These advanced components connect with a networked automation system and provide more control and safety for protecting pump systems.
Eaton
03/23/2017
Modern motor control technologies have surfaced that address evolving smart pumping system requirements. They protect pumping systems by simultaneously providing a new level of diagnostics, energy awareness and control, as well as by enhancing operator safety.
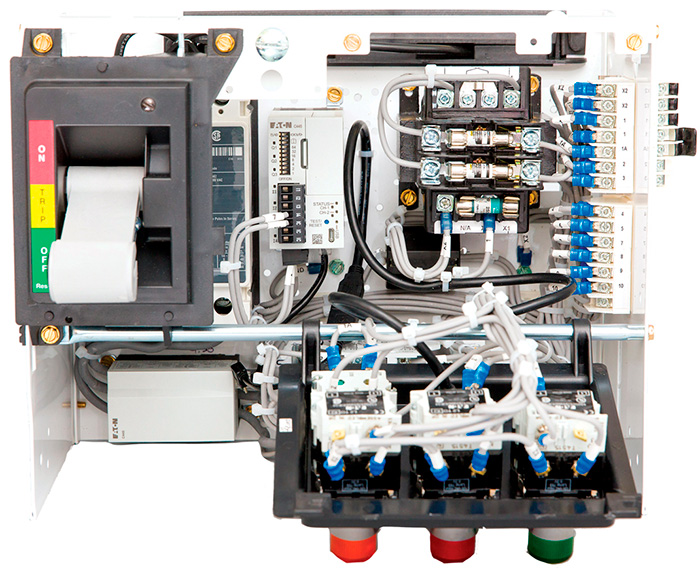
Motor Management Relays
Many new options are available when it comes to protecting pumps from various issues associated with motor overloads. Motor management relays are one example of an emerging technology that enables improved diagnostics and intelligence of pumping systems without requiring a complete overhaul of the distribution and control system. These motor management relays increase energy awareness, improve diagnostic capability and enhance uptime through excellent monitoring and protection. These devices communicate on all standard industrial protocols and provide performance data on entire pumping systems. Unlike legacy overload relays, motor management relays contain features such as real-time clocks, non-volatile memory backup, motor temperature protection, efficiency monitoring, fault queues, trip snapshots and optional algorithms that provide automatic restart after an outage. These relays are also capable of remote configuration and monitoring, which contribute to operator safety. Another example of product evolution in the smart pumping space is in drives technologies. Drives can support communications and save energy costs in the process. The general-purpose drive incorporates an energy-control algorithm, extensive onboard industrial communication protocols and built-in harmonic reduction to help reduce the cost of using a drive for pump control.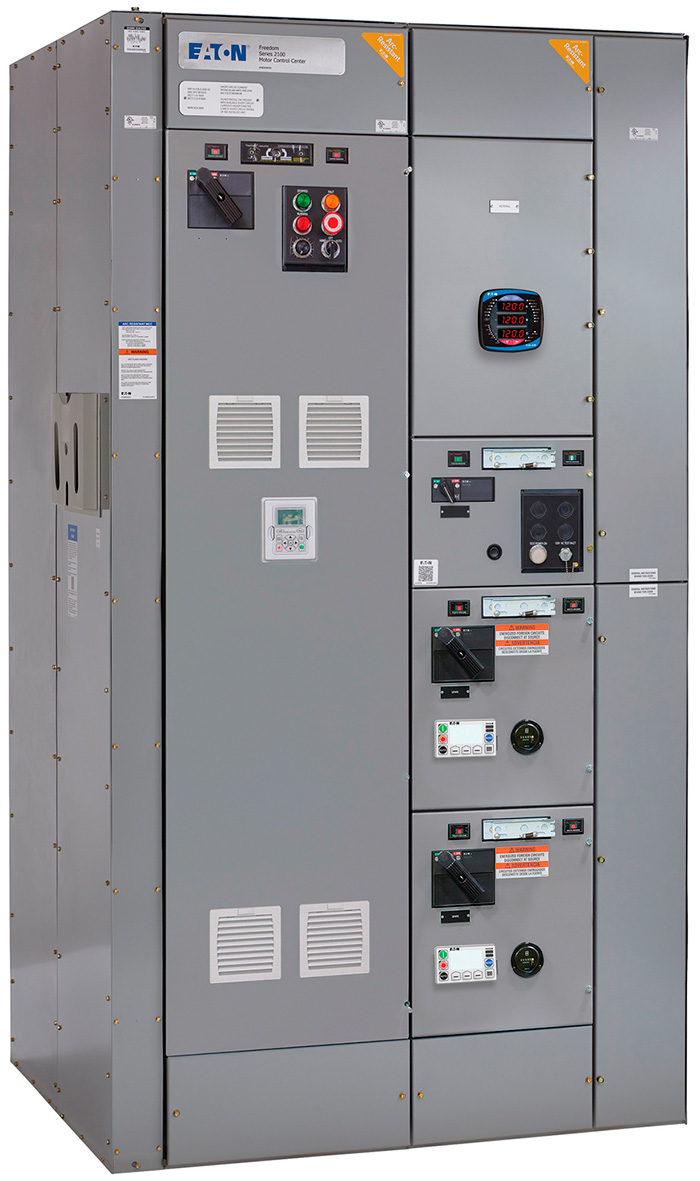
Enhancing Safety
Two of the most common requests in MCC technology are for product longevity and safety during maintenance. MCCs require regular maintenance and have higher instances of user interaction than most other electrical equipment. When there is an issue and personnel must perform maintenance, some MCC product features can help protect workers. Arc flash safety is one of many requirements that continues to evolve in power distribution and controls. For example, arc-resistant designs engineered to contain arc blast energy are no longer limited to switchgear. MCCs are available with a Type 2 accessibility rating, which means that arc-resistant designs are present on the front, back and sides of the assembly. This rating translates to enhanced safety around the entire perimeter of the MCC if an arc flash event occurs. Arc flash safety solutions found in today’s MCCs are specifically designed to help reduce personnel risk during maintenance. Industrial circuit breakers address this in MCCs through technologies that reduce the energy available during an arc flash event. Safety remote racking mechanisms can be found within modern MCCs, providing bus isolation, stab indication and lockout features that proactively prevent the initiation of an arc flash event during maintenance operations. Global manufacturers have the expertise to design and build components that assimilate well into smart, communicating pumping systems. Because of networked devices such as drives and motor management relays, end users can be sure that they have the information they need to run a safe and energy-efficient remote pumping installation. In the case that maintenance is required, they can be sure that their personnel will be safe as they interface with modern MCCs.
To read more Motors & Drives articles, go here.