01/22/2014
Q. What are some factors to consider when conducting a life-cycle cost evaluation for a sealless rotary pump? A. There is a substantial first-cost premium for sealless rotary pumps. Depending on the type, this cost is a multiple of a similar pump with a conventional mechanical seal. A magnetic drive pump’s expense is primarily associated with the cost of the magnets required to transmit torque. Sealless pumps may be selected for many applications based on a life-cycle cost analysis. Each application is subject to individual review, but general areas that may be considered in a life-cycle cost analysis are:
- Negative for sealless pumps
- Initial capital cost
- Additional instrumentation, if required
- Lower drive efficiency
- Variable cost elements based on user experience
- Cost of maintenance differential (numerous surveys have shown mechanical seal failure to be the primary cost of pump maintenance)
- Cost of production loss associated with system reliability
- Reduced cost of instrumentation compared to complex seal systems
- Positive for sealless pumps
- Monitoring exemption for fugitive emissions under the Clean Air Act
- Cost of liquid disposal as a result of seal failure
- Risk associated with personnel or fire incident loss
- Cost of alternate sealing systems to meet environmental emissions control requirements, such as double-seal and compliance
- Value of extended operating periods between unit turnaround
- Space reduction when compared to complex seal systems
- Cooling water costs
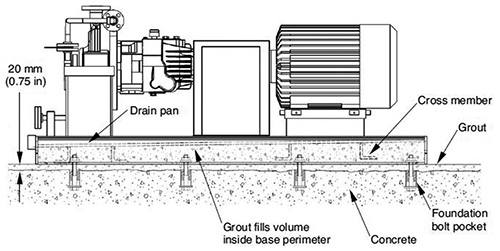
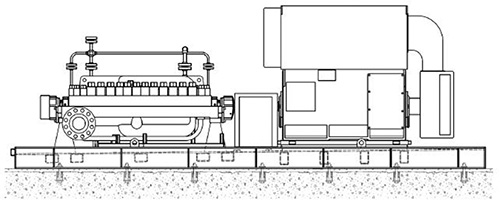