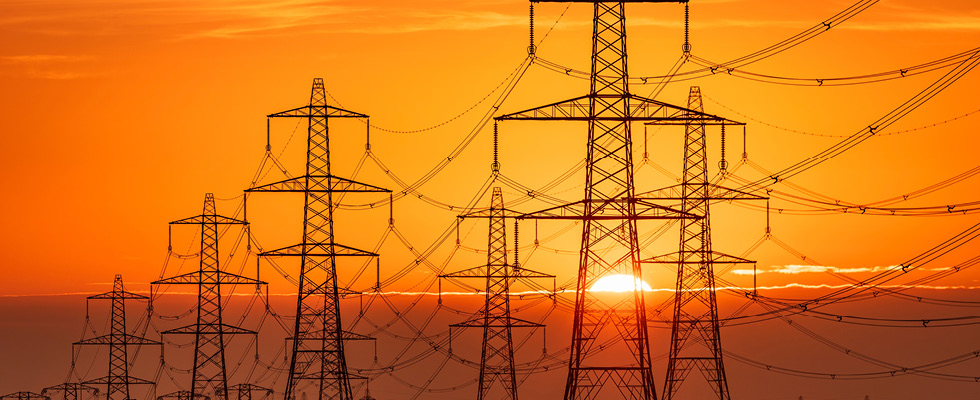
Power grids are an immensely complicated network. These vast networks of power generation, transmission and delivery ensure there is electrical power on demand for immediate consumption.
Historically, the main sources of power generation relied on coal, natural gas, nuclear and hydroelectric to create the electricity flowing into the grid. However, in the last few decades, renewable energy on a commercial scale—consisting mainly of wind and solar—has grown tremendously.
Wind and solar power have become technologically advanced in recent decades. They have also become much less expensive and more efficient, converting more sun and wind energy into electricity at a lower cost. The explosive growth of wind and solar farms has caused situations where the amount of power produced exceeds demand. This forces the renewable energy generation to be curtailed for increasingly longer periods while also wasting valuable wind and solar resources.
It is obvious that the need to store large quantities of electrical energy for this segment must grow equally as fast. Energy storage at this scale is essential to help achieve a total transition from fossil fuels to renewable energy.
These renewable energy sources also face another common challenge: The sun does not always shine, and the wind is not always blowing. This is in addition to the issue of the grid not needing the power being produced.
Long-duration flow battery storage can help address these challenges. Flow batteries help eliminate renewable curtailment (when the power grid can no longer accept power generated by renewable energy sources) by providing an additional energy storage option rather than wasting the valuable energy potential of wind and solar farms. Energy storage systems that can store power not needed by the grid are not new and include pumped storage in hydroelectric systems, compressed air storage, lithium-ion batteries and fly wheels.
Flow batteries are a good choice, especially when compared to lithium-ion batteries. Some of their advantages include:
- Lower fire risk than lithium fires, which can burn hot and be difficult to extinguish
- Long service life of 25, or more, years to meet or exceed the life of the wind or solar farm components without degrading like lithium-ion batteries
- Little or no self-discharge when idle, meaning maximum power is readily available
- Tolerance to overcharge and overdischarge, providing improved reliability
- Operation at a wide range of temperatures to ensure worldwide installation in a variety of climates and seasons
- Scalable to meet a wide range of energy storage requirements
How Do Flow Batteries Work?
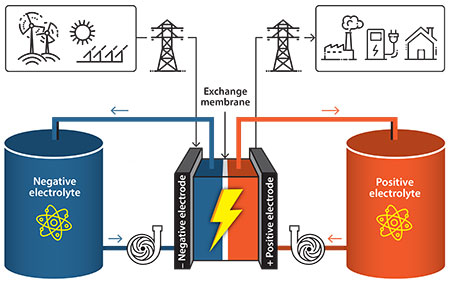
In a flow battery, negative and positive liquid electrolytes are pumped from large storage tanks through separate loops to porous electrodes separated by a membrane. During discharge, electrons freed by reactions on one side travel to the other side along an external circuit, powering devices on the grid. During charging, the opposite set of flows and reactions occurs as the battery stores power.
The power (MW) of a flow battery system is determined by the surface area of the ion-selective membrane, and the capacity (MWh) of the system is determined by the volume of the liquid electrolyte storage tanks. The length of operation can be increased by simply adding additional electrolyte storage capacity.
What Type of Electrolytes Are Used?
Different flow battery manufacturers use different types of electrolytes. Zinc bromide was the original material, which has since been replaced by other materials, including hydrogen bromide/diatomic bromine, vanadium-based, iron/salt/water-based and others.
How Are Electrolytes Moved Through Flow Batteries?
Magnetic drive centrifugal chemical pumps are used to move the electrolytes in the systems. Centrifugal pumps use rotational energy supplied by an impeller to move safely and efficiently at a wide range of flows. From applications less than 1 gallon per minute (gpm) (≈ 3.8 liters per minute [lpm]) to greater than 1,400 gpm (≈ 318 meters cubed per hour [m3/hr]), there is a size to fit any flow battery design.
Magnetic drives can eliminate the need for the mechanical seal found in other types of centrifugal chemical pumps. Mechanical seals typically contain metal, which can allow external components to potentially become electrified. In a magnetic drive centrifugal pump, there is no direct connection between the impeller and the motor shaft. Magnets are mounted on the motor shaft to transfer the motor power through a solid nonconductive barrier to other magnets inside the pump. These magnets rotate the impeller to move the fluid, preventing any electrification of external components.
The centrifugal design produces the smooth, pulseless electrolyte flow required for flow batteries to operate properly.
Mechanically sealed chemical pumps require routine seal replacement or repair that can make them costly to operate. Fortunately, magnetic drive centrifugal chemical pumps have low maintenance requirements. This low maintenance not only reduces the long-term cost of ownership but also decreases downtime, which is critical in flow battery applications.
Other benefits of magnetic drive centrifugal chemical pumps include:
- Corrosion resistance: Magnetic drive centrifugal chemical pumps are manufactured using corrosion-resistant materials. This construction allows them to withstand the harshest chemicals and conditions inside and out. Environments that would quickly break down other pumps are not an issue for their corrosion-resistant design. Some flow batteries use electrolytes that are corrosive.
- Electrically insulated construction: Magnetic drive centrifugal chemical pumps have nonconductive material options like glass-filled polypropylene and unfilled ethylene tetrafluoroethylene (ETFE). These nonconductive materials prevent any electrical flow from the charged electrolytes to the exterior of the pump. The ability to have this option is a critically important safety feature for flow battery applications.
Increasingly, international, federal, state and local governments are establishing aggressive goals for renewable resources to allow them to become carbon free, carbon neutral or clean energy. It is clear that energy sources like wind and solar are only going to increase, and taking maximum advantage of the technology will require the use of energy storage systems, with flow batteries becoming a key component of this growth.
Magnetic drive chemical pumps are a solid choice for flow batteries and have had a proven track record in flow battery applications for more than 25 years. The durable design will allow for continuous, long-lasting performance in flow battery applications, helping users meet the increasing number of regulatory demands to eliminate fossil fuels.