By most definitions, metering pumps handle small or low flow volumes that are precisely dispensed at pre-set intervals. Most metering pumps, however, need to vary flows either manually or through some form of PLC control. The dispensing is usually done at low speed, with accurate repeatability being essential. Many dispensing systems are required to operate non-stop and may need to dispense the fluid several times a minute without human interface. The pump industry worldwide has a plethora of pump companies that manufacture metering pumps, which is good news for the end users. The good news for pump distributors is that metering pump sales worldwide are estimated at $2 billion per year. With a little research, most users should be able to find a metering pump that meets the majority of their requirements. Most metering pumps generally provide the same overall dispensing function,but can vary greatly in operation. Some metering pumps are designed to handle high discharge pressures while dispensing miniscule amounts. Others can dispense larger flow amounts but with lower discharge pressure limitations. The following is a sampling of some of the various types of available metering pump designs that are available, along with the industry-recognized capabilities and limitations of each.
Metering Pump Designs
Progressing cavity metering pumps generally can generally handle abrasive and corrosive liquids as well as suspended solids and viscous fluids. The double helical design creates a gentle pumping action that keeps minimizes shear to a minimum. Progressing cavity metering pumps are used in chemical processing, food and beverage dispensing and the personal cosmetics industries. This positive displacement pump is self-priming and can handle high suction lift applications. The downside to positive displacement pumps in metering applications can be their inability to run dry. Piston / diaphragm metering pumps are frequently used in municipal applications for dispensing PH additives. They are used in many other applications where high pressures up to 3,000 psi can be reached. Reciprocating pistons can either be designed to contact the dispensed fluid directly or they can be protected from direct fluid contact by a diaphragm. The disadvantage to a piston / diaphragm pump can be its tendency to clog. The most commonly recognized metering pump design is the gear pump. The industry leading manufacturers of metering gear pumps have designed their products for agricultural, chemical processing and dispensing as well as many other municipal and commercial applications. Limiting factors of gear pumps are their inability to run dry or handle clean fluids efficiently. Centrifugal metering pumps rank among the most commonly used. Their design fits many applications where the pump may occasionally "dead head" and must still continue to operate. The centrifugal design can also run dry without causing failure. These are two advantages over other metering pump designs that customers appreciate, particularly in unmanned operations. Even though the centrifugal design is popular, they too are not without limitations. Centrifugal metering pumps will not suction lift. Typical centrifugal metering pump applications tend to have higher pressure requirements since centrifugal pumps do not operate well at low pressures. In addition, they typically handle viscous fluids better than low viscosity fluids. The air operated diaphragm (AOD) and the double diaphragm (AODD) metering pumps are have a simple design. They typically are typically inexpensive to operate, especially if the air lines and a compressor have already been installed. The AOD/AODD pumps can run dry and are sealless, which eliminates any leakage. They also exhibit effective metering capability. The draw back to the AOD/AODD design is that they tend to clog easily. Peristaltic metering pumps are another positive displacement design. They are also called hose pumps, which is are a variation of the peristaltic design. The key to the success of this design is the pump's ability to isolate the pumped fluid from external elements. This makes it an ideal pump for medical applications where that require sterilization. The peristaltic pump is typically used to meter low flows such as required in intravenous fluid applications. Peristaltic pumps can also meter harsh chemicals since compatibility issues are limited to the tubing material. Most tubes are made of PTFE, but there are a variety of other materials are available. In general, the design is simple and inexpensive to operate. No valves or seals are used in a peristaltic pump. The hose pump is a robust design capable of handling pressures over more than 200 psi. The peristaltic pump design limitations include frequent tubing maintenance.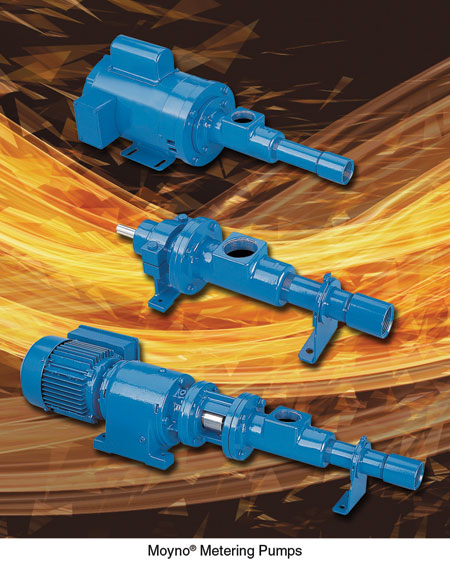
Applications
There are many hazardous applications that tend to be overlooked in which metering pumps play a vital role daily. The dispensing of hazardous or toxic materials is one example. These pumps can be found in numerous production facilities and laboratories worldwide. For example, a precise amount of a solvent additive (Methoxy-2-propyl) keeps a cleaning supply from turning into a lethal hazard. This precisely dispensed measurement is repeated many times each hour of every day and most likely goes unnoticed. Fuel additives are effectively dispensed by a line of plunger pumps that can withstand temperatures up to 750° F and pressures over more than 1,300 psi. These pumps are designed to handle gas to liquid conversions. Sealless CO2 diaphragm metering pumps are used for semiconductor manufacturing. These waterless systems pump cleaning fluid to remove etchings during microchip processing. To meet the challenging demands of many applications, it is often necessary for metering pump manufacturers to retrofit existing stock models with exotic elastomers or housing and internal materials. Another approach is custom engineered product development that results in a specific, proprietary model tailored to meet a customer's precise application requirements. This approach requires a commitment from both the manufacturer and the end user regarding design, quantities needed and delivery deadlines. Most metering pumps can be supplied in the latest construction materials to accommodate specific application requirements. The industry has advanced past the traditional cast iron and plastics to other products like Kynar, PVDF, polypropylene, glass filled, titanium, Acrylic/ PVC, carbon fiber and Hastelloy C & B2. Within the metering pump industry, certain designs seem to be selected most often for specific applications, regardless of alternative pump designs that offer better performance or longer service life. For example, the piston/diaphragm pump has been a dominant metering pump for sodium hypochlorite applications even though gassing can be an issue with this design. Ammonia and hydrogen peroxide have also caused gassing issues for diaphragm pumps.Next Generation of Metering Pumps
Worker safety and environmental protection of the environment are two key issues that the pump industry has championed for many years. The introduction of the magnetic sealless pump reinforced that claim. A magnetic drive for a pump is not a new concept but the design has proven to be a life saver when metering dangerous or environmentally un-friendly fluids. Leakage from a faulty mechanical seal could be dangerous. A magnetic drive sealless pump will not leak. The pumps are typically constructed with polypropylene housings or similar materials that are inert to chemicals. Most motors are of high efficiency design. Here is a brief sampling of pumped materials where a magnetic drive sealless pump would work best:- Sodium Hypochlorite
- Ammonia
- Ferric Chloride
- Aluminum Chloride
- Nickel Chloride
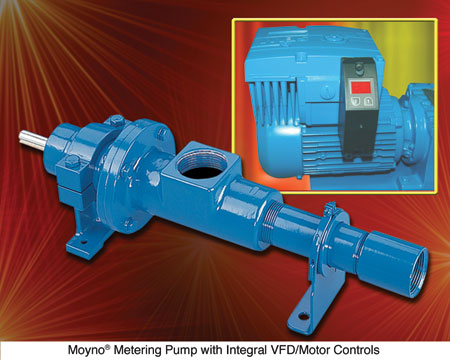