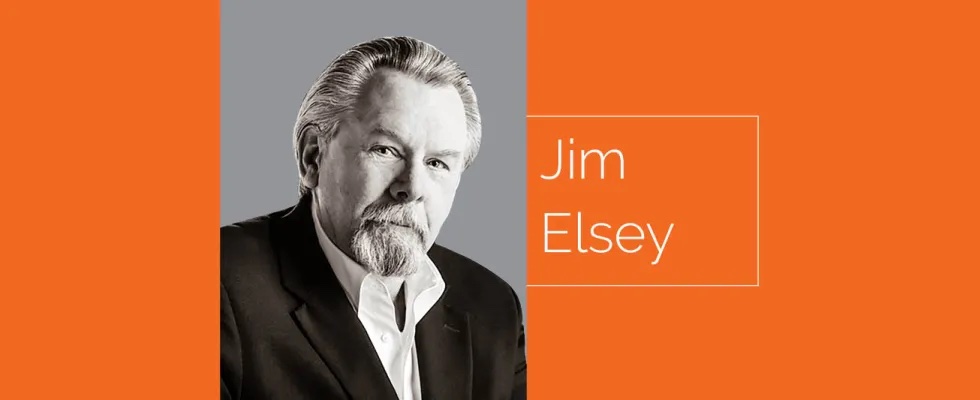
Here I go again, writing about net positive suction head (NPSH). I persistently harp on this subject because I frequently witness NPSH problems in the field. To paraphrase the words of the famous psychologist Carl Jung, “what you resist, will persist.”
You may believe that NPSH is something you can check and forget, but do you realize that both the system’s NPSH available (NPSHa) and the pump’s NPSH required (NPSHr) are continually changing over time? It’s like the air pressure in your car’s spare tire—forgotten in the trunk.
Yesterday’s NPSH margin may not be sufficient today. Don’t get caught with a flat spare tire or insufficient NPSH.
Background on NPSH: Energy & Pressure
Confused by the term NPSH? Think of it as a required energy level to prevent most cavitation. Pumps require a certain amount of NPSH (energy) to satisfactorily operate at a given point of head (pressure) and flow on the performance curve. These points are empirically determined by the manufacturer (sometimes calculated) and are noted as NPSHr.
The suction side of the pump system must, in return, provide a certain amount of NPSH (energy), and that is referred to as NPSHa. There must be more NPSHa than NPSHr for the pump to operate satisfactorily.
The difference between the two is referred to as the margin or ratio. Refer to Hydraulic Institute (HI) 9.6.1-2017 for more information on NPSH margins and ratios.
NPSH Tips to Keep in Mind
NPSH changes with a number of things, including:
Impeller diameter: For the same flow rate on a given system, an impeller of a smaller diameter will have a higher NPSHr. For proof, check it on a pump selection program. Use the same flow rate over a selection of four to five heads.
This phenomena occurs for several reasons and most are complex. The main reason has to do with a mismatch in the relative velocity of the fluid at the inlet of the impeller as compared to the outlet. Note that the higher the specific speed (NS) of the impeller design, the more the effect will occur.
Another often overlooked factor is a simple math axiom. NPSHr, also known as NPSH3, is normally defined as a 3 percent head drop at a fixed flow rate for the pump. A 3 percent head drop with a smaller impeller (implies lower head) is a smaller number than a 3 percent head drop of a larger impeller (implies higher head). In essence, what this result demonstrates is that, by default, pump manufacturers actually allow for less cavitation on smaller diameter impellers. Terry Henshaw, in one of his many outstanding articles, (Pumps & Systems May 2009) discusses this industry disjunct in more detail.
Clearance of impeller and wear rings: Over time as the clearances open up on the pump, the NPSHr will also increase. This effect is significantly worse for closed impellers than open or semi-open styles. A closed impeller that uses wear rings can have an increase in NPSHr by as much as 40 percent due to wear in the critical clearances. The main reason this increase in NPSHr occurs is recirculation flow at and near the impeller eye.
Vane geometry: Specifically, the leading edge profile of the pump impeller vane. The shape of the leading edge will affect NPSHr.
In descending order of best to worse shape include:
- Parabola
- Ellipse
- Circular
- Blunt
You may have unwittingly changed the profile due to maintenance mistakes (during impeller removal or installation), under or over filing the vanes or during machining or balancing operations.
Speed: This is not 100 percent true across the entire curve range, but for small speed changes, NPSHr will vary approximately as the square of the speed ratio for the pump in the midrange operating region and areas near the best efficiency point (BEP). NPSHr increases with speed and vice versa. This is normally not an issue except on variable speed systems and/or systems where parallel pumps are automatically controlled by downstream system parameters. When programming the software or programmable logic controller (PLC), make sure the first pump started does not run out on its curve prior to the second pump startup.
Viscosity: Yes, an increase in viscosity will increase the NPSHr and decrease the NPSHa. A correction for viscous fluids must be calculated and used. I recommend corrections for all liquids with a viscosity over 40 centipoise, but you should be looking at the potential ramifications at viscosities even lower.
In one word, the culprit is friction.
As explained in this excerpt from my November 2017 Pumps & Systems article:
“Intuitively, you would think that changes in viscosity will affect NPSHr (aka, NPSH3), but most published empirical data disputes that line of thinking. On pump suction line applications where highly viscous fluids have issues flowing in the pipe to the pump suction come to mind, but these issues would normally be covered in the friction component of the NPSHa calculation. That is, the friction factor would be higher for the viscous fluid and consequently reduce the NPSHa. My advice on viscous fluids is to increase the margin between available and required NPSH.
Several well-respected (but older) reference books state that there is little to no evidence that viscosity affects the NPSHr (NPSH3) value. The new edition of the ANSI/Hydraulic Institute guideline 9.6.7 states that an analytical approach may be considered (refer to section 9.6.7.5.3 [2015] of the guideline). The guide offers an equation to calculate a corrected NPSHr (NPSH3).
To quote one paragraph from this section: ‘There is a dual influence of the pumped liquid viscosity on NPSH3. With increased viscosity the friction goes up, which results in an increase of NPSH3. At the same time, higher viscosity results in a decrease of air and vapor particle diffusion in the liquid. This slows down the speed of bubble growth and there is also a thermodynamic effect, which leads to some decrease of NPSH3.’”
Air entrainment: Air entrainment in a range of 0.3 to 1 percent will work to help mitigate the NPSH issues, but above 1 percent, the NPSHr will increase.
Age of system and pump (fouling and corrosion): As systems age and/or foul, the flow velocity profile and the friction will increase. This could be due to marine growth such as zebra mussels or simple general corrosion and pitting of the metal pipe.
Both factors work to reduce NPSHa and increase NPSHr. In some systems, this fouling process can take years, and in others, a few short weeks. Note that a clogged suction strainer can happen in minutes.
Suction pipe geometry: For every elbow, valve and “tee” in the suction pipe, the downstream fluid velocity profile becomes more turbulent. The turbulence creates a mismatch/discrepancy in the fluid velocity when compared with the impeller inlet vane velocity. This mismatch creates flow recirculation and eddy currents at the impeller eye. This chaotic mix of velocities and flow profiles affects NPSHr in both a direct and negative manner.
Sometimes just a simple change, like the drill and tapping of the suction flange/nozzle to add a gauge/transducer or other instrumentation, will cause an increase in NPSHr.
Static head or pressure head: You may have calculated worse-case static and/or pressure head considerations when the system was first designed, but I frequently see pump issues occur because the system is presently being operated differently than what it was designed for. As a matter of fact, this is one of the most common issues I experience across the board.
Temperature and elevation: As I have often stated, “the NPSHa formula is your friend,” when you are trying to calculate or manage NPSH issues.
Referring to the formula, you should easily understand how a change in temperature will affect both the vapor pressure and the specific gravity. I already covered viscosity, but please note viscosity is in a direct relationship with temperature.
Elevation above sea level is not a common issue except perhaps on portable units or when equipment is moved from one site to another. Remember, the elevation above sea level will change the absolute pressure. (Equation 1, page 22)
NPSH margins: Please understand that all centrifugal pumps with adequate NPSH margins (as defined by HI) where the NPSHa exceeds NPSHr can still experience cavitation. This is because the margins, in spite of their magnitude, are not sufficient to preclude 100 percent of the cavitation.
You could have a pump that has 10 to 50 feet of positive margin or even more and it will still cavitate. The NPSH inception (NPSHI) point could easily be 100 feet or more in some cases. I have experienced several high-energy boiler feed pump designs (multistage) in the over 20,000 brake horsepower (bhp) range where normal NPSHr at BEP would be 200 feet or more, but the suppression of all cavitation in the first stage would require over 1,000 feet or more.
Last Hors d’Oeuvre
Know that NPSHr increases as you approach the left side of the curve and minimum flow restrictions. It increases exponentially and at a higher rate than the square function witnessed in the midrange. This reversal of the curve geometry is rarely if ever illustrated on the manufacturer’s curves. This is usually because they don’t want you to operate in that region where radial forces are highest, thermal considerations are necessary and flow is turbulent and mismatched to the impeller inlet vanes.
Conclusion
NPSH, like the questionable air pressure in your car’s forgotten spare tire, will change over time.
While you resist the effort required for the reliable solution, and when you least need the aggravation, the problem will persist.
References
(1984) TAMU Pump Symposium Proceedings: Does Impeller Affect NPSHR? by Daisude Konno and Yoshiyuki Yamada