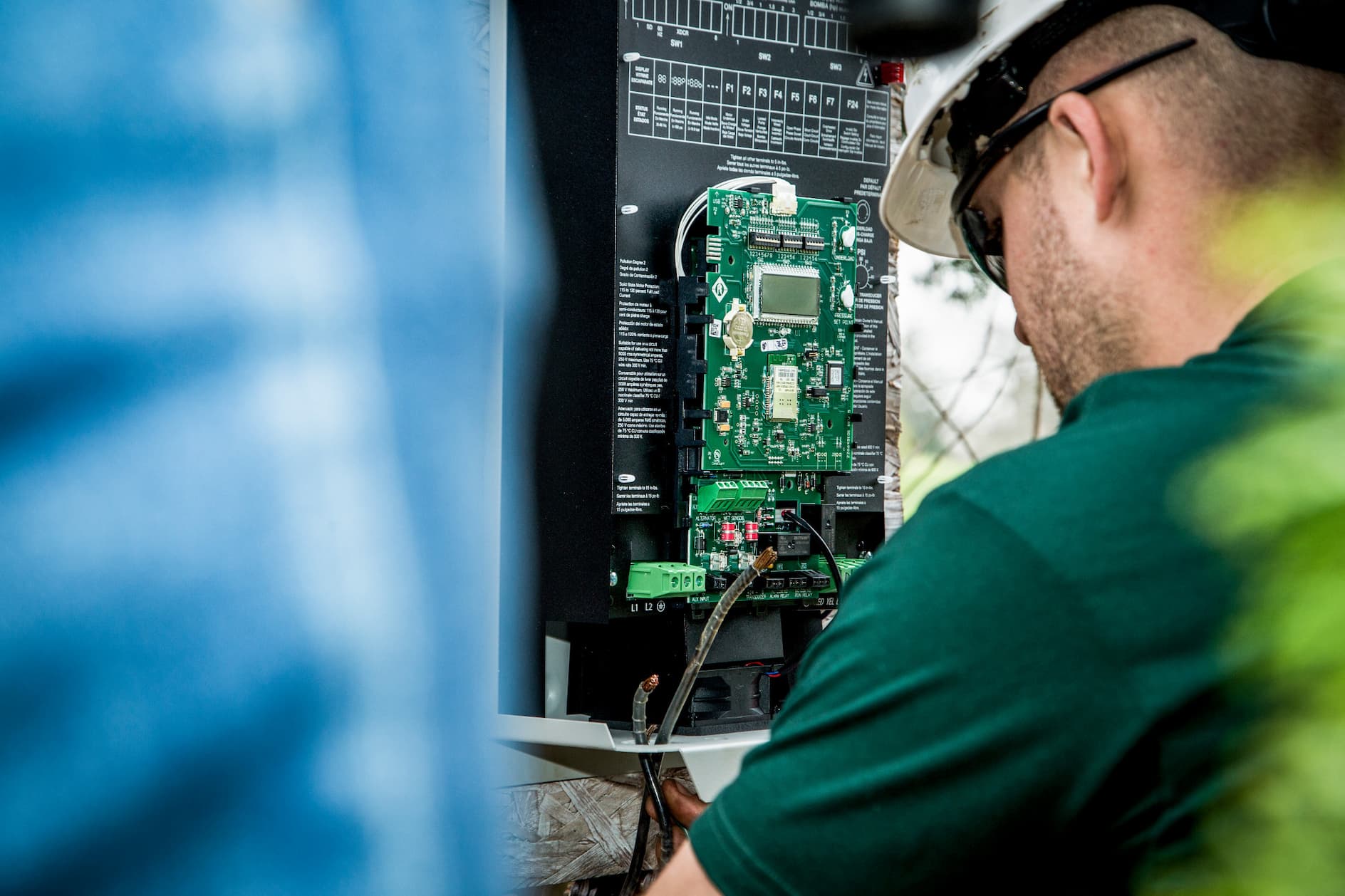
Just as products in the technology sector tend to become more advanced as they become smaller, the same holds true for many of today’s most vital water system components, including the motors and variable frequency drives (VFDs) used in pumping systems. In recent years, these critical components have become smaller in size, minimizing their overall footprint and delivering more advanced power and performance.
The advancements are due, in large part, to the innovative thinking and technological improvements that work to draw more power while occupying a smaller physical space. This is known as power density. Increasing power density allows owners and operators to benefit from more streamlined units that are easier to ship and install, without sacrificing performance or reliability. One of the primary drivers of technology and design evolution is the goal of delivering more power per volume, and the benefits do not stop there.
Advancements in Power Density
To fully understand the effects of progressing power density and why it is important, consider the circuit boards used in computers. In the 1950s and 60s, computers were massive and occupied buildings, yet they could only process a small amount of data by today’s standards. Throughout the 1960s and 70s, as engineers discovered ways to produce more computing power, they also worked on ways to make the boards more efficient. Circuit boards grew smaller and so did computers. In the 1980s and 90s, these circuit boards grew small enough that they could be used in new ways. Laptops and cellphones were born. Cars became more automated and continue to push the limits of what is possible. Hand-held games became a household staple and, albeit hard to believe sometimes, they have progressed beyond the legacy computing power that NASA once used to send the first man to the moon. Today’s computers are often a prime example of “small scale, big power” in action.
At the same time, engineers discovered other benefits of more efficient operation. They realized that smaller circuit boards generated less heat. When a room-sized computer, which required a specialized heating, ventilation and air conditioning (HVAC) system to cool it, was replaced by a handheld device, operating temperature became less of an issue. Smaller units also meant reduced costs in terms of production, allowing new markets and consumers to purchase products that were once cost prohibitive.
Circuit boards also became easier to maintain and more reliable. Engineers combined all these collective benefits (cost reduction, temperature maintenance, improved efficiency, smaller size and enhanced reliability) into one big catchall benefit: increased power density.
The pumping industry benefits from the effects of improved power density as well. Today’s most advanced circuit boards are now used in many water system components (VFDs, soft starters and protection devices, among others).
Continuous improvement across the industry, including a revolving selection of more efficient components, has resulted in enhanced engineering of all pumping electronics. “Small scale, big power” opens doors to all power density benefits, delivering cost savings, lower operating temperatures, smaller size and better reliability to more users.
VFD Solutions
VFDs are one component that has benefited from increased power density, and these benefits trickle down to installers and users. In fact, when compared to the inception of VFDs 30 years ago, the power density of a drive’s primary components has increased more than seven times its original power (35 kilowatts per square centimeter [kW/cm2] from the beginning to 250 kW/cm2). What does that mean in terms of benefits, and how do those translate to both initial and long-term benefits to users?
Smaller footprint: In many industrial settings, real estate and floor space are at a premium. Whether housed in a ceiling, mechanical room or elsewhere, finding the right space for a drive on the job site can mean creative thinking and/or costly retrofits. This is true when the job requirements demand a drive panel configuration. Power density assures users can pack the most power in the smallest space. Water professionals report that even residential and light commercial customers are putting a premium on their space. Certain
VFDs have been engineered as self-contained units. The enclosures continue to be enhanced to meet various installation needs, including wall mounting, and allow for more flexibility and the capacity to complement the water system with adjacent products and services.
Easier installation: Traditionally known for their heavier enclosures, drive panel configurations can present challenges to installers depending on the application. The need to integrate various components under the same roof tends to create a space issue that results in higher installation costs, shipping and placement issues and more involved mounting. This is magnified in large-scale applications, such as those in an industrial setting, where a larger footprint and bigger, bulkier unit, seems unavoidable. In contrast, VFDs that have been optimized to improve their power density minimize their footprint while maximizing power output.
Improved heat dissipation: Because today’s VFDs can run more efficiently, installers can eliminate or reduce many of the cooling components previously required. For example, certain VFDs that operate as high as 98% drive efficiency (standalone drive), which is above the industry standards, require only 2% of heat dissipation when operating.
This is cost-effective, as engineers specify solutions for high horsepower jobs that would normally require larger and more costly components to address thermal management.
Ability to handle more demanding requirements: When applications require a reduction in harmonics, it is industry standard to include input filtering as part of the panel configurations that go along with the VFD. In general, because of more demanding specifications and standards, more components are needed within the product solution. A smaller VFD provides the room needed to fit these components into the panel.
Better reliability: Just as computers have become more reliable over the years, today’s VFDs are engineered to perform consistently and reliably for years to come. Manufacturing processes have improved the quality of the power and electrical components used throughout the drive. General components have also gotten more efficient and thus produce less heat than previous versions. Since heat is always the enemy of reliability, these advancements have led to more
stable units.
More advanced operation: Because many of today’s VFDs offer additional computing power, they also feature more advanced and intuitive features. This allows them to have communication protocols that enable connectivity to other devices and systems. Because of these advanced features, more applications can benefit from breaking single large loads into multiple smaller loads, such as booster systems. In these broken-up systems, owners and operators benefit from fitting these units into multiple smaller places within their site. In terms of setup, they also offer more plug and play designs that are easier to hook up to advanced apps and communication devices.
What’s Next for VFDs & Power Density?
As technology progresses, manufacturers have also come a long way in providing more efficient system solutions that are built around VFDs. This includes solutions that are engineered to operate with both induction and permanent magnet (PM) motor technology. PM motors themselves have also benefited from power density advancements.
Increased power density is no longer a concept that only benefits the high-tech sector. It has powerful implications for the work water professionals do every day. Technology advancements on VFDs and motors have allowed engineers to draw more power from a smaller footprint, bringing advancements in power density to a variety of water applications.
For owners and operators, the benefits of this evolution thread throughout the entire life cycle of the product, from reduced shipping to more streamlined installation to better overall performance. That makes power density an important concept for water professionals to not only know and understand, but also ask about for any project.