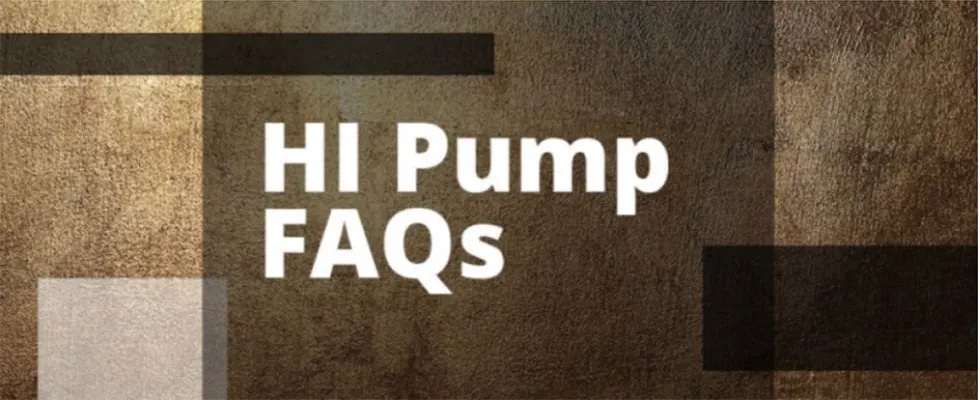
Mechanical seals in pumps prevent process fluid from leaking at the point where the driver shaft enters and exits the pump housing. In pumps, the process fluid in the pump housing is typically at a higher pressure than the surrounding environment. Without a mechanical seal, the process fluid would leak to the environment (Image 1, top). For a pump to function, it needs to retain the process fluid in the pump housing, which is accomplished by the mechanical seal. The mechanical seal (Image 1, bottom) accomplishes this with rotating components (red) attached to the rotating shaft and a stationary element (green) within a gland. A rotating and stationary seal face contact axially to limit the process fluid leaking from the housing along the shaft.
The seal faces are commonly made from carbon, tungsten carbide, silicon carbide and aluminum oxide (ceramic), but these are not the only materials used. A complete list of seal face materials, their properties and application considerations can be found in the Hydraulic Institute’s guidebook, Mechanical Seals for the Pump Industry.
For the materials listed, there are various manufacturing processes and grades. The combination of materials used for seal faces are chosen based on their physical properties relative to the application requirements. Application considerations that may dictate the appropriate seal face materials include the viscosity or lubricity of the process fluid, fluid temperature and vapor pressure, the chamber pressure, fluid corrosive properties and if abrasives are present.
Carbon is the most common seal face material. Carbon seal faces are used within a wide range of temperatures and can be alloyed to form compounds with a variety of frictional resistance. They are generally chemically inert, which allows them to be used with some corrosive fluids.
Tungsten carbide is widely applicable as a pump seal and exhibits many of the same characteristics as carbon, but with some superior properties, such as higher chemical resistance, tribological properties and thermal resistance.
Silicon carbide is available in a number of grades, including reaction bonded, alpha sintered, porous alpha sintered and composite grades that include graphite. All silicon carbides offer unique properties for use in demanding applications because they maintain strength at elevated temperatures and have excellent resistance to corrosion with low thermal expansion. These properties make them ideal for abrasive, corrosive and high-pressure applications.
Aluminum oxide varies in grade from about 85% to 99.8% purity. Because of its hardness, it offers excellent wear characteristics.
For more information on mechanical seals, please consult the Mechanical Seals for the Pump Industry guidebook published by the Hydraulic Institute.