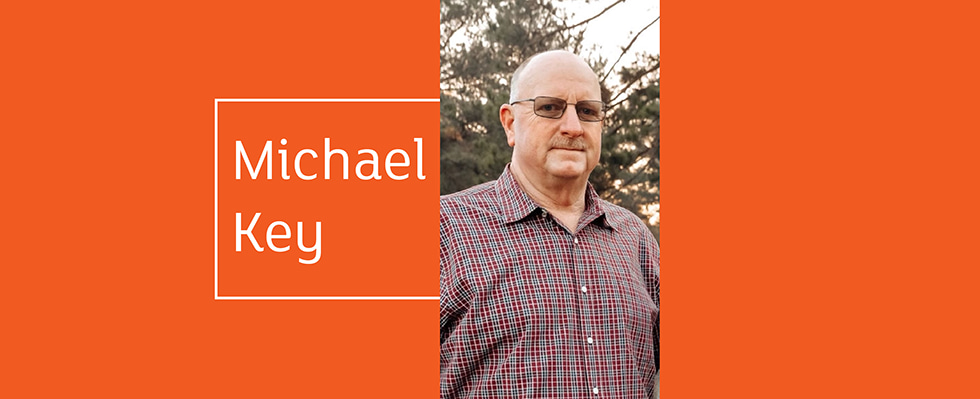
In an industrial plant environment, the mean time between repairs (MTBR) metric is the key measurement in assessing the reliability of American National Standards Institute (ANSI) centrifugal pumps. While most centrifugal pumps will run a minimum of 18 to 24 months, exceeding 24 months is the goal. The best-case scenario would be to perform regularly scheduled preventative maintenance while the pump is in service.
The implications of reliability extend beyond just the loss of production while the pump is out of service. Supply chain shortages and inflation have caused both an increase in the cost of the repair parts as well as much longer lead times on items that in past years were readily available.
ANSI centrifugal pumps break down for a variety of reasons. Overheating due to insufficient lubrication, cavitation when pressure inside the pump drops, corrosion when pumping corrosive liquids, misalignment of the pump shaft, mechanical wear and improper installation of pump components are just a few examples of what might cause a pump to break down.
When the pump fails, it will need to be removed from its foundation and taken to the pump shop for repairs. Once in the pump shop, the likely failed components will be the bearings, seals, impeller or the casing. All of these items could possibly be damaged.
To extend the MTBR of your ANSI centrifugal pumps, there are several measures reliability machinists can use. The most important thing is to make sure the pump is repaired properly before it leaves the pump shop. Meticulous care needs to be taken when reassembling and balancing. Look closely at the cover and make sure there has been no damage. Inspect the pump shaft thoroughly for any damage. Using a dial indicator, ensure the lift and thrust movements are to the pump’s specifications. You will also want to replace the mechanical seal, making sure to choose the correct seal for the pump as indicated. Make sure to lubricate the O-rings going on the shaft to prevent issues when applying the seal and cover back on the pump. Carefully inspect the impeller for damage. Impeller vanes can become sharp while in service. Many times, the impeller will need to be replaced. Reinstall the impeller and new gasket, making sure to use the proper tool for the job to ensure the impeller is tightened properly and not damaged.
Once back in the field, you will want to make sure the pump is properly bolted and the pump and motor are properly aligned. Regular maintenance such as lubrication and checking the foundation bolts are properly tightened can go a long way toward preventing future failures and extending pump life. Regular monitoring of the pump can identify problems early on.
Vibration analysis should be regularly performed, as pump vibration of any kind is deemed a problem. If you can visibly see vibration, you will need to shut down the pump and take it out of service. A handheld vibration mic may display a small problem that can wait. Most of the time, the vibration is caused by an internal problem, but you may just have to tighten the foundation bolts.
Operating the pump within its designed parameters, such as the flow rate and head pressure, can prevent the pump from overheating. If continuously pumping corrosive material, the impeller can become damaged. A fiberglass pump could be a better fit for that application.
Using the best quality of impellers and seals can improve the performance and life expectancy of the pump. Qualified machinists properly trained and certified will make certain the work is performed right.
ANSI centrifugal pump MTBR can certainly be extended when you properly repair, maintain, monitor and operate your ANSI centrifugal pumps with certified reliability professionals.