Although they have been around nearly as long as the oil industry itself, production additives—chemicals that help move crude through the flow stream faster—rarely receive more than a fleeting consideration. However, with cost pressures as well as health, safety and environmental (HSE) concerns on the rise, oilfield and refinery professionals are realizing the benefits of additives. This demand is driving development of “greener,” more cost-effective formulations. Additives have contributed to every major industry milestone during the last 150 years, from the distillation of kerosene in the mid-1800s to the critical streamlining of crude movement through pipelines in Algeria, Alaska, Canada and Russia in the 70s and 80s. Many early indicators show a recognized need for additives that could help turn crude oil into usable products for profit. The reason for this is simple: Crude is difficult to extract, transport and refine. The oil is under extreme pressure in its natural state, and it is often just one component in a hot, roiling mixture of gases, saltwater and other substances. Difficulties continue as the oil moves out of the reservoir. When crude oil cools in pipes, pipelines or tanks, its organic solvents evaporate, which causes increased viscosity that results in significant extraction and transport problems. These factors have driven the development and evolution of production additives, or specialty chemicals. Some of these chemicals, for example, work to alter the thixotropic properties of the oil to create a lower kinematic viscosity in a process called fluidification. Others are formulated to maintain a strict hydrophilic-lipophilic balance to aid in demulsification. Chemical additives can be applied to any point in the process at which the crude’s flow slows—points often called areas of “parasitic loss.” These capabilities can enhance pump performance and reduce downtime during both the extraction and refining processes.
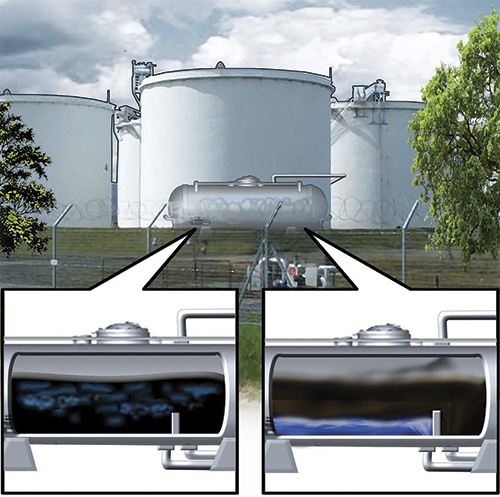