As the debate over the pipeline’s future continues, Siemens and TransCanada celebrate six years of collaboration on an advanced oil & gas monitoring system.
04/02/2015
STANTON, Neb. (Nov. 11, 2014)—Even as the Midwest cold dipped into the teens, the steel at Pump Station 38 was hot to the touch. Beneath the curved pipes rushed hundreds of thousands of barrels of Canadian crude oil destined for Gulf Coast refineries. Pump Station 38 is one of dozens of pump stations along the Keystone XL pipeline—a 1,200-mile addition to the Keystone system that connects Hardistry, Alberta, to Steele City, Nebraska. Six years of political debate has made the Keystone XL (KXL) project a favorite for national headlines, but the real story lies in the innovative technology that makes the expansion possible.
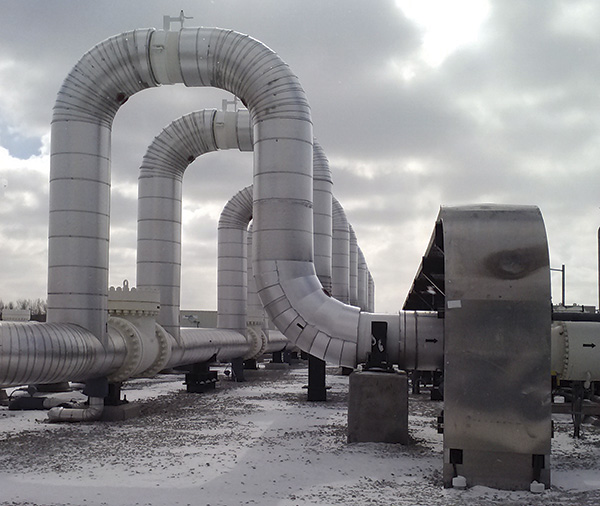
Mapping the Pipeline
A common misconception is that KXL will be the first oil pipeline on American soil. The pipeline is actually another addition to the Base Keystone system—the fourth phase in a crude oil transfer network that spans much of the Midwest and reaches from Canada to the Gulf of Mexico. Base Keystone started as 275 miles of pipe and five pumping stations. Now, the system and its expansions rely on more than 200 pumps to handle 47 approved petroleum products.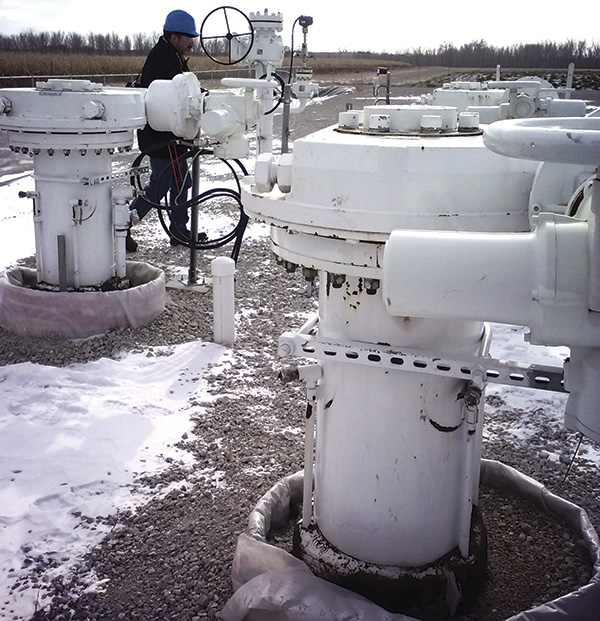
Pressure Control
Virgil Pfenning, area manager of Pump Station 38, said that the products move through the station at more than 1 million gallons per hour, or 660 gallons per second. This is equivalent to “walking pace,” Pfenning said. At this rate, about 550,000 barrels of crude product are handled by the station’s pumps each day.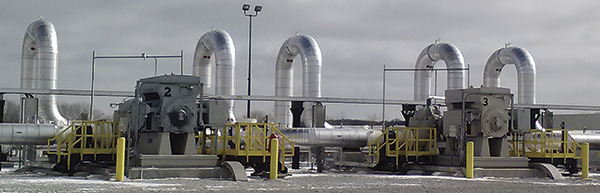
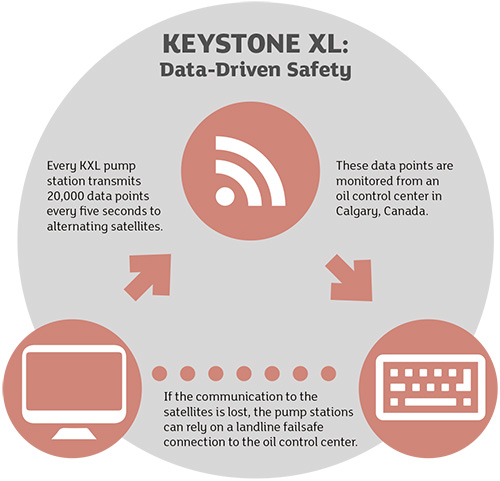