Energy is the driving force behind global manufacturing today, and demand has increased exponentially with each generation. The global modern economy depends on its accessibility and, even more so, on its affordability. This energy demand has generated an important discussion in the pump industry, and it begins with the increased cost of energy during the last decade. The Bureau of Labor Statistics reported that the average consumer pays 47 percent more for electricity than they did 10 years ago. While many producers and consumers are aware of this fact, many accept it as part of the cost of doing business. The desire to decrease the end users’ cost of doing business motivated a diaphragm pump manufacturer’s team to develop a new line of pumps to meet this energy problem head-on. Energy comes in many forms—liquid fuel, hydraulic, electrical and pneumatic. This article focuses on compressed air, which powers air-operated double diaphragm pumps (AODDP). AODDPs are used in many applications but are most commonly used in the transfer of fluid from one location to another. A basic assumption is a standard price for electricity of $0.07 per kilowatt hour (kWh). Another assumption is that a 1-horsepower (hp) air compressor yields, on average, 4 standard cubic feet per minute (SCFM) of compressed air.
Reading an AODDP Curve & Determining Operating Cost
To progress further into a discussion on the operating costs associated with compressed air usage in AODDPs, the proper way to read an AODDP pump curve must be understood. For a given operating condition, a pump curve conveys two important pieces of information:- The flow rate in gallons per minute (gpm)
- What the air consumption rate will be in SCFM
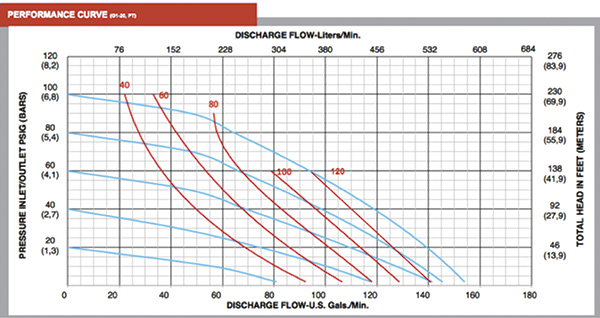
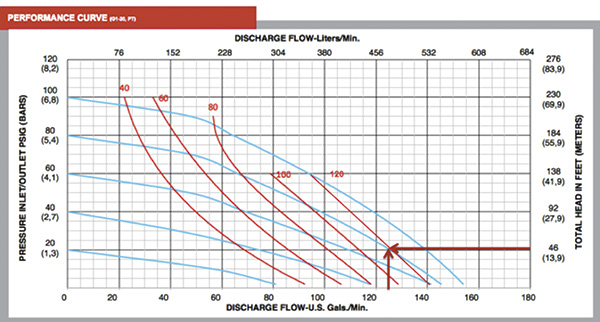
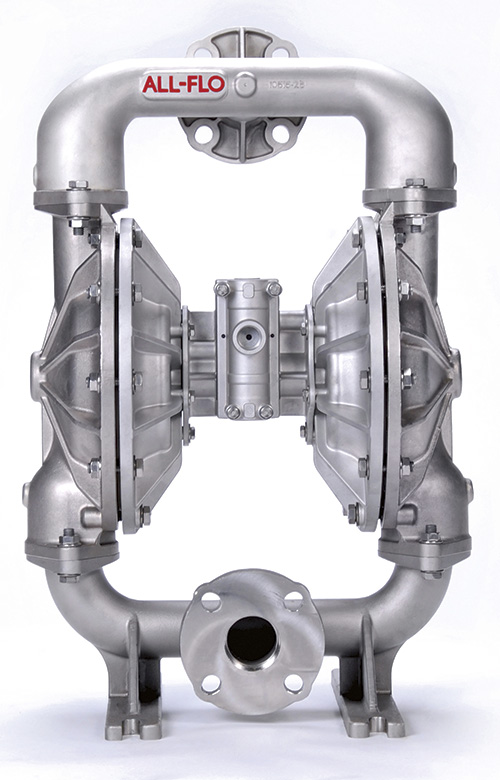
A More Efficient Solution
Recognizing the impact of the rising cost of energy on the cost of operating a standard AODDP, the pump manufacturer developed a line of pumps that would significantly reduce the end user’s cost of operation. This pump improves overall performance (with increased suction lift and flow rate) and uses less than half the compressed air of previous models. Multiple modifications were made to its original design, including:- Considerable reduction and optimization of “dead space” on the liquid and air side of the diaphragms
- An adjustment to the shift point of the main air valve to allow for a longer operating period during a more efficient point in the air valve’s cycle
The Improved Pump Curve
The redesign resulted in a pump with dramatically improved energy characteristics (see Figure 3). In Figure 3, the new design is compared to the average AODDP from Figure 2.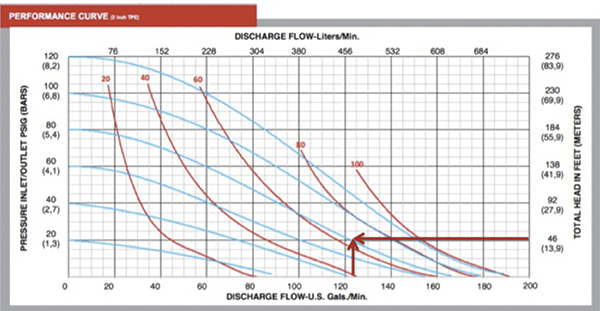
Redesign Benefits
The energy cost of several AODDPs will be analyzed from a different perspective. Instead of deciding to operate the pump at a certain air pressure, consider an application in which the pump must transfer 8,000 gallons of liquid every hour, 8 hours per day for an entire year. In this application, a basic transfer application with a liquid discharge pressure of 20 psi will be assumed. In this example, 8,000 gallons per hour is equivalent to a flow rate of 133 gpm (8,000 gallons/hour/60 minutes). The pump operates at 133 gpm against a discharge pressure of 20 psi. The air consumption required to operate this specific pump can be determined using Figure 4. Find 133 gpm on the horizontal axis and move up until it intersects the 20 psi line. The resulting point is the required operating condition to meet the 133 gpm requirement. From this point, the required air operating pressure in psi and the required air consumption in SCFM can be estimated.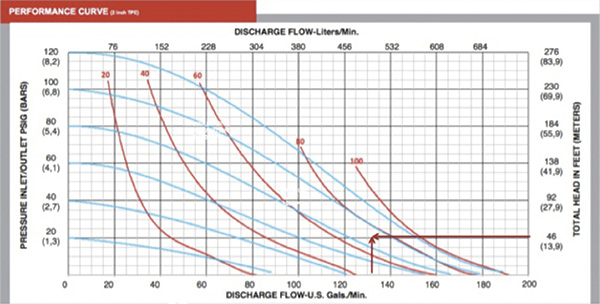
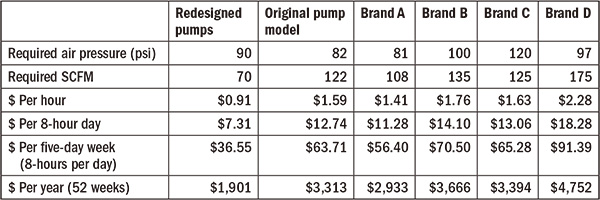