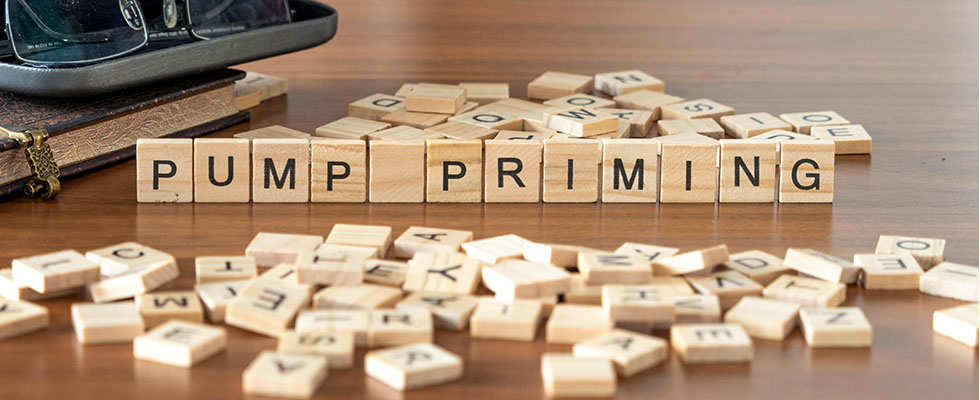
In my June 2022 column about high temperature pump applications, I stated/implied several times that heat is a property of the material. An observant and knowledgeable reader reminded this old engineer that heat is technically not a property and is simply energy in transition. Heat is a process/path function. My years of experience with steam turbines and the steam tables should have reminded me, so apologies to Mr. Richard Mollier. For those curious souls seeking to further understand, please look up the definition of heat, enthalpy and entropy.
I am frequently solicited by pump users to solve field problems. In a high percentage of cases, the root cause is located on the suction side of the pump. I have written numerous pump system (suction side) related columns on net positive suction head (NPSH), critical submergence and other common field issues, including self-priming pumps. Spurred by recent issues, I decided to devote more time to further examining self-priming issues.
Primed
What does it mean when someone states the pump is primed? The simple definition is that both the pump and its associated suction line are completely full of liquid. Further, there are no significant amounts of air, vapor or other gases in the suction system as these vapors and non-condensable gases have been removed by the priming process. Technically, a self-priming pump can be deemed “primed” but not fully primed if the priming chamber is full but the casing and suction line are not.
A centrifugal pump can be primed by many different means, and there are both internal and external methods to accomplish the evolution. This column will focus on self-priming pumps which is an internal method.
All Pumps Are Not Created Equal
I will address only centrifugal pumps in the self-priming category, but first I will make a few generic comments about positive displacement (PD) pumps. Essentially all positive displacement pumps are, in principle, self-priming by design. Consequently, priming issues are not as prevalent in that world except when the pump is operated dry. Albeit, there may be priming issues with PD pumps, but the magnitude is insignificant by comparison to centrifugal pump issues.
As a simplified example, for a PD pump system, the pressure differential between the suction source and the pump is strong enough to move multiphase fluid combinations of air, vapor, gases and liquid in the suction line and through the pump. The PD pump has the capability to handle dual phase fluids, while most centrifugal pumps do not. My statement assumes that the system is properly designed, the suction line has no ingress leaks and the pump is in good condition.
In the case of centrifugal units, the pump by itself cannot overcome the amount of energy required to move all of the air, vapor and gases along the suction pipe and through the pump.
As I have stated in past columns, centrifugal pumps are not compressors. A simplistic way to view this problem is that water is approximately 800 times denser than air. Consequently the pump would have to work 800 times harder and/or longer to move air as opposed to liquid. (At sea level, 68 F water is 784 times denser than air.)
Centrifugal Pumps Do Not Suck the Liquid Into the Pump
A suction lift simply means the maximum level of the liquid to be pumped is physically below the centerline of the pump impeller. Most centrifugal pumps can operate with a suction lift if they are primed first.
Contrary to urban myths and colloquial expressions, centrifugal pumps are not capable of “sucking” liquid from a lower elevation up to the level of the pump. I will concede that an operating pump does create a small differential pressure (a slight vacuum perhaps?) in the vicinity of the impeller eye. To a lesser degree, we should also understand that liquids do not possess significant tensile strength (compared to solids); therefore, the impeller can neither grab onto nor pull the liquid. Some external source of energy must work in concert with the pump to actually push (not lift or suck) the liquid into the pump. In an open system, the required external energy is typically supplied by the surrounding atmospheric pressure. Because we are relying on atmospheric pressure, it is important to understand that the amount of energy available is neither overly abundant nor constant. Atmospheric pressure will change with the barometric pressure (weather), and more importantly, it will change with the elevation above sea level. There are rare instances where atmospheric pressure will be higher than 14.7 pounds per square inch absolute (psia) because the site is below sea level (two famous examples are Death Valley in California and the Dead Sea on the Israel/Jordan border).
In a Perfect World
If there was no friction or vapor pressure effects in the pump system, we could theoretically lift water to the height of the equivalent surrounding atmospheric pressure. For example, at sea level, the atmospheric pressure would approach 14.7 psia (actual 14.696 lbs.-force per square inch). Converted to feet of head, 14.7 psia would be approximately 34 feet (assume water at a specific gravity of 1.0 and therefore 14.7 X 2.31 = 33.957 ft ≈ 34).
We don’t live in a perfect world, and so friction and vapor pressure will manifest as negative factors that further reduce the maximum achievable lift. Even for a cold-water pump located at sea level, you will probably have serious performance issues if your system lift exceeds 26 feet or more.
For more information and details on maximum lift, see past articles on this subject.
- (October 2021): pumpsandsystems.com/rethinking-npsh-matrix
- (September 2015): pumpsandsystems.com/centrifugal-pumps/10-common-self-priming-pump-issues
Priming Time
I am frequently asked how long it should take for a self-priming pump to prime. My sardonic but accurate answer is that it depends. Normally I tell people that priming four to five minutes is that length of time when you need to start asking, “What is wrong?” but also realize that some systems may take a little longer due to extenuating factors that include liquid temperature, viscosity, marginally high static lift, NPSH available (NPSHa), critical submergence, system integrity and overall pump mechanical condition. It is also important to understand that it takes longer for a pump to prime the system if it was initially full of air versus full of liquid. Note: The pump casing was primed but the suction pipe was not. If you have nowhere else to start your estimate, I know some experienced field people will use a thumb rule of 25 seconds per foot of suction pipe as a rough guideline. Pump manufacturers, experienced engineers and industry best practices will always advise you to locate the self-primer pump as close to the suction source as possible. The main reason for the close proximity is to reduce the priming time.
The next consideration is suction pipe diameter. For most pump applications, you should select a pipe diameter at least one size larger than the pump suction. This criterion is not always true for pumps on a lift situation because, again, the goal is to reduce the priming time. Granted, friction factors, NPSHa and best practice designs/axioms for maximum suction line velocity may dictate the larger pipe size. These additional factors will need to be evaluated on a case-by-case basis and compared to the estimated priming time for the lift application. I am 100% confident the suction pipe size should never be smaller than the pump suction nozzle on any pump. Minimizing both the length and diameter of the suction line reduces the air volume in the line. The smaller the air volume, the less time required to remove it during the priming process.
The suction pipe contains some volume of air “x” that must be removed for the pump to be primed and subsequently operate satisfactorily. Harking back to high school geometry class, you will remember that the volume of a cylinder is easy to calculate. The volume of a cylinder is equal to pi (π or 3.14159) times the radius squared, times the height. In this case, our cylinder is actually a pipe, so the cylinder height simply becomes the length of the pipe. Be careful to use the internal diameter of the pipe for better accuracy. Use the full length—not just the vertical distance (static head)—and be careful to watch your units. It is an easy and common mistake to state the radius in inches and the length in feet.
Don’t Wait Too Long
(Note this section is an abridged excerpt from my October 2021 column)
What’s the big deal with priming time?
First concern: The lubrication of the mechanical seal faces is paramount to the health of the seal and overall successful operation of the pump. If the pump is running without liquid (lubrication) the seal faces will be destroyed in a New York minute (fast). If the pump has a packed stuffing box, then the packing is operating dry, and it too will fail quickly. Whether your pump has packing or a mechanical seal, if it fails outside, air will leak into the system, and the pump will not prime.
Most self-priming pump OEMs design the position of the seal chamber to be automatically flooded (default by position) with product and/or filled with a compatible fluid (e.g. oil) to preclude dry operation during the priming process. However, appreciate that the manufacturer expects the priming evolution to be a short period of time. For self-primers with packed stuffing boxes, it is important to have an externally sourced flush or alternative lubrication method during the priming period. Check with the manufacturer for its advice. For example, some pumps have a grease injection port at the stuffing box to be utilized only during the priming process.
Second concern: During the priming process, the water in the priming cavity (casing or ancillary chamber) is being recirculated and churned by the impeller. This shearing action adds heat and increases the liquid temperature
rather quickly.
It is difficult to accurately calculate how fast the liquid temperature will rise for your specific installation as there are many factors involved, but we do know that the aggregate of horsepower and speed are major factors. It is important to note that pumps operating at 3,550 rotations per minute (rpm) will heat the liquid eight to
10 times faster than at 1,750 rpm.
On the higher-speed pumps, it is not uncommon for the liquid in the mechanical seal chamber/stuffing box to heat up at a rate of 40 to 50 degrees a minute. Some of that heat will be dissipated to ambient, but the salient point
is that the liquid does heat rather quickly which also changes the vapor pressure. As the liquid surrounding the mechanical seal heats up, it can easily flash to vapor. Note: Not all mechanical seals are subjected to this seal chamber situation as described, and it depends on the manufacturer, model and design.
Meanwhile, back in the casing/priming chamber, the temperature and vapor pressure will also increase rapidly. Consequently, the risk/probability of flashing the liquid in the priming chamber also increases. The ultimate goal is to prime the pump before you flash the liquid.
Calculating Priming Time
To calculate the estimated priming time for your unique system, you can request assistance from the pump manufacturer.
Prior to contacting the OEM, you will first need to know the following information:
- maximum static lift: This is the vertical distance from the liquid surface to the pump impeller centerline, worse case.
- total length of the suction piping
- nominal diameter of the suction pipe, materials of construction and schedule
- summation of pipe friction factors such as elbows, valves
- and filter/strainers
- pump model and size plus the actual impeller diameter
- vapor pressure: If you know what the liquid is and the temperature, this value can be obtained from reference sources. Vapor pressure is normally stated in absolute terms.
- specific gravity for the liquid at the expected pumping temperature
- NPSHa (above information will be required)
In any open system, using a self-priming pump in a lift application, vapor pressure, friction, static lift and time are not your friends. You do not have an infinite amount of available positive energy in your arsenal to combat them.
Your only allies in the quest for a properly primed pump is absolute pressure and minimizing the time of the priming evolution. Design the system to have short priming times by placing the pump near the source and size the suction
pipe properly.
In my next column, I will run through an example of prime time calculation and offer some tips for a trouble-free system.
Read part 2 here.