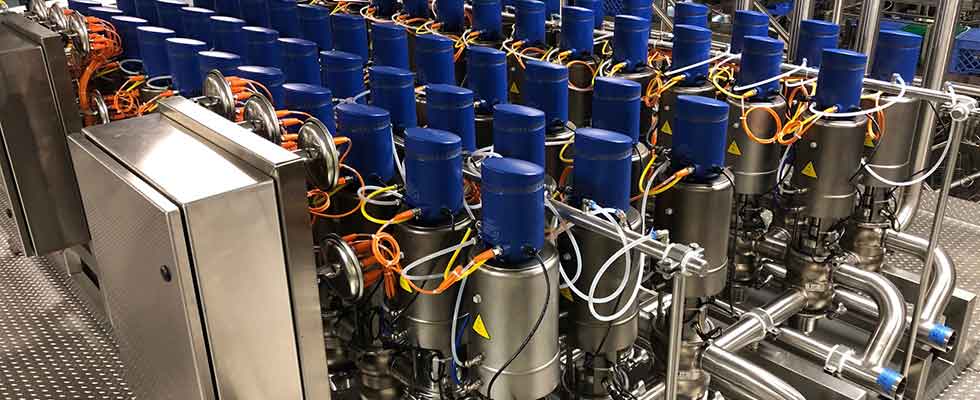
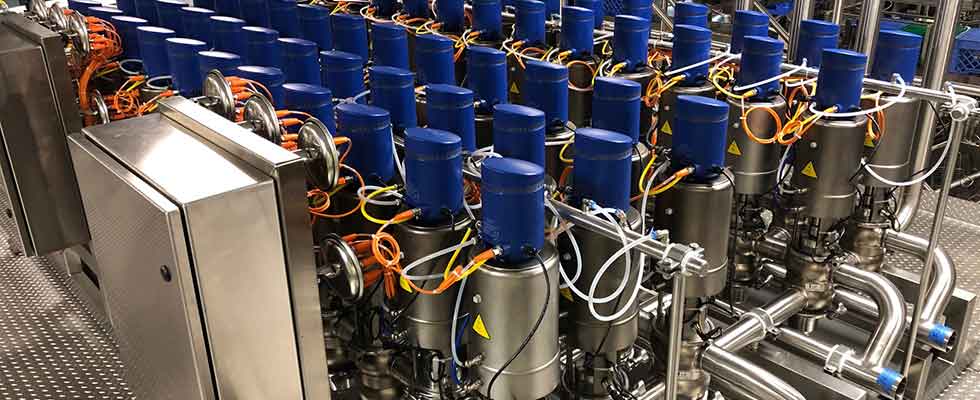
Large-scale dairy, food, beverage and other high-purity producers that want to enhance their process while eliminating the risk of fluid cross-contamination should consider mixproof valves as a solution. Understanding the working principles of mixproof valves, associated benefits and best applications for use is step No. 1.
Working Principles
Understanding a mixproof valve’s design, its working principles and benefits is critical to recognizing potential applications. A mixproof valve has two seats within the valve versus the traditional single seat. This allows for fluid separation. In the case of a leak, there is an exit area between the two seats. This creates a positive method for preventing the two different fluids from contaminating one another.
Mixproof valves have two independent plug seals to separate the fluids. The space between these seals forms a leakage chamber at atmospheric pressure during all working conditions. Leakage is not common with mixproof valves; however, if leakage does occur, product flows into a leakage chamber and leaves through the bottom outlet, making detection easier.
When the valve is open, the leakage chamber is closed. The product then flows from one line to the other. The radial seal design of the valve ensures that virtually no product spillage occurs during valve operation. It is possible to adapt valve configuration to get
optimum cleaning and water hammer protection as per the requirements of individual process specifications.
The mixproof valve’s design of two independently controlled valve stems helps ensure that two different products cannot mix. This makes mixproof valves ideal for large-scale food, beverage, dairy and other high-purity manufacturing facilities that produce several products at the same time.
Benefits
Designed to optimize resources, mixproof valves’ ability to perform dual functions simultaneously is helpful for food, beverage and dairy manufacturers. Integrating mixproof valve technology leads to decreased downtime and increased production. Maintenance and service are relatively simple, and a long product life span is common, with little investment required for spare part replacement.
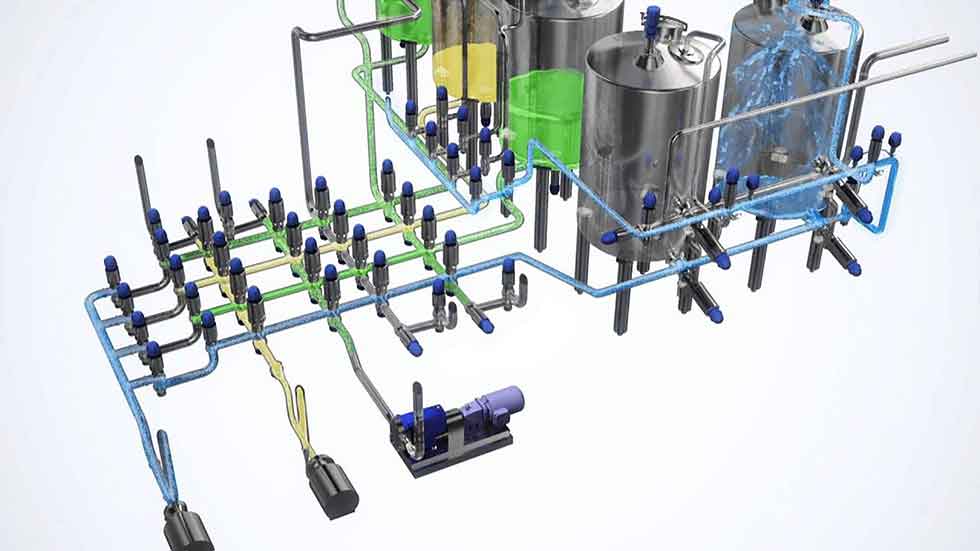
Here are several key benefits to explore when considering mixproof valve technology.
Flexibility
Mixproof valve technology offers flexibility. Using two independent plugs and seals means a single mixproof valve can replace two or more valves of other types. This flexibility results in boosted production capability and conserves space within the facility.
Workforce savings
Implementing mixproof valves means eliminating swing connections. The mixproof valves absorb the function of manual pipe swing connections into automatic, air-operated valve technology. This eliminates the need for in-person labor. This also allows for faster changeover, easier product-to-product transition and easier product-to-clean-in-place transition.
Reduced waste
Additionally, when swing connections are eliminated, users eliminate drip points and minimize product waste. Mixproof valves allow the product to be flushed to the destination and offer virtually spillage-free operation. For expensive products, the cost of spillage can be high. This technology can cut out unnecessary product loss.
Faster changeover
With faster changeover from mixproofs, users remove the need for total system cleaning and can clean each system individually. This creates increased use of assets and scheduling flexibility. Plants can be modeled to run 24/7, and tanks and piping can be turned over faster.
Elimination of process cross-contamination
Swing connections have the potential for error, and single seat valves can allow products to mix in certain conditions. Mixproof technology eliminates the need for manual swing connections and enables the simultaneous flow of two different products or fluids through the same valve without cross-contamination. These valves ensure secure, efficient and automated routing and changeover of incompatible enemy fluids in hygienic applications.
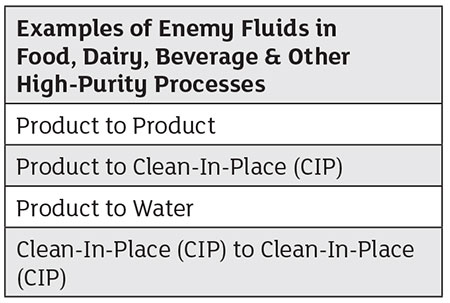
Extension of shelf life
A mixproof valve’s impact on extended shelf life involves a combination of factors: system design (easier to clean), valve design and elimination of swing connections. When swing connections are removed from the process, the system does not have to be opened after cleaning, reducing the bacteriological contamination that occurs when exposing the system to plant air and human contact.
Mixproof Valve Applications
Mixproof valves have been used in the dairy, food and beverage industries for more than three decades. The technology has been tested, proven and accepted by the Pasteurized Milk Ordinance and is becoming a standard, particularly in dairy processing facilities. The change is driven by the payback and product improvement.
Mixproof valves work well in a number of sanitary processing applications throughout food, dairy, beverage and other high-purity processing facilities, such as:
- fluid tanker reception and cleaning
- transfer to storage
- raw and pasteurized product routing
- high-temperature, short-time systems
- extended shelf life and aseptic systems
- tank and line clean-in-place systems
- cleaning solution routing valves
Mixproof valves can increase production and minimize cleaning and downtime, without adding additional processing or filling equipment. Although the advantages of mixproof valves are numerous, they are not a fit for every application. The system design requirements to incorporate mixproof valve technology can be complex and the initial investment costs can be high. It is best to consult an experienced integrator for consultation when considering mixproof valves.
In order to maximize the benefits of the valves’ flexibility and efficiency, they are frequently installed on automated skidded systems. Automation helps ensure repeatability, protects product integrity and increases uptime, all resulting in faster payback. Users should consider automation when looking at this technology.
For large-scale food, beverage or dairy processors looking to automate and enhance processes without risking cross-contamination of fluids or adding additional equipment, mixproof valves should be considered. The valves two-seat design offers flexibility and opens the door for other subsequent benefits.