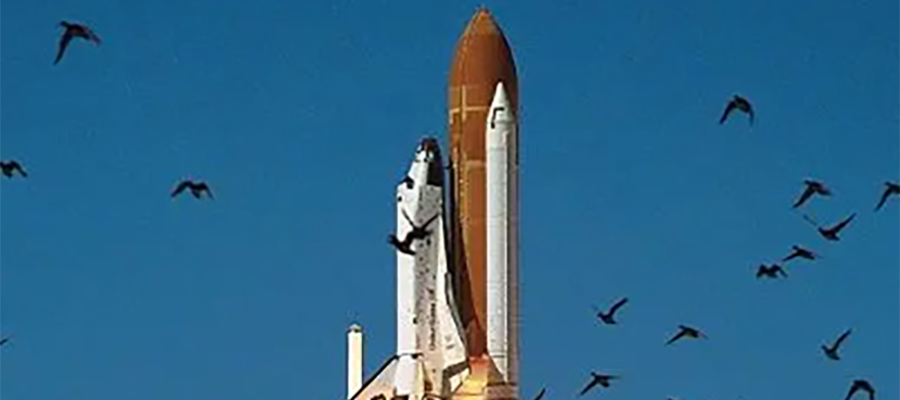
On Monday, January 27, 1986, the anticipation was palpable as the crew of the space shuttle Challenger readied themselves for a historic launch. Poised atop the multibillion dollar spacecraft, all systems signaled a resounding “go for launch” on that warm Floridian day at Cape Canaveral. However, as technicians diligently sealed the cockpit door, an unexpected glitch emerged. The handle steadfastly refused to budge after a 90-degree rotation. No amount of pulling or pushing could dislodge it, prompting Lockheed Space Operations engineers to request power tools for assistance.
The unfolding drama captured global attention, with live TV broadcasting the escalating tension. Battery-operated drills and cutting blades were deployed, only to discover the batteries were running low, exacerbating the predicament. A seemingly inconspicuous bolt, responsible for securing the handle to the shuttle, had seized, casting an unforeseen shadow over the imminent launch of seven astronauts into space. Faced with escalating embarrassment and the ticking clock, a pivotal decision was made—to cut the handle with a hacksaw.
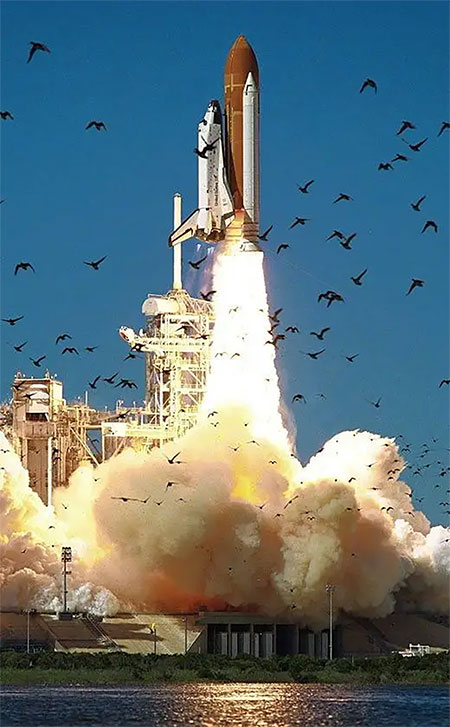
(Images courtesy of Fluid Sealing Association)
A maintenance worker, propelled into action from a nearby service building, entered the fray, President Reagan observing the unfolding events from the Oval Office on live TV. After overcoming security hurdles, the worker ascended the colossal 184 feet of the space shuttle using an elevator. The team diligently wielded their tools until the handle finally broke off, tumbling down between the gangway and the shuttle. Simultaneously, a weather front tracked by NASA swept into Cape Canaveral, with winds surpassing the shuttle’s “return to launch site emergency constraints” threshold. NASA, confronting the unpredictable forces of nature, chose to abort the launch, rescheduling it for the following day.
Yet, hidden beneath the dramatic tale of this hatch bolt seizure lies a narrative rarely discussed—the incident that transpired on the eve of the space shuttle Challenger disaster. In the aftermath, discussions predominantly focused on the sealing of the O-ring in the booster rockets as the primary culprit behind the catastrophic setback that reverberated through NASA’s space program. However, it is crucial to acknowledge that bolting, exemplified by the seized bolt, played a contributory role in this tragic accident. Beyond the space mission context, the challenges associated with bolting extend to plant operations, generating safety hazards and operational headaches, particularly in the domain of tightening valve glands.
At the core of industrial discourse lies a significant debate on how to precisely apply bolt load to valve packing. When overtightened, valve packing can wreak havoc, causing substantial damage to the valve and disrupting overall operations. On the flip side, insufficient load jeopardizes the valve packing’s ability to maintain a reliable seal, culminating in costly leakage.
In times past, installation instructions for valve packing would often invoke the nebulous concept of “the skill of the craft” when it came to tightening. This approach relied on institutional knowledge, lacking precision. Older valve packing designs featured loose cores of fibers, a potential trigger for blowout failure modes when subjected to load loss. This perilous scenario resulted in injuries to maintenance workers, prompting efforts to preempt accidents by applying extra load to valve packing. This extra load typically took the form of using a pipe or cheater bar to extend the length of the wrench tightening the gland follower bolts, creating extreme gland forces that wreaked havoc with the valve’s operation.
Excessive gland load on valve packing bolts gives rise to three primary issues. Learn more about these challenges and how to prevent them in Part 2.
We invite your suggestions for article topics as well as questions on sealing issues so we can better respond to the needs of the industry. Please direct your suggestions and questions to sealingsensequestions@fluidsealing.com.