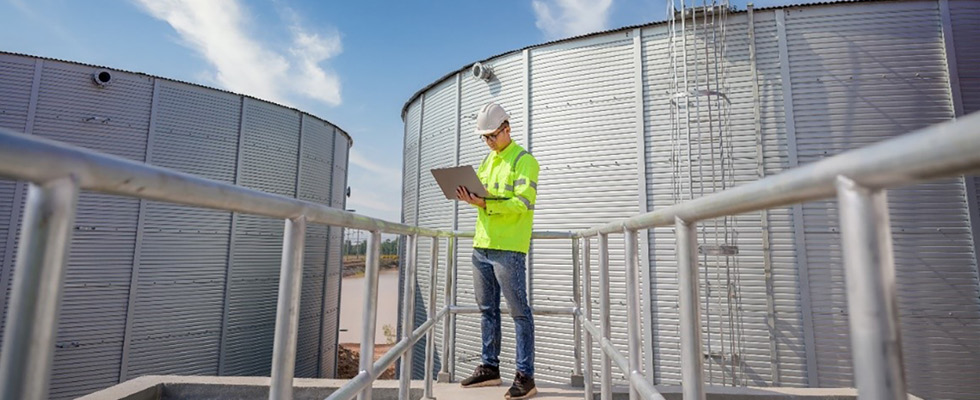
Every facility wants to operate as efficiently and safely as possible. Remote monitoring reduces the amount of in-person troubleshooting, testing and maintenance needed, leading to cost savings, extended equipment life span and increased uptime. Remote condition monitoring may be a solution for employees looking to keep equipment running without unplanned downtime, make productivity improvements and increase safety.
Benefits of Remote Monitoring
One obvious benefit of remote monitoring is its ability to provide real-time data, enabling oversight and analysis of systems and equipment without anyone needing to physically be on-site. It makes it easier to monitor many devices in multiple locations across an entire operation, even when at different sites. Remote monitoring can indicate potential problems in equipment and alert personnel immediately when equipment deviates from standard operating range, indicating an issue. This allows problems to be addressed immediately, so they can be corrected before operations, productivity and safety are impacted.
Real-time data and notifications not only help detect problems earlier, they also help increase uptime. There is no need to wait on maintenance personnel to travel to the location and troubleshoot. Many issues can be addressed off-site, and if in-person work is required, robust data insights collected from all monitored assets provide a clearer picture of where the issue lies. This helps avoid major equipment damage and optimize production stops for maintenance, shortening downtime.
of ABB)
With remote monitoring, maintenance teams save time when fixing troublesome areas and can also better plan for preventative maintenance to occur at a convenient time, avoiding unexpected downtime. Because the health of equipment is more easily tracked, better preparation is possible. A planned shutdown can occur, and an optimized maintenance schedule can be built. Since remote condition monitoring can be designed to proactively alert users to potential problems so unplanned downtime can be prevented, it also helps improve operational reliability and efficiency.
What to Remotely Monitor
Ideally, remote monitoring would take place across the entire powertrain (motor, drive and pump) to help provide a holistic picture of the state of equipment. By seeing the status of different assets, a full picture of the operation is available, allowing for targeted and immediate responses. Monitoring the entire powertrain, including motor, drive and pump, can help determine the best parameters to track for efficient and reliable operation of the system. This keeps the operation more efficient, predictable and safe.
If full monitoring is not possible, it is best to start by monitoring the most critical equipment and processes. Since remote monitoring is easily scalable, monitoring can be added to additional assets in the future or existing assets. Also consider remote monitoring in safety-critical applications and locations that pose greater safety risks and lengthy visits
to access.
Remote monitoring solutions in the market also provide new functionalities and customized features that can meet specific site requirements, including system integration and visibility across the shaft line and whole operation (product lines, manufacturing chain, etc.). Remote monitoring data can be compiled into dashboards, allowing a user to drill into details and easily see any anomalies in performance. This data provides trends and visualizes patterns for easier monitoring of the health of each piece
of equipment.
In the case of motors, temperatures, vibrations, revolutions or too-frequent starts, additional desired criteria can be tracked. Changes in temperature and vibration can indicate potential problems in equipment. Monitoring low voltage motors is considered expensive and is often overlooked, leaving problems unnoticed until the motor fails. Unplanned downtime can be avoided, efficiency optimized and safety improved with remote monitoring.
For variable frequency drives (VFDs), parameters including voltages, currents, torques, overloads, component wear and more can be monitored. Users can often connect to a device-level drive to review individual asset parameter values and event logs. The deployment of backup and support packages, along with remote drive experts, allows for efficient troubleshooting and support without the need for on-site intervention, thereby maximizing uptime and operational continuity.
Typical parameters that help provide an indication of pump health status include vibration and temperature. More serious issues such as flow turbulence and cavitation can be detected using vibration frequencies. For example, certain problems, such as rolling element bearing issues, need to be identified well in advance for planning corrective actions. Remotely monitoring these parameters in a pump is beneficial because it provides users with data to make informed decisions in planning a maintenance schedule.
By monitoring all individual assets, users can determine which exact piece of equipment is operating outside its desired operating range, quickly analyze why and take action to correct the issue. As a result of remote condition monitoring, companies can also use the data to validate maintenance and purchasing decisions and give peace of mind that equipment is performing as desired.
Remote Monitoring in Water & Wastewater Applications
Remote condition monitoring in the water and wastewater industries is especially impactful to productivity, regulatory compliance and ensuring permit and license conditions are met. By remotely monitoring equipment, the need for personnel to enter dangerous work areas (both electrical and chemical/gas exposure) to adjust and monitor equipment is greatly reduced. This is particularly useful in managing multiple sites or remote locations, such as wet wells and lift stations. For example, if a motor current is changing but the amount of water being transferred is not, the operator can be alerted and determine if the water is moving as it should, or if pump efficiency has been impacted. This can be identified and corrected without needing to send maintenance personnel into the lift station or well to troubleshoot and correct the issues. Automating inspections of equipment health through remote monitoring also reduces injury risk by not requiring personnel to enter more hazardous locations.
Using sensors to monitor parameters like flow rate, motor temperature, vibration, motor current and more can optimize performance, maintain pump efficiency and lengthen pump life, avoiding extended downtime and costly damage to equipment.
Operators can also ensure pumps run efficiently and to specification, meeting permit and licensing conditions. It is also beneficial for environmental protection. Remote monitoring ensures that any issues with equipment running treatment processes are quickly identified and corrected, minimizing potential for spills or treatment failures that affect discharge quality. Early detection of issues also reduces the need for emergency repair call-out costs and replacement equipment. This results in cost savings in both labor and parts as well as a reduction in non-revenue lost water in clean water networks.
There are many benefits of remote monitoring. When deciding if remote monitoring is worth the investment, consider the cost and energy savings, increased uptime and safety benefits provided by identifying root causes earlier, before they impact production.