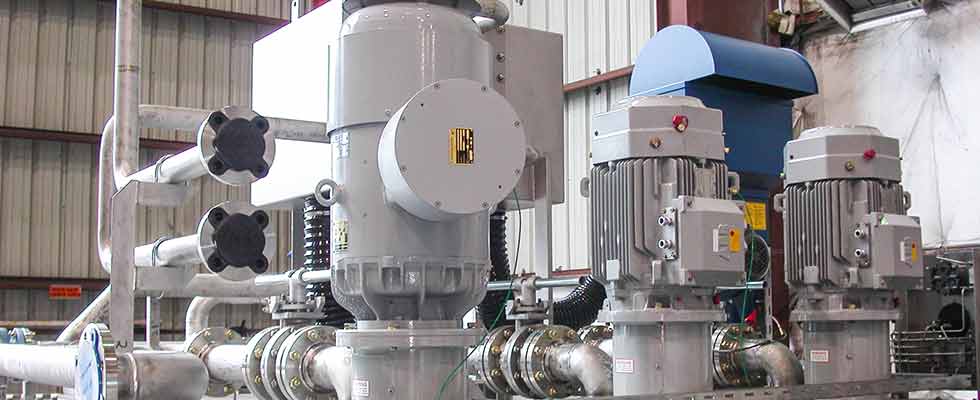
The circulating lubrication oil system is essential for cooling and lubricating all kinds of rotating machinery. In typical train steams or gas turbines, diesel engines, reduction or step-up gears, compressors, generators, pumps or expanders could be included. The oil system includes a number of components for which the pumps provide adequate flow and pressure—such as the gears, journal and thrust bearings in the machinery. The cooling and filtering of the oil are equally dependent on pump flow and pressure to function properly.
Depending on the application, different system alternatives are used. The systems in process service are designed and built per standard API 614; however, in the case of power generation they are often designed and built per the OEM’s standards.
This article will deal with the pumps and how certain system conditions, such as air entrainment, can upset the pumping function and lead to a slow down or shutdown of the machinery it is intended to serve. In order to prevent machine damage, several steps of protection must be included. The article will also compare how different pump technologies are more or less suited for dealing with air entrainment, and how one OEM decided to change from a hydrodynamic, or centrifugal, pump to a positive displacement, or screw, pump.
Air Entrainment in Lube Oil
As the oil passes through a number of lubrication points in the machine, air will be absorbed in the lube oil, which under atmospheric conditions already contains about 5 percent dissolved air. The air entrainment will develop sometimes substantially with splash or mist lubrication, which is often the case with engines and gearboxes.
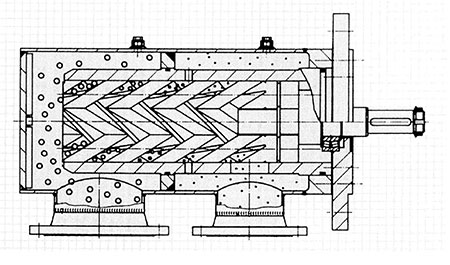
As the oil returns to the lube oil tank, which is normally at atmospheric pressure, most of the air is released and vented off. The rate of air release depends on many factors such as the tank volume and the resulting retention time, the design of the tank including baffles and any additives used to prevent foaming and improve air release.
As seen in Image 1, the transformation from dissolved and entrained to free air in lube oil is largely dependent on the pressure. In the system, the circulating oil pump will draw oil under suction pressure, which will dramatically increase the presence of free air. The suction line—including strainer and restrictions from valves, elbows and piping—results in a pressure drop before the oil enters the pump. The oil will have an increasing amount of free air when it enters the pump.
Additionally, a small pressure reduction always occurs as the oil enters the pump and the pumping elements and a significant amount of free air can break out as a result of the pressure drop.
To facilitate the installation and reduce constraints from the suction piping arrangement, most lube oil systems today use vertical tank-mounted pumps, which differs significantly from the “classic” API 614 system with its skid, lube oil tank and horizontal, free-standing pumps. The tank-mounted pumps make for a space-saving system, allowing the pump to be either submerged or—using a short suction pipe—directly in the tank.
Effects of Pumping Air Entrained Lube Oil
The most common pump is the hydrodynamic or centrifugal pump. It has a number of advantages with regard to simplicity and cost and can be installed vertically in a lube oil tank as a sump pump. Normally a mechanical shaft seal and a pressure relief or safety valve is not required.
The centrifugal pump is less sensitive to impurities and the alignment of the motor and is always fixed by the piloted mounting flange and adapter.
The other most-used pump type in lube oil systems is the screw pump, which is in the positive displacement pump family. Typically for lube oil systems, a three-screw pump is used. It has three rotors, one power rotor and two idler rotors surrounded by a supportive liner in which the rotors are running. In comparison to other positive displacement pumps, the flow is smooth and pulsation free, and it is also known for good suction characteristics even with cold and viscous oil. As a positive displacement pump, a relief valve is an integral part of the pump arrangement.
With regard to complication from air entrainment by dissolved and free air, the two pump types behave differently. As the oil enters the centrifugal pump, the sudden pressure drop at the inlet and in the eye of the impeller will turn the dissolved air into free air, which could block the pump (also called vapor locking).
Even with vented and properly designed oil tanks, the acceleration of the inlet flow will cause air to break out. Before vapor locking takes place, the reduced density of the oil/air flow will limit the pump flow and pressure buildup ability.
The result will trigger a low oil pressure alarm and possibly a shutdown command from the control system. The standby pump will be called into action and, if it is able to overcome the opening pressure of the downstream check valve, hopefully no harm is done.
The screw pump behaves differently, and pressure buildup is only related to system back pressure, not to density. However, increased free air will somewhat reduce the pump flow, which has to be taken into account when deciding the pump capacity.
Listening to noise and vibrations in the pump can help identify air entrainment. This is sometimes incorrectly referred to as cavitation.
Contrary to conventional cavitation, which is related to inlet velocity, there is normally no harm done to the pump. It more closely resembles multiphase pumping, where the two-phase inlet stream turns into single phase as the pressure increases.
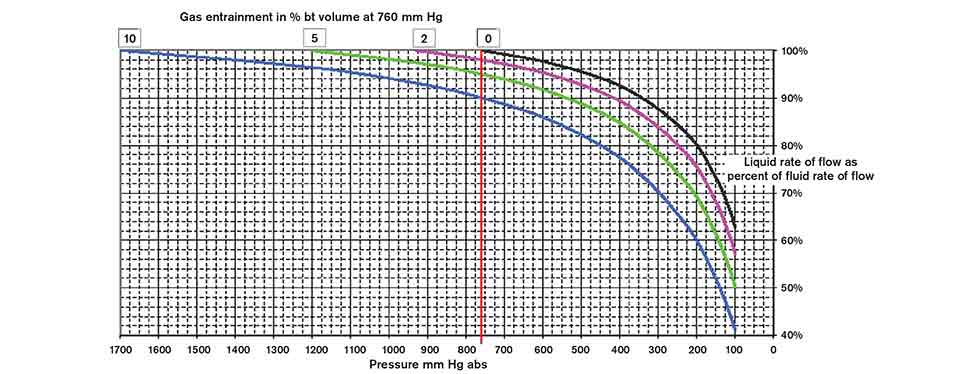
The successive pressure buildup along the rotors will collapse the air bubbles, which go back into a dissolved state as a single-phase fluid (Image 2). The graphic shows how a small return flow from the discharge pressure side is injected in the rotor profile. By “filling” the air bubbles with liquid, the forces from the implosion of the bubbles will be reduced and noise and vibrations eliminated.
Case Study
A large OEM and manufacturer of rotating machinery had for a long time used vertical centrifugal pumps for lube oil service due to cost and simplicity. In an effort to limit oil tank size and also add more oil flow (as the machine power was uprated and more cooling was needed), the centrifugal pumps ran into difficulties with lube oil air entrainment.
Frequent trips and shutdowns caused the OEM to look at positive displacement pumps or, more precisely, three-screw pumps. However, the limitations of installation space and connections imposed on the three-screw pump made it necessary to customize the pump and also include a relief valve, which the centrifugal pump did not need.
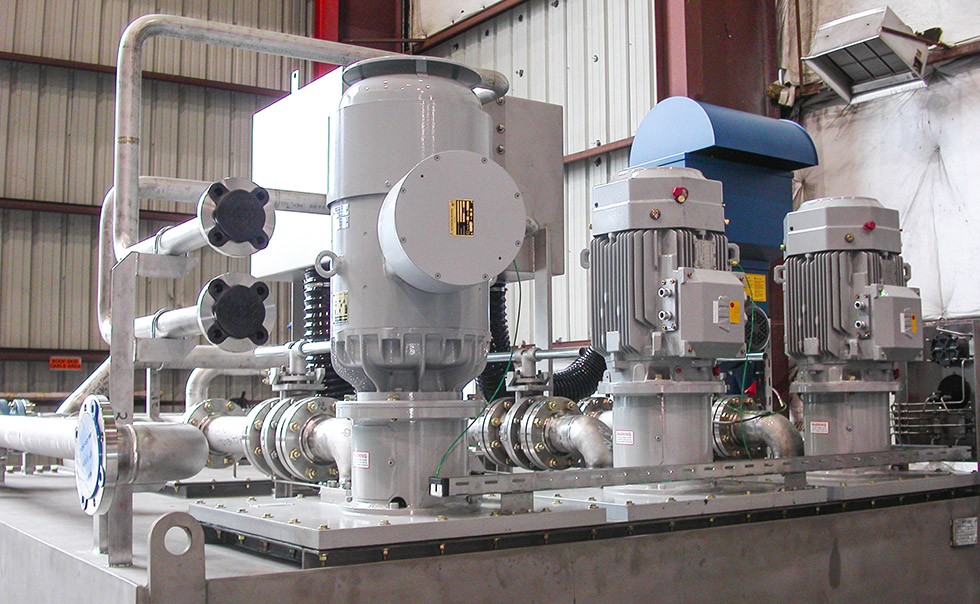
Even with the confined space and installation arrangement it was possible to replace the two centrifugal alternate current (A/C) and direct current (D/C) driven lube oil pumps with three-screw pumps (Image 3).
The three-screw lube oil pump can be a good choice when air entrained lube oil is pumped. Attention to energy efficiency and cost-effective rotating machinery designs often means reducing the lube oil volume and using more energy efficient lubrication, which also can result in less retention time for air release.
Subsequently, the lube oil pumps must be able to handle more air without interruption and provide added flexibility to deal with more demanding lube oil systems. In many practical examples, screw pumps have shown to successfully meet such demands.