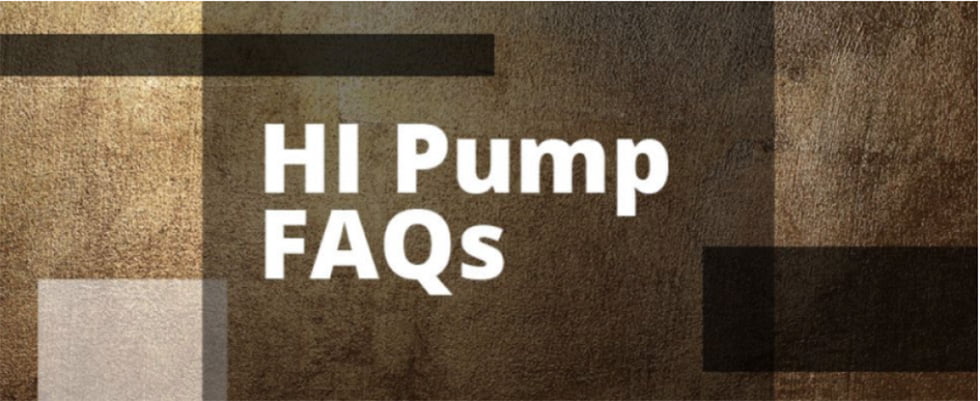
Why would I use a mag-drive pump?
Magnetic drive pumps are typically used in applications that require liquid containment. They use strong inner and outer magnets that transmit torque through a containment shell. This design feature eliminates the need for a mechanical seal and the potential for seal failure and leakage to atmosphere.
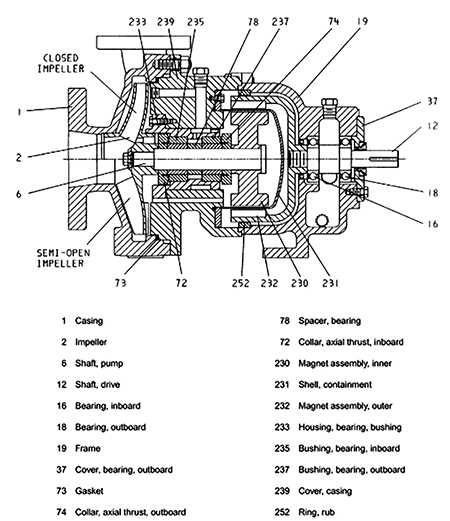
Magnetic drive pumps can be rotodynamic or positive displacement types. The Hydraulic Institute covers them in American National Standards Institute/Hydraulic Institute (ANSI/HI) 5.1-5.6 Sealless Rotodynamic Pumps and ANSI/HI 4.1-4.6 Sealless Magnetically Driven Rotary Pumps, but they are also covered in American Society of Mechanical Engineers (ASME) and American Petroleum Institute (API) standards. Image 1 from ANSI/HI 5.1-5.6 shows the inner magnet assembly (230), the containment shell (231) and outer magnet assembly (232).
The application benefit of the magnetic coupling is it provides primary containment without a dynamic (mechanical) seal, limiting the chance of leakage to atmosphere. This requires some additional design features that must be considered in their application. For example, there will be bushings to support radial loads (235 and 237) and axial thrust collars (72 and 74) that are product-lubricated. The product lubricated bushings and collars require the pumpage to be of sufficient pressure so it does not vaporize, and it must be free of particles, or other design features need to be considered.
For more information on magnetic driven pumps, refer to ANSI/HI 5.1-5.6 and ANSI/HI 4.1-4.6 at pumps.org/standards.