Large-scale pumping systems are all about the numbers. In applications where individual pumps require power inputs that are measured in megawatts, even the smallest improvement in efficiency and productivity can yield major benefits. One of the latest developments uses advanced data analytics to provide a real-time view of operations and highlight opportunities to improve the performance and efficiency of multiple assets at system level. There are several challenges operators of pumping systems might face. The cost of asset availability, increasing energy bills and restrictions in performance are three that usually appear at the top of the list. The key to addressing these, and a few others, is better interpretation of system data—using it to reduce costs, to make better decisions more quickly and to improve overall profitability. Large-scale pumping installations are usually equipped with sensors and data gathering devices to monitor performance. From vibration and flow rate measurement to system pressure and energy consumption, information is often collected and analyzed as part of the daily routine. The interpretation of data and putting it to work to benefit the operation is the greatest challenge. In many cases, there is a considerable opportunity to improve both the analytical process and the speed at which changes are implemented to optimize performance. Using modern communications and procedures enabled by the Internet of Things (IoT), it is possible to use near real-time data to drive actions in the field that will improve productivity.
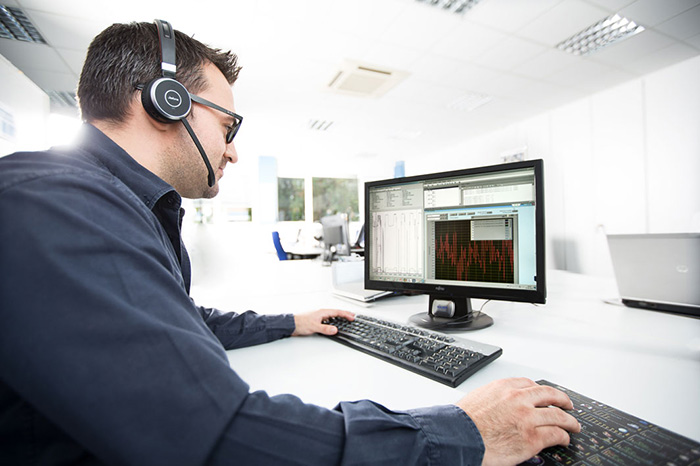
Ideal Operating Conditions
Accurate interpretation of pump system data enables operators to fine-tune performance and identify under-performing assets. Ideally, all pumps would be designed and manufactured to precisely match their applications, which would enable them to operate continuously at the best efficiency point (BEP) on the pump performance curve. However, in practice, it is necessary to closely monitor pump performance and establish underlying trends. These, along with associated flow rates, can be used to highlight periods when pumps are over-exerted and prone to excessive wear. Combined with historical data and new data analysis, it is possible to evaluate individual asset performance and optimize efficiency and reliability.Security of Data
Each pumping station should be connected to a supervisory control and data acquisition (SCADA) system, but this is not always the case. Some installations rely on local programmable logic controllers (PLCs) or process historians, but the important point is that the pumping process data is captured. One data gathering solution uses a secure access point to analyze the ongoing stream of data and deliver a tailored analysis and visualization of the information in a dashboard layout. At the same time, the software highlights potential issues with system assets to enable focused maintenance action. The whole predictive analytics package is designed to be flexible so that it can be easily integrated with existing information technology (IT) platforms and deliver valuable insights into the performance of the pumping installation.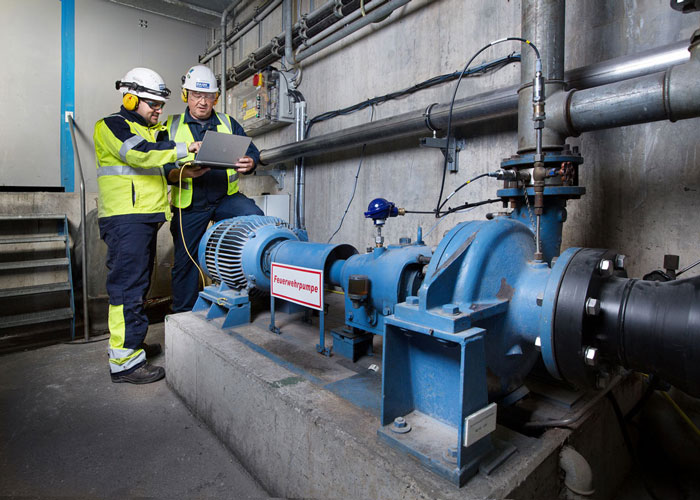