Editor’s Note: This case study is provided by a pump advisor for Turbomachinery Lab at Texas A&M where students are exposed to hands-on experiences, providing them pump training in the field. In this article, students learn the importance of doing the math. A call came from a regional engineering manager in a Connecticut-based facility two winters ago, inquiring about an operational issue with a No. 2 fuel oil pump feeding a power generation boiler. It would not pump like it should. The problem had a sudden onset, which coincided with a dramatic flow rate drop, increased vibration, loud noises and overheated pump case. This was all amid a cold spell, when it was necessary to generate additional power. After some discussion about the layout and the symptoms, the “why” became clear. The cold weather caused the viscosity of the fuel oil in the long, outdoor suction line to increase until the net positive suction head required (NPSHr) by the pump could no longer be met. It was an NPSH problem.
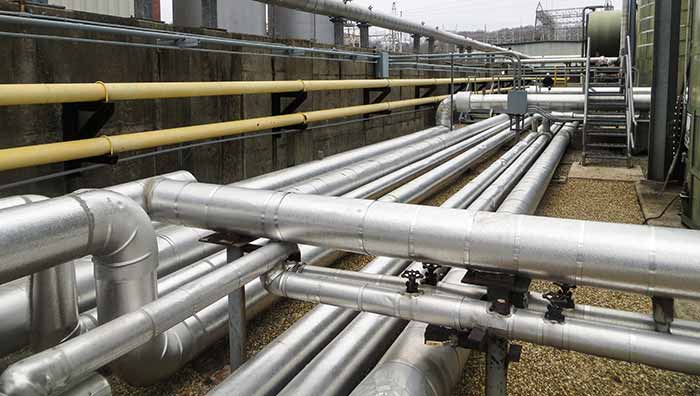
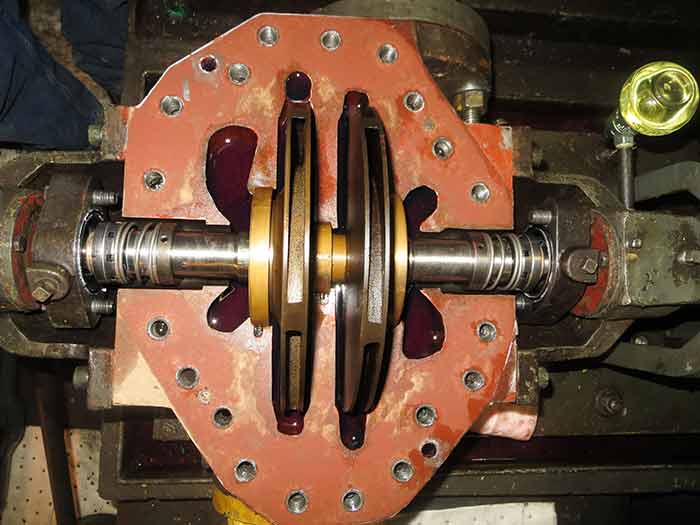
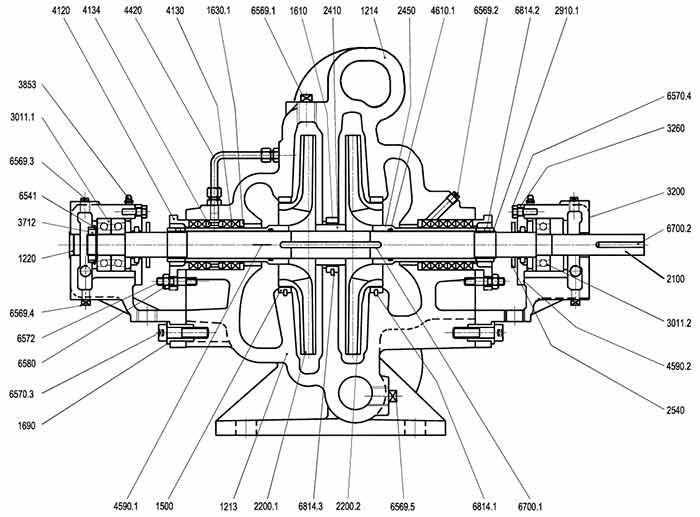
- Residence time in the suction pipe exposed to the cold was reduced, thereby reducing the risk of waxing.
- The pump minimum flow recirculation was now activated and functional, such that the pump would run closer to 65 percent BEP. This was a significant improvement over the former 25 percent.
- Major reliability improvements were made possible for minimal investment.