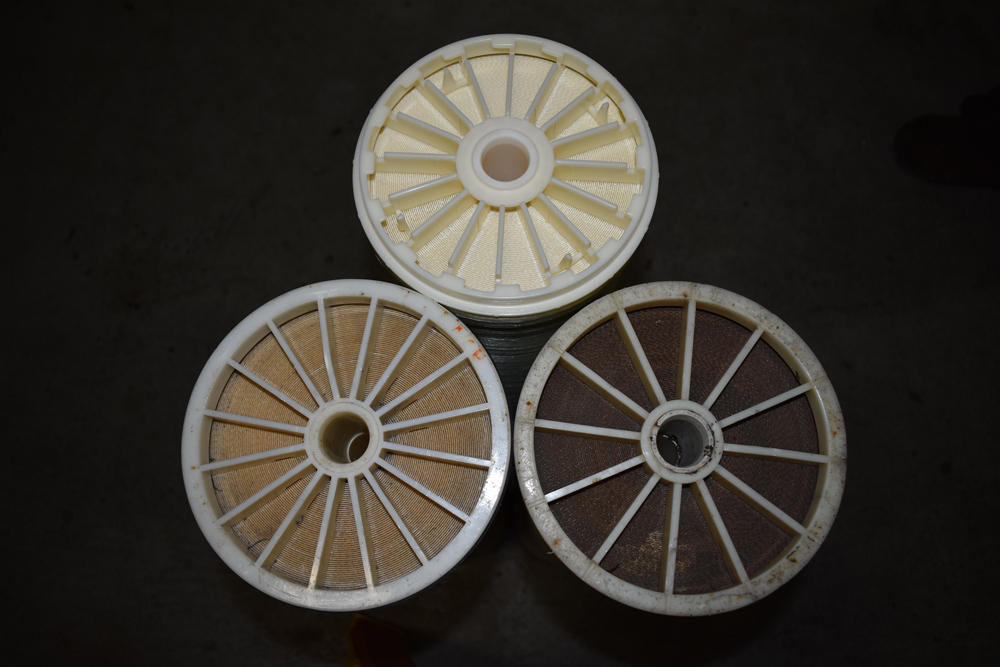
Part 1 was published in the May 2023 issue of Pumps & Systems.
Reverse osmosis (RO) membrane manufacturers provide guidelines for when to perform a cleaning that are based on the normalized permeate flow rate (the permeate flow rate corrected for changes in pressures, salt concentration and water temperature) and the normalized pressure differential (the membrane inlet-to-concentrate pressure differential corrected for changes in flow rate and water temperature).
They generally agree the RO should be cleaned if the normalized permeate flow rate declines from its clean baseline value by 15% or if the normalized pressure differential increases by 25% from its baseline value. Because the ability to fully restore original RO performance will be impacted by the type of fouling solids and other variables, these are only guidelines, but they serve as a conservative way to operate the RO system that improves the likelihood performance will be fully restored using normal cleaning procedures with most types of fouling solids.
Many membrane manufacturers and RO system manufacturers offer spreadsheet programs that will assist in performing these calculations. It may also allow you to graph these variables, which will offer excellent insight as to the health of the RO membranes, as well as whether a cleaning should be scheduled due to accumulated fouling. Some of these companies offer online monitoring and graphing programs for trending RO performance over extended periods of time.
If after the cleanings there continues to be a declining trend in the normalized permeate flow rate or in the percent rejection of dissolved salts (usually measured using the water conductivity) or an increasing trend in the normalized pressure differential, then the membranes are suffering from declining health and another course of action should be considered.
For example, ineffective on-site cleanings may be due to insufficient RO downtime or plant chemical limitations. Off-site cleaning by a third party should then be considered. If off-site cleaning is also ineffective at restoring original performance of specific membrane elements, then plans should be made to replace the poorly performing membranes.
Partial Membrane Replacement May Be Sufficient
In many cases, membrane replacement can be surgical. In the case of permanent fouling, it is possible cleaning was ineffective with just the most severely fouled membranes, such as the inlet-end membranes, and only those will need replacement.
When scale formation causes an increase in the RO last-stage pressure differential that is not restored by cleaning, only the concentrate-end membrane elements will need to be replaced to restore original performance.
Scale formation can occur quickly if there is a failure in the means used to prevent that scale or if the water conditions should change. Common causes include the failure of a chemical injection pump or poor regeneration of an upstream softener. Many types of scale will cause the last-stage pressure differential to increase. On-site acidic cleaning will often be successful if the scale is primarily composed of calcium carbonate, which will be evident when there is a substantial increase in the permeate conductivity from the affected membrane vessels. Sulfate and silica scales are far less soluble than carbonates, and their presence may result in the need to replace the concentrate-end membranes.
Ways to Extend Membrane Life
The polyamide thin-film membrane commonly used for reverse osmosis can tolerate many aggressive chemicals but has minimal tolerance to the presence of strong chemical oxidizing agents in its feed water—the most common concern being free chlorine. Even concentrations as low as 0.05 milligrams per liter (mg/L) of free chlorine will damage the membrane polymer over time. This oxidative damage is cumulative, as each exposure results in more breakage to its polymer links as chlorine atoms become attached within the polymer. An increasing normalized permeate flow rate, followed by a declining salt rejection, usually means membrane oxidation has occurred.
Ozone is another oxidant of concern if it gets into the RO feedwater. Even trace concentrations will rapidly react with the membrane. But while the inlet-end membranes will be quickly destroyed and require replacement, the ozone will be fully depleted before reaching the concentrate-end membranes.
Because free chlorine is less aggressive, its degradation of the RO membranes tends to be more uniform throughout the RO system, and all RO membranes will need to be replaced if the problem is not quickly corrected. Inlet-end membranes may be more prone to oxidation by a low concentration of free chlorine or chloramines if iron or other transition metals are in the inlet water, which tend to deposit in those membranes and will catalyze the oxidation.
When metals are not appreciably present in the RO inlet water, it may be feasible to obtain reasonable membrane life, even while allowing chloramines to be present in the RO inlet water. Depending on the water pH, chloramines can be stable and only minimally oxidative for the membrane. If not already present in the water source, chloramines may be added to the RO inlet water for biological control. With water that has a high potential for biological activity, allowing the chloramines prevents a high RO fouling rate that might otherwise result in the need for frequent RO cleanings.
Do Not Over-Inject the Sodium Bisulfite
A common method used to break down the chlorine in the RO inlet water is to pump in a chemical reducing agent, like sodium bisulfite. A failure in the injection pump operation, or simply running out of bisulfite solution, can result in significant losses in RO performance within hours if not caught and resolved sooner. Incomplete mixing of the bisulfite in the inlet stream, or not setting the pump injection rate appropriately for the incoming chlorine concentration, can result in accumulated performance losses over an extended period.
Concern about chlorine damage can lead to a tendency for operational personnel to set the bisulfite injection pump for an excessively high injection concentration to make certain the chlorine is fully broken down. Over-injection is likely if the control target for the bisulfite injection pump setting is based on trying to achieve a 0.00 free chlorine analytical result, especially given the best analytical sensitivity for many of these test methods is 0.02 mg/L. Targeting a low oxidation-reduction potential (ORP) measurement for the injection setting can also lead to over-injection, since increased bisulfite injection can reduce the feed water pH and will cause the ORP reading to increase. Best practice would be to set the bisulfite injection based on a sulfite residual that ensures complete bisulfite destruction without unnecessary excess. If the incoming chlorine concentration is consistent, as well as the sodium bisulfite solution concentration, it might be safe to maintain a target sodium bisulfite concentration of 2 mg/L for the residual1 with no danger of this bisulfite concentration ever declining to zero.
Sodium bisulfite over-injection can result in a reduction in the dissolved oxygen concentration in the RO water, which then will cause the water to be more conducive to heavy growth of slime-producing bacterial species, which can quickly foul the RO system with stable biological materials that will be difficult to remove with chemical cleaning. Biological fouling is one of the most common fouling problems that can reduce membrane life. If the source of the biological materials is upstream of the RO, the inlet-end membrane elements will be most severely impacted and may require replacement.
Poor Performing Membranes Requiring Replacement
When there is a decline in the RO salt rejection, the increase in the permeate conductivity can often be isolated to a particular location within the RO system by first measuring the conductivity of the permeate water from each pressure vessel—a method called profiling. If there is high permeate conductivity from a single vessel, the problem may be a damaged O-ring.
Probing the poor-quality vessels will further isolate the regions where excessive salt is getting into the permeate stream. This involves inserting tubing into the permeate interconnections within the pressure vessel to divert water away from the bulk stream to measure water conductance coming from specific locations within the vessel. By testing the permeate water coming from varying distances within the suspect pressure vessel, it may be possible to isolate the problem to a particular interconnector or to a specific membrane element within that vessel. The replacement of its interconnector O-rings, or of a suspect membrane element, may then be sufficient to restore original performance.
Attempting to maximize RO membrane life is a reasonable goal for most RO systems. This is most easily accomplished with well-designed RO systems that have adequate pretreatment so they can be operated with a manageable cleaning frequency that fully restores original performance. Knowing when best to clean can be determined using an RO monitoring program that includes the calculation and trending of the normalized permeate flow rate, the normalized differential pressure and the salt rejection. Achieving maximum membrane life also means the RO membrane must be protected from oxidants, like free chlorine, but not by over-injecting sodium bisulfite. Finally, if a performance problem should arise, its effects should be isolated to the specific membranes responsible by profiling the vessel permeate conductivities and probing suspect vessels so the membranes specifically responsible for the poor performance can be surgically replaced.
References
1. i.e., the concentration after the sodium bisulfite fully reacts with the chlorine in the water