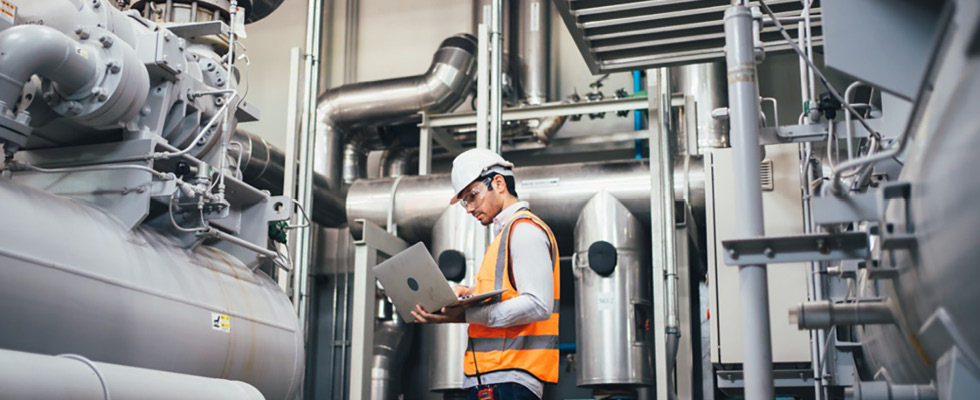
State of the Industry
For decades, the global pump industry has seen persistent complacency in a largely conservative market with no real disruption to pump operational practices. Today, the industry continues to face a number of challenges where pump manufacturers are struggling with slow growth. Products have become commodities and efficiency, quality and reliability levels have become standardized across brands. Still:
Millions of unconnected pumps, drives and controllers are sold annually. Each machine generates massive amounts of data with significant value—and eventually, every single one of the machines will be intelligent (connected). The question is, who owns the data output from the future equipment? Will it be the company holding the data?
There is an increasing fear among pump manufacturer executives that Internet of Things (IoT) will disrupt the current market structures. Figuring out the business model and why IoT is valuable is not a cookie-cutter model. This framework differs from product to product and application to application.
A lack of action by both pump OEMs and their clients in leveraging IoT for critical infrastructure (water utility, process industries, food and beverage, power and heating) means they lack basic insights into the state of their equipment. Every single day, companies in these sectors consume billions of gallons of water that costs billions of dollars in energy, treatment and equipment repairs. By placing sensors on industrial water pumps and connecting them to the internet, the flow volume can be optimized to generate thousands of dollars in energy savings from just one standard 100 horsepower industrial pump.
To capitalize on a connected pump market anticipated to reach $77.2 billion by 2033,1 there needs to be a greater sense of urgency toward digitalization of assets. Pump manufacturers stand to gain tools, methods and insights to future-proof their products and thereby offer water system operators a remote ability to analyze and control the flow and quality of water. A market motion to accelerate the transition toward IoT and digital solutions can improve efficiency and increase uptime through preventive maintenance. By providing automated alerts based on system optimization, IoT allows manufacturers and their clients to profit from full-time monitoring and control that reduces:
- Downtime/runtime
- Wear and tear
- Water consumption
- Energy consumption
Connectivity and the data generated also allows manufacturers to improve products and create stronger client relationships. And since the digital transformation gap is widening for pump manufacturers, it is imperative to digitize and differentiate from
conservative competition.
Challenges
Some corporate innovators in pumps, large and small, have been hard at work in anticipation of the need to digitize product lines. Nevertheless, integration challenges remain. The adoption rate of digital technologies is long, mainly due to uncertainty in the business model. Even though pump OEMs like the financial potential of a subscription-based business, they struggle to price it out correctly or create a meaningful business model supporting software as a service (SaaS).
Additionally, IoT connectivity does not sell itself by virtue of its novelty. It is important that the adoption of technology is secured by a strong value proposition. Pump manufacturers often go to market without a clear value proposition and thereby risk clients not understanding how an IoT product solves their problems or addresses their needs.
There are six areas that are critical to success and must be considered when doing a “make vs. buy” analysis for an end-to-end IoT connectivity solution.
Hardware types and changes
- Firmware versions
- Variations for cellular, satellite, Bluetooth and other wireless technologies
- Rapid technology cycles
- System changes as a result of the above
Integration with equipment
- Control panels
- Bus networks
- Harnesses
- Installation kits for factory or field
- Certifications from the Federal Communications Commission (FCC) to networks
- Securing the hardware
- System changes as a result of the above
Carrier management
- Contracts and private access point names (APNs) with each carrier
- Activation/deactivation processes and tools
- Roaming and toggling issue resolution
Software apps and service
- Platform feature management, including apps
- The latest trends in web interface design (UI)
- Changes to the rest of the system due to changes in these software features
Gateways
- Unique gateways for each device
- Raw data decoding, filtering, scaling and parsing
- Remote updates as devices change
- Diagnostics that include devices and application programming interfaces (APIs)
- Billing reconciliation
- International coverage
- Certification
- Hardware and integration changes as a result of the above
- Encryption and data security
- Changes to the above due to changes in hardware and software functionality, and vice versa
Data center management
- Class A data center with biometric security
- Redundant connections to each wireless carrier
- Inconsistent external data sources
- Data architecture, including warehousing and analytic cubes
- System and network monitoring
The biggest challenge for companies that would like to undertake digital transformation is the speed at which technology moves. Pump manufacturers that decide to invest in “build it yourself” must be cognizant of the constant change of the technology, then become experts in every aspect of the technology. And even then, the muscle memory of the company has to change from long research and development cycles to agile development. With all these limiting factors in mind, it is advisable for pump OEMs not to risk complacency and the slowness of in-house IoT development.
Integration
It is time to tackle these difficulties and speed up IoT innovation in the pump evolution. To achieve this, there needs to be an endorsement of digital adoption for products by company management. Additionally, management needs to put in place a dedicated IoT team to secure successful implementation—particularly in larger corporations. Putting such a team together is a big investment in resources and time, and especially for medium or smaller manufacturers, it can be hard to take on the cost and risk associated with such an investment, not to mention attract the right talent. The solution to this can be to partner with an external technology company to help get things off the ground at a limited risk. It is not unheard of for product and pump engineers to conflict with innovation “not invented in-house” versus using expert IoT connectivity external providers, which work with higher momentum and less bureaucracy. Only top management can remove those roadblocks.
Commercial Benefits
As mentioned previously, manufacturers gather insights on equipment performance, run hours, start/stops, condition monitoring, etc. Connecting pumps, drives, controllers and other industrial equipment will enable industrial pump OEM clients to explore new business opportunities through data aggregation, including, but not limited to:
- Distribution channel modifications
- Alternative and new business models and service offerings (parts, service, after sales, recurring revenue, etc.)
- Optimized sales, branding and marketing functions.
When a SaaS model has been adopted, a pump manufacturer has access to the latest technology and future software updates, meaning the solution is forward-compatible. Everyone involved in the business model benefits from the recurring revenue, and end users receive the latest tech and insights into their equipment’s behavior.
Adding recurring SaaS revenue is a very tangible part of the value capture. But the value of the full commercial benefits opens up entirely new opportunities for growth in the future, opportunities that simply are not available without embracing IoT and digitalization.
IoT connectivity for pump manufacturers is a profitable and strategic opportunity to reinvigorate the industry. Realizing this potential in the pump markets should be a top priority for all industrial pump companies aiming to remain viable against competitors—and to extract value and obtain insights from machine health monitoring data performance, uptime, user satisfaction and support. The challenges to realizing this value are substantial, but rather than going at it alone, choosing the right partner to help overcome some or all of the challenges can be the first step toward success.
References
persistencemarketresearch.com/market-research/water-pump-market.asp