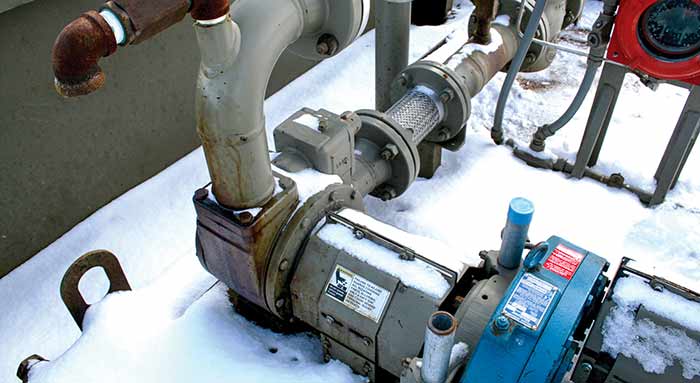
As the ambient temperature gets colder, many materials common in the construction of pumps become embrittled. This brittleness can result in sudden catastrophic failure of the equipment with virtually no warning.
For this reason, the end user must be careful in selecting materials for use in a cold environment. Brittle fracture is a fracture characterized by little or no deformation of the metal in the vicinity of the fracture.
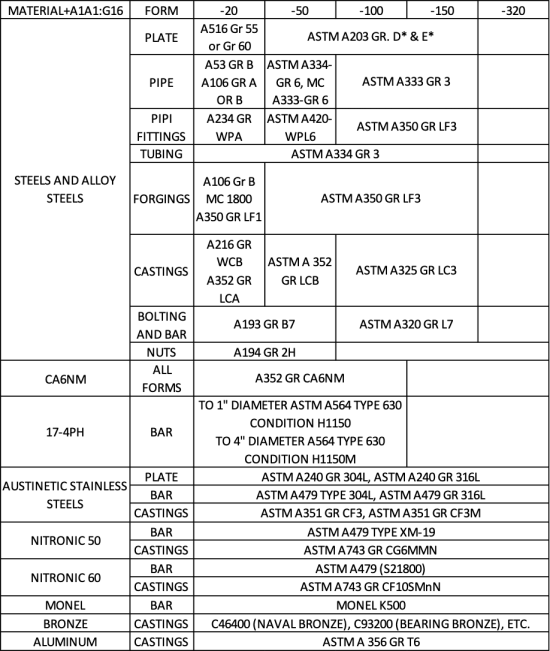
In general, metals fall into two distinct categories with respect to the influence of low temperatures on their ductility and toughness. A relatively small class retain a high order of ductility at low temperatures, and a larger class at some temperature undergo a transformation from ductile to brittle behavior.
Metals that retain their ductility at extreme subzero temperatures include nickel, copper and aluminum. These metals have a face-centered cubic microstructure and ductility at low temperature as common traits. Metals that have a body-centered structure such as iron, chromium and molybdenum have a marked decrease in ductility over a temperature range approaching the freezing point of water.
Although pumps used in cold service are usually applied in noncorrosive services, austenitic stainless steel is often applied because of its good low temperature properties.
American Petroleum Institute (API) 610 states that the purchaser will specify the minimum design temperature that the pump will see. This temperature will be used to establish impact requirements.
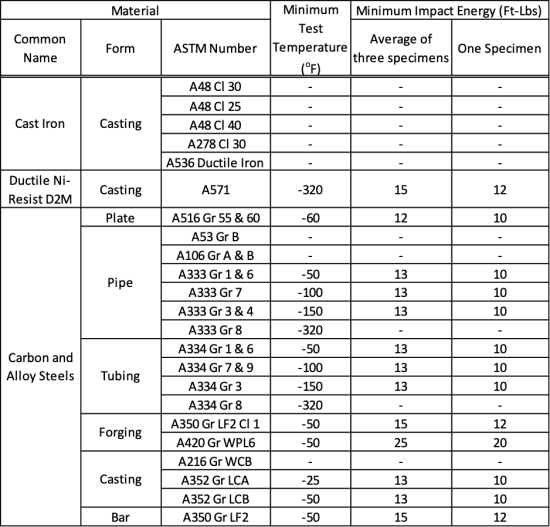
This will be the lower of the ambient temperature or the product temperature. In addition, a lower temperature may be specified based on liquid properties such as auto refrigeration. This is the temperature generated when a pump is vented, and the product has a high vapor pressure such as many liquefied gases.
Generally, materials used at temperatures approaching the freezing point of water will require an impact test. Exceptions to this are materials with high nickel content such as austenitic stainless steel, aluminum or copper. It is important that the purchaser and vendor agree on what conditions can occur during operation, maintenance, transportation, erection, commissioning and testing.
Also of consideration is the weld procedures used at the foundry and at the manufacturer to ensure that the material retains its ductility at the specified temperature. Of particular consideration is the fabrication of heads and cans for vertical pumps.
API 610 specifies the following considerations will be applied to the impact testing.
1. The governing thickness used to determine impact-testing requirements shall be the greater of the following:
- Nominal thickness of the largest butt-welded joint
- Largest nominal section for pressure containment, excluding:
- Structural support sections, such as feet or lugs
- Sections with increased thickness required for rigidity to mitigate shaft deflection
- Structural sections required for attachment or inclusion of mechanical features such as jackets or seal chambers
- One-fourth of the nominal flange thickness, including parting flange thickness for axially split casings (in recognition that the predominant flange stress is not a membrane stress)
2. In addition, if the American Society of Mechanical Engineers (ASME) Boiler and Pressure Vessel Code, Section VIII, Division 1 is specified, the following shall apply:
- All pressure retaining steels applied at a specified minimum design metal temperature below -20 F shall have an impact V-notch impact test of the base metal and the weld joint unless they are exempt in accordance with ASME Boiler and Pressure Vessel Code, Section VIII, Division 1, UHA-51
- Carbon steel and low-alloy steel pressure retaining parts applied at a specified minimum design metal temperature between -20 F (-29 C) and 100 F (38 C) shall require impact testing as follows:
- Impact testing is not required for parts with a governing thickness of 1 inch or less.
- Impact testing exemptions for parts with a governing thickness greater than 1 inch shall be established in accordance with ASME Boiler and Pressure Vessel Code, Section VIII, Division 1, UCS 66. Minimum design metal temperature without impact testing may be reduced as shown in Figure UCS 66.1. If the material is not exempt, Charpy V-notch impact test results shall meet the minimum impact energy requirements of ASME BPVC, Section VIII, Division 1, UG-84.
Generally, it is better to use a material that is acceptable at the designated temperature that does not require an impact test. Typically, this means upgrading to austenitic grade stainless steel or using one of the bronze or aluminum grades for bowl assemblies for vertical pumps. Impact tests are often unpredictable, which can result in a delay in delivery and cost overruns.
All grades of carbon steel used below 0 F should have impact V-notch testing at the specified temperature. This applies to the base material as well as weld joints. Austenitic stainless steels, nickel-based alloys, aluminum and brass do not require impact tests unless specified in American Society for Testing and Materials (ASTM) or ASME standards.
Image 1 is a compilation of materials that are suitable for cold service. Image 1 provides the common description for the materials specified. When using these materials, it is advisable to check with the suppliers for availability and cost before specifying them.
In selecting materials for cold application, careful attention must be paid to the thermal expansion of the selected materials. The difference in thermal expansion can be substantial. The differences in thermal expansions must be carefully determined and allowed for during coupling alignment and may not work at all if the pump has many stages.
For temperatures above -20 F, the materials listed in Image 1 are acceptable for use with an impact test. When an impact test is required, the values in Image 2 can be used as reference. The final authorities are the ASTM and ASME standards. Note that all steels are not acceptable for use in this temperature range.
For steels with temperature designated below -20 F, full compliance with the ASTM standards are required to meet the impact requirements. Impact testing will be included as part of the purchase order for these materials. Charpy impact tests can be specified to the values listed in Image 2. Not all grades acceptable for low temperature service are listed in Image 1. Other grades, as specified in the ASME or ASTM standard, can be used as long as the standard is followed.
Martensitic stainless steels (400 series) are not acceptable for pressure containing parts below -20 F.
ASTM A352 Gr CA6NM is acceptable for temperatures up to -100 F. Impact tests are required for this material when it is used below -20 F.
Austenitic stainless steels may be used for temperatures up to -320 F. The preferred materials are ASTM A340 Gr 304L and 316L. Full compliance, including solution annealing, must be complied with for the material to be acceptable for this application. All fabrications welding must be performed to ASME Section IX.
Nitronic 50 and 60 to the ASTM standards in Image 1 are acceptable to -320 F. Copper-based alloys in most cases do not experience loss of impact strength when exposed to cold temperatures. Many of the common materials in this category do not have published ASTM standards, and ASME does not require impact tests for these materials listed in the standards.
K500 Monel is a nickel copper alloy and has good mechanical properties for shafts down to -320 F. It does not require an impact test unless specified by the user to this limit. Cast Monel is also acceptable at this temperature range.
Most of the classes of bronzes, including nickel aluminum bronze, are acceptable up to -320 F. Nickel alloys such as Inconel have excellent low temperature properties.
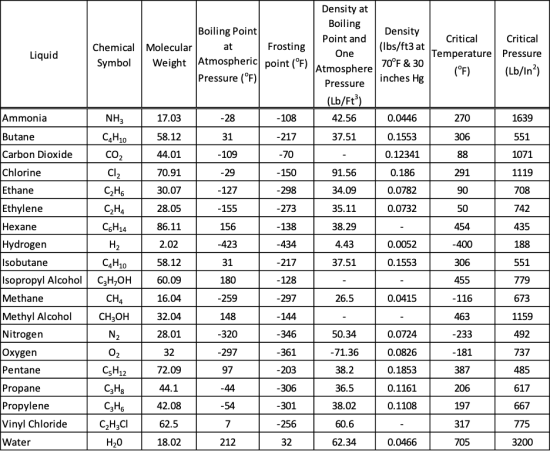
Image 3 lists some typical cryogenic liquids and their physical properties. This information may be used for pump design and calculations when complete information is not available from the user. This table can be used as a guide for the low temperature requirements for equipment. When the pump is vented, auto refrigeration will drive the pump temperature to the boiling point of the product at atmospheric pressure. It is necessary to design for this temperature in the selection of a suitable material.
References
1. API 610, 12th edition
2. ASME Section VIII, Boiler and Pressure Vessel Codes
3. ASTM Material Standards