Magnetic drive pumps are now being applied to a wide variety of applications where they face new demands and must respond to new trends in the marketplace.
Trends
While these pumps are still firmly entrenched in corrosive chemical applications and applications involving difficult to seal fluids, magnetic drive pumps are being challenged to be more efficient and have enhanced characteristics, such as dry running capabilities and corrosion resistance in the most severe conditions - all under the specter of higher material costs.
Also, more manufacturers now produce magnetic drive technology as it becomes accepted in the marketplace. These competitors are expanding their offerings - more options, sizes, and types - to match market growth and answer the evolving trends in emissions regulation and so-called green technology.
The regulation of emissions has been, and continues to be, a market driver for mag-drive pumps caused by safety statutes or simple economics. For example, a recent scrubber application for mag-drives resulted from the increased concentration of hydrofluoric acid in a scrubber system. At lower concentrations, the cost of wastewater treatment becomes burdensome, so the concentration is allowed to increase to a point where a mag-drive pump must be applied.
This general increase in the concentration of process streams, due to emission control across many industries, has greatly broadened the market for mag-drive pumps and resulted in expanded material offerings for them. For this reason, we have seen a trend towards more corrosion resistant resins and more fully fluorinated elastomer sealing elements.
Green technology is opening up markets for mag-drive pumps in some methods of producing biodiesel fuels, where mixtures of caustics and solvents create difficulties in sealing. Ethanol production also creates applications for acids used in functions such as pH trim and clean-in-place systems.
Another trend is the application of self-priming magnetic drive pumps to avoid the use of bulkhead fittings in the sides of storage tanks, which can cause of chemical spills. This type of mag-drive pump has been used in railroad and tank car unloading for many years, but smaller versions of mag-drive self priming pumps are now being applied similarly to such diverse uses as caustic pH trim in mine runoff ponds, plating tanks, and day and storage tanks at water treatment facilities. An illustration of such a self-priming mag-drive pump is shown in Figure 1.
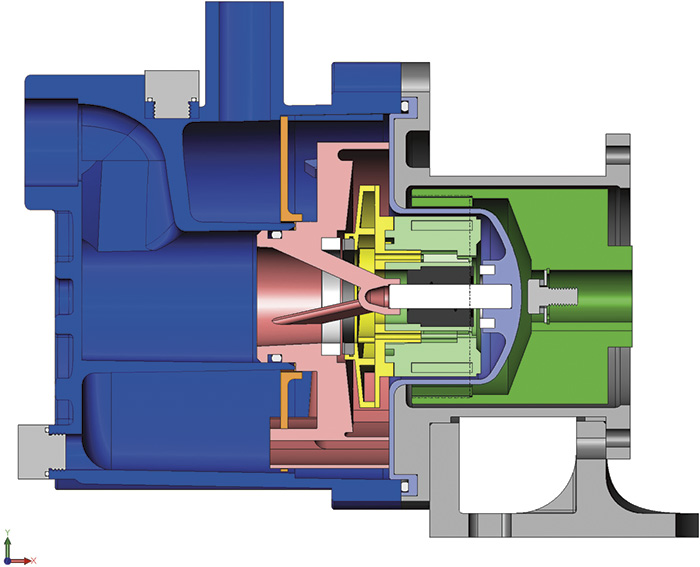
Challenges
One of the main challenges to magnetic drive pumps is the corrosion resistance of the magnetic elements themselves - both internal and external to the wet end. While several types of magnets are used, including ceramic and Samarium-Cobalt, most magnetic couplings in mag-drive pumps utilize Neodymium-Iron-Boron magnets due to their high maximum energy product.
Neodymium, however, has little corrosion resistance. The inner magnets are typically hermetically sealed within injection molded plastic resin. These resins must be tough to resist cracking and readily weldable. Some drives are now being designed with unfilled polymers, and finite-element based flow modeling of the mold process is being used to optimize the part, mold and weld joint designs. Figure 2 is an illustration of the plastic flow within the injection mold of a mag-drive pump inner drive.
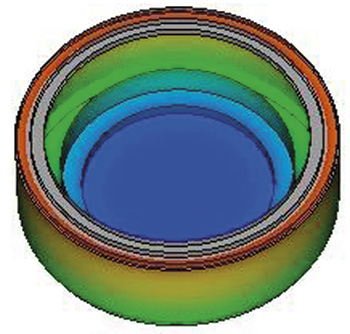
Outer drive magnets, while not being wetted, are subject to fumes and wet conditions. As such, they are often Nickel plated, painted with epoxy or other paints, or encased in a thin stainless steel shell. Magnet manufacturers are responding to the Neodymium corrosion problem by offering enhanced corrosion-resistant grades - the "HAST" (highly accelerated stress test) grades. Motor adapters sealed with o-rings (see Figure 3) are also available on some models of mag-drive pumps.
Because the first magnetic drive pumps were metallic in construction and produced efficiency-robbing eddy currents within the barrier, a lingering perception persists that all magnetic drive pumps are less efficient than packed or sealed pumps. This is not true.
Any permanent magnetic drive pump with a barrier made of material that is not electrically conducting will not produce eddy currents and can be equally efficient to any pump design of similar size and specific speed. With energy costs soaring, the marketplace is definitely trending towards evaluating pump efficiency carefully, as well as applying pumps by controlling speed rather than system friction to vary flow rate in order to increase overall efficiency. Many magnetic drive pumps can fully and equally participate in this evaluation and be successful.
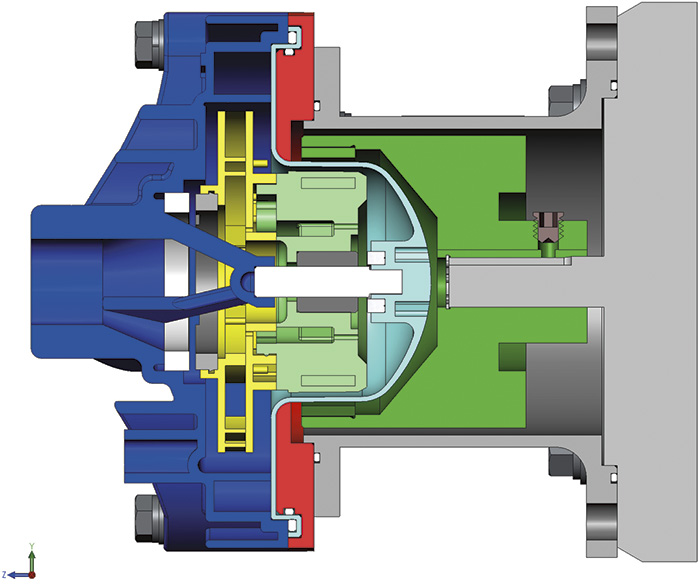
The ability for the magnetic drive rotor to run dry - that is, for the bushing or bearing support system of the inner rotor to continue to operate without malfunction in the absence of any pumped fluid to provide lubrication and heat removal - continues to be a focus of many mag-drive pump manufacturers.
Be it proprietary coating technology or careful material selection of bushing and shaft materials, many manufacturers of magnetic drive pumps contrive to offer products with dry running capabilities. This greatly expands the versatility and reliability of mag-drive pumps into marginal applications and systems that may be prone to process upsets.
While increasing prices of raw materials affect manufacturers of all types of pumps, magnetic drive pumps have an extra cost burden - those rare earth materials that comprise the permanent magnets of which their drives are made. These materials come almost exclusively from China. There are several reasons for the increasing cost, including production and export quota problems along with the ever-expanding market for Neodymium material in the automotive and consumer electronics industries. The result has been double digit price increases in the cost of Neodymium, with no end in sight.
This gives magnetic pump designers a strong incentive to get the most out of every gram of this material. To help alleviate the cost somewhat, magnet producers offer a wide and growing variety of Neodymium magnet grades that combine varying levels of saturation magnetism and coercivity. They also offer Neodymium grades that retain magnetic properties up to 350-deg F.
Changes
While the challenges to applying magnetic drive pumps are many and varied, some formidable design tools are available to help meet those challenges. Finite element software design tools are the foremost change in magnetic drive pump design over the past several years and can affect every aspect of the design process and almost every component.
From CFD for hydraulic and mold design to FEA for structural analysis and magnetic flux, these tools are changing the way magnetic drive pumps are designed. As a result, the pump user community has a broader selection than ever for choosing mag-drive pumps for the many pumping applications for which they are suited.
Pumps & Systems, April 2007