The changing properties of wastewater and other fluids can cause unexpected pump performance.
02/03/2015
Knowing a fluid’s viscosity is essential to properly sizing piping and pumps. The viscosity of all fluids changes with temperature—the higher the temperature, the lower the viscosity. For Newtonian fluids, only temperature changes viscosity. However, non-Newtonian fluids’ viscosities also change for other reasons. Understanding these reasons is critical to efficiently pump this common type of fluid.
Time-Dependent Viscosity Changes
Thixotrophic fluids thicken when sitting but thin over time when stressed. A single sharp impact does not appreciably reduce a thixotropic fluid’s viscosity. However, continuous shearing usually thins the liquid. Examples of thixotropic fluids include many wastewater sludges, drilling fluids, paints, flocculants, bentonite mixtures, honey, molasses and ketchup. Most thixotrophic fluids are also shear-thinning, meaning the force and the length of shear time reduces the fluid’s viscosity. Rheopectic fluids do just the opposite. They get thinner when sitting and thicker when stressed over time. Printing ink is one example, but rheopectic fluids are fairly rare.Time-Independent Viscosity Changes
Pseudoplastic, or shear-thinning, fluids’ viscosities decrease with the force of stress. Most shear-thinning fluids are also thixotropic. Ketchup is a good example of this type of fluid. When trying to get ketchup out of a glass bottle, usually the bottle has to be turned upside down and shaken or hit. A combination of sufficient force over sufficient time is required to reduce the ketchup’s viscosity enough for it to flow. Dilatant, or shear-thickening, fluids’ viscosities increase with the force of stress rather than the length of time of stress. A familiar example is the silicone-polymer toy Silly Putty, which is very soft in the hand but becomes hard when thrown down. Most dilatant fluids are also rheopectic. For example, turning cream into whipped cream takes the right combination of time and force.Implications for Pump and Pipe Sizing
To effectively size pumps, motors and piping to meet performance specifications, operators need to know the minimum and maximum viscosity of fluids. Viscosity can affect pump suction and discharge pressure requirements and pump performance.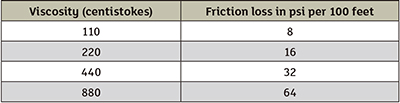
Modeling Non-Newtonian Effects for Wastewater
Figure 1 shows a practical way to model friction losses for wastewater sludge. The chart is taken from the Environmental Protection Agency’s (EPA) Standard 625/1-79-011. The thicker a particular type of wastewater sludge is, the greater its viscosity.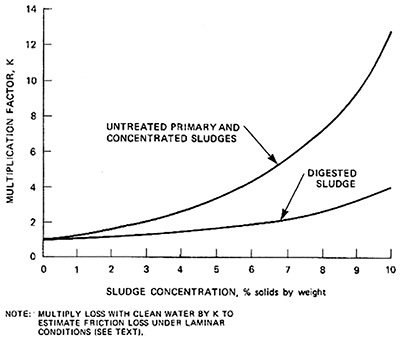
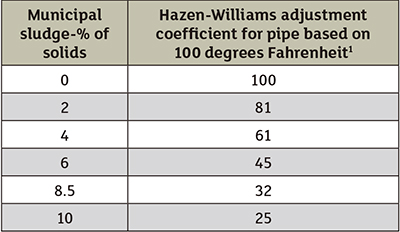