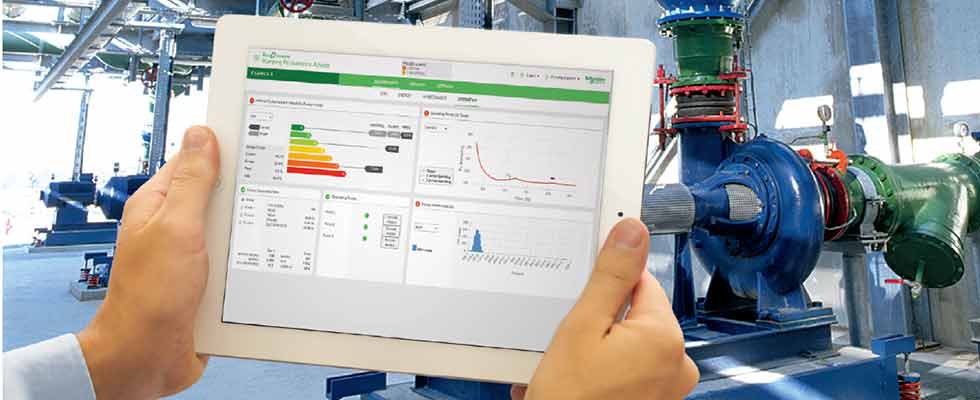
Water and wastewater operations are under increasing pressure to achieve ambitious targets for service delivery, regulatory compliance and resiliency in managing a large and aging infrastructure. With limited capital, they must find ways to extend the lifetime of vital assets, prioritize renovation and fend off cybersecurity threats. To meet these challenges, many are looking for savings in pump station energy maintenance and operating costs, which consume an estimated 75% of a typical pump station budget.
Addressing such issues requires timely access to—and manipulation of—performance data, which is available to the water industry through the digital transformation that is now taking place industry-wide. Digital transformation promises to harness the information volumes emerging in the wake of industrial operations and to apply it to improving operations. It does so by adding intelligence and connectivity to previously isolated assets, synchronizing control and communications among them, and sharing information with analytical applications. At the base of the architecture are the pumps, motors, drives and other assets that are becoming increasingly intelligent and connected. At the middle “edge” layer are controllers such as programmable logic controllers (PLCs) or other edge control devices like internet boxes that coordinate the exchange of data with analytical applications at the top layer.
Pump Station Improvement
For pump stations, a structured approach to digitalization means greater ability to contain costs. It could reduce pump station energy costs by enabling operation closer to target curves by leveraging the most efficient equipment and lower cost periods while matching set points or by optimizing charges on energy bills to avoid demand charges and power factor penalties.
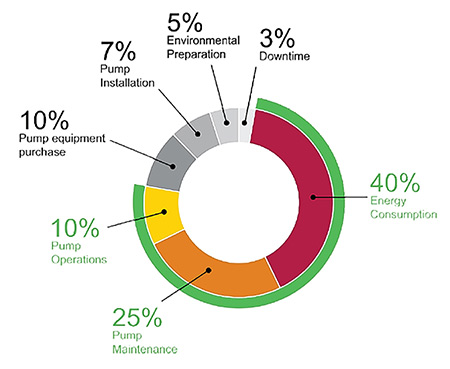
Reducing Costs
Digitalization could reduce maintenance costs by enabling pump operation closer to best efficiency points (BEP) by:
- eliminating inspection through advanced monitoring
- augmenting routine maintenance with condition-monitoring to identify pending points of failure before they happen
- protecting assets by eliminating operation in low-flow conditions
Digitalization could contribute to overall operational cost reductions through enhanced, real-time monitoring against target performance points; varying motor speeds to achieve established targets; and synchronizing pump performance in the wider context of pumping installation. This context might involve hydraulic systems, pump control strategies or auxiliary control functions like chlorination dosage.
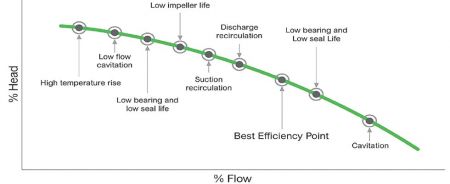
Asset Reliability & Optimization, Plus Maintenance Excellence
Detailed, timely access to information enables performance to reach new levels. This includes:
- cost-effective application of condition-based maintenance
- improvements in overall operating conditions
- reduction of frequency and, therefore, labor costs of inspections
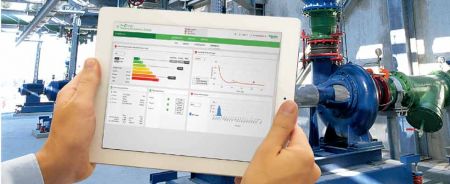
1. Condition-Based Maintenance
Impellers are among the first pump parts to go and once erosion and corrosion begins, it accelerates. Analytics can provide insight into the pump health index and capacity losses, which can correlate directly with energy usage as reported by energy meters. Monitoring pump suction with pressure transmitters can send alerts when pump suction dips below a certain level.
2. Improving Operating Conditions
In addition to monitoring pump conditions, enhancing pump operating conditions improves the meantime between failures (MTBF) by reducing the axial forces that contribute to shortening the lifetime of gaskets and bearings.
3. Reducing Inspection Frequency
When information on pump operations is limited or unreliable, frequent manual inspection is necessary to identify the need for maintenance intervention. Continuous digital monitoring of assets and key operating variables can reduce the frequency—and labor costs—associated with manual inspections. With modern digital tools, you can track electrical variables, mechanical variables and hydraulic variables of motors and pumps and receive alerts when performance drifts from established thresholds.
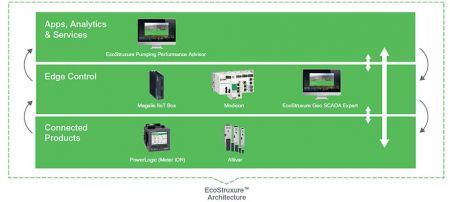
Case Study
An asset performance improvement initiative begins with setting the objectives of the pump station management. In a water treatment plant in northern Spain, the plant manager wanted to reduce energy costs by improving plant-wide communications regarding operating actions and their results. In addition, he needed to reduce operating expenses (opex). His technical and production managers shared the same objectives and were considering replacing aging pumps as a way to accomplish those goals.
This project started by deploying the architecture to gather and analyze operating data. Using instrumentation already installed on each of the station’s three pumps, water industry specialists configured energy meters, intelligent drives on the motors as well as pressure and flow sensors to monitor key process points.
SCADA software and PLCs at the edge control layer supervised the data exchange and production logic and connected with an industrial internet of things (IIoT) edge box across PROFINET and Modbus TCP networks. The IIoT edge box was housed in the plant control room and delivered data to the pumping performance advisor hosted in the cloud.
Return on Investment
After about three months of monitoring the Spanish facility, the following conclusions were reached:
- There was no need to replace the old pumps. Wear and corrosion impact could be managed through control loop tuning. It was, however, recommended that the facility refurbish impellers and wear rings.
- Changes in pump speed control improved performance and reduced the energy bill. Controlling speed variation with the drives was more effective than running the control loop in the PLC.
- The need to inspect every two weeks was eliminated.
- Automating switching in the chlorination valve reduced operation costs by approximately $5,300.
Implementing all recommendations except the impeller and repair ring refurbishment and the automated ozone system warnings saved nearly $22,000 a year, which represents 12% of opex.
Reducing Opex Through Asset Performance
- $8,300 per year in reduced energy charges
- $3,500 per year in maintenance costs by suspending the need to inspect every two weeks
- $10,000 per year in operations savings, apps, insights and alerts by automating the chlorination valve option (on/off)
- 12% in opex savings
The Fundamentals for Asset Performance Improvement
Although the previous example related to potable water, the same basic architecture can be applied to pumps in almost any setting. For example, the same user operates a wastewater treatment plant and water collection network and engaged an energy management specialist to accomplish similar objectives at their lifting station.
Similar variable speed adjustments were made based on monitoring, increased pumping performance, reduced energy consumption, wear and tear, and vibration. The monitoring also revealed the need for reducing the size of wastewater screens to keep out larger objects from increasing pump wear. Total additional savings were more than $21,000 (representing 14% opex).
Achieving such results involves three fundamental steps:
- Evaluate current operations to assess.
- the potential return and set improvement targets.
- Implement the improvements and monitor progress against targets over a few months.
- Adjust performance accordingly.
Operations will eventually reach a point of consistently meeting targets, but the process should not end there. Water and wastewater operations will always need to go beyond initial objectives to adapt to changing economic circumstances and physical realities.