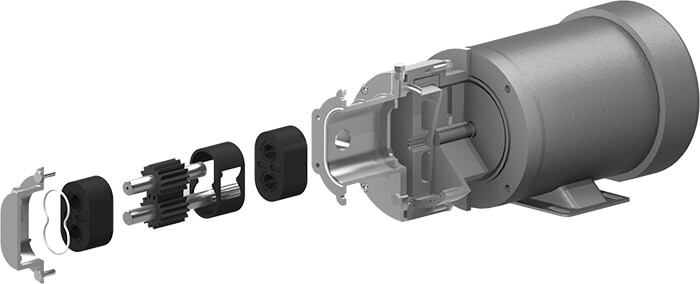
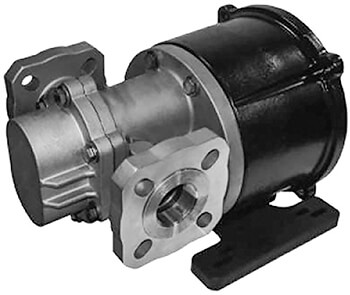
Requirements for Metering Pumps Used in Power Plants
The criteria for selecting metering pumps typically includes flow rates, pressures and corrosion resistance (depending on what chemicals are pumped). Although plant operators and the engineering, procurement and construction (EPC) firms that serve them have multiple options for pumping infrastructure, the most popular choices usually involve diaphragm or rotary gear pumps. In plants where American Petroleum Institute (API) requirements must be adhered to, diaphragm pumps are the preferred choice. Diaphragm pumps can also deliver +/- 0.5 percent accuracy, which is often required in chemical manufacturing processes or in refineries. But when it comes to water treatment applications in power plants, API standards (and the costs that come with meeting them) are usually not required. Accuracy levels of +/- 2 percent are generally acceptable for water treatment applications. In these cases, rotary gear pumps can provide the functionality needed at a fraction of the cost of hydraulically actuated diaphragm pumps. Rotary gear pumps also provide the following capabilities: Flexibility to accommodate flow and pressure requirements. The flow rates required for water treatment applications in power plants typically range from a few liters per hour (l/hour) to approximately 100 l/hour. Most water treatment processes are low pressure applications, ranging from less than 10 Bar, up to about 40 Bar. Gear pump lines feature numerous models that can accommodate any flow range, connection size and pressure requirements within these ranges. Construction materials. Rotary gear pumps are available in different materials, including polyvinylidene fluoride (PVDF) or 316-SS, to provide corrosion resistance against a wide range of acids, caustics, polymers, flocculants, resins, solvents and scale inhibitors that are needed for the treatment processes. Safety. Because exposure to chemicals such as chlorine gas can cause respiratory issues for employees, great care should be taken to ensure that leaks do not occur when dosing hazardous chemicals. Sealless gear pumps offer fewer points of failure because there are no leak points for harsh chemicals to damage the pump or the surrounding equipment. Streamlined maintenance. The simpler the design is, the easier a pump is to maintain. With just a few moving parts, a rotary gear pump’s front pull-out design facilitates easy access to the inner workings. This enables the pump to be repaired in place with one tool. This reduces downtime and eliminates the need to move the equipment to a repair shop, which in some plants can require separate personnel. Spare parts kits are readily available and include everything needed to return the pump to as-new condition. This gives plant operators greater flexibility to schedule maintenance between shifts, or whenever it is least disruptive to do so. Smaller footprint. Rotary gear pumps are compact in nature, and they do not require as many ancillary items as diaphragm pumps (such as pulsation dampeners), so the overall size of the equipment package can be reduced. Longevity and reliability. Chemicals such as sodium hypochlorite tend to off-gas when they come in contact with metal surfaces. But nonmetallic gear pumps feature a simple design that helps prevent off-gassing, which minimizes disruptions and helps to maximize uptime for water treatment operations. Accuracy. When used as a metering pump, rotary gear pumps can provide +/- 2 percent metering accuracy, and accuracies of 1 percent or better are achievable with a closed loop control system. This level of control is well within the range needed for pH and disinfection applications at power plants.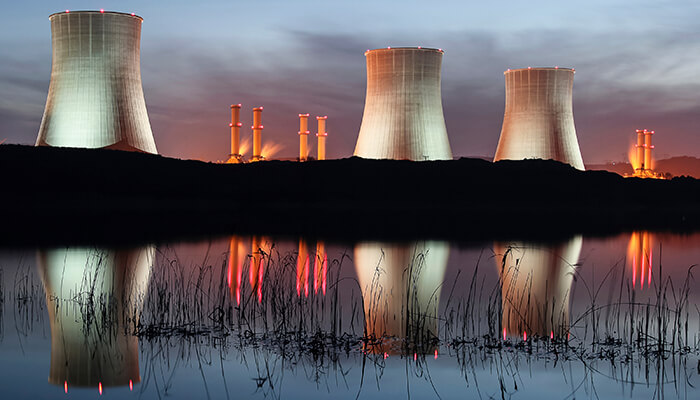