Technology that senses initial rags can catch the impeller and clear them before buildup occurs.
DERAGGER Inc
01/15/2019
Clearing detrimental materials such as rag balls before they cause harm in a system increases the efficiency of pumps, which reduces energy consumption and cuts operational costs.
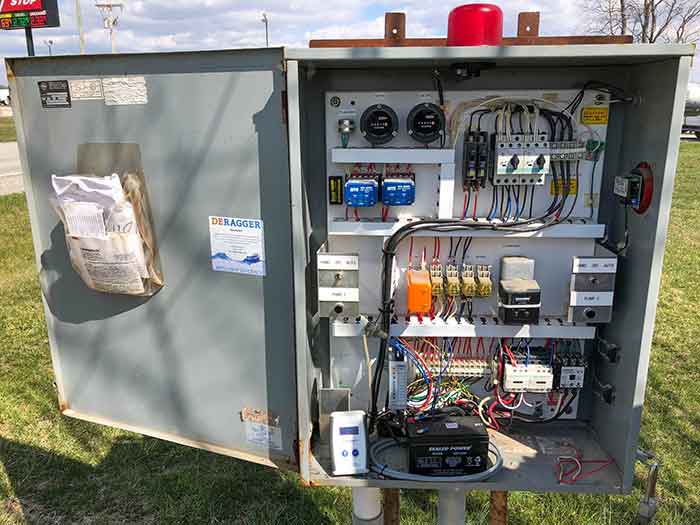
What Are the Benefits?
Keeping a pump running clean can bring many benefits:- With reduced lift and cleans required, significant savings to staff time and costs can be achieved. Recently the city of Palestine, Texas, for example, calculated a savings of $100,000 in eight months. Time previously spent cleaning pumps can now be spent on other maintenance tasks.
- Risk to employees is reduced as the systems handle less raw sewage, and fewer exposures of personnel to sharps or needle sticks occur.
- Cleaner pumps and fewer blockages reduce risk of overspill.
- Issues like advanced bearing or seal wear are detected, alerting the operator prior to equipment failure and allowing maintenance to be planned in advance.
- A recent independent study by the Water Research Centre (WRc) also found a reduction in overall runtime, even on stations that had previously been reported to be “nonragging” stations. Of course, any decrease in runtime will reduce energy costs and can be directly related to improvements in asset life.
What Are the Alternatives?
Many choose to install choppers or grinders to solve the problem of pump ragging. However, particles created by grinders and choppers can pass through headworks screens and cause problems in treatment plant processes. Trying to use timed reversal or high-current set-points to clear blockages can be risky. The amount of debris inside the pump at the point of reversal is unknown.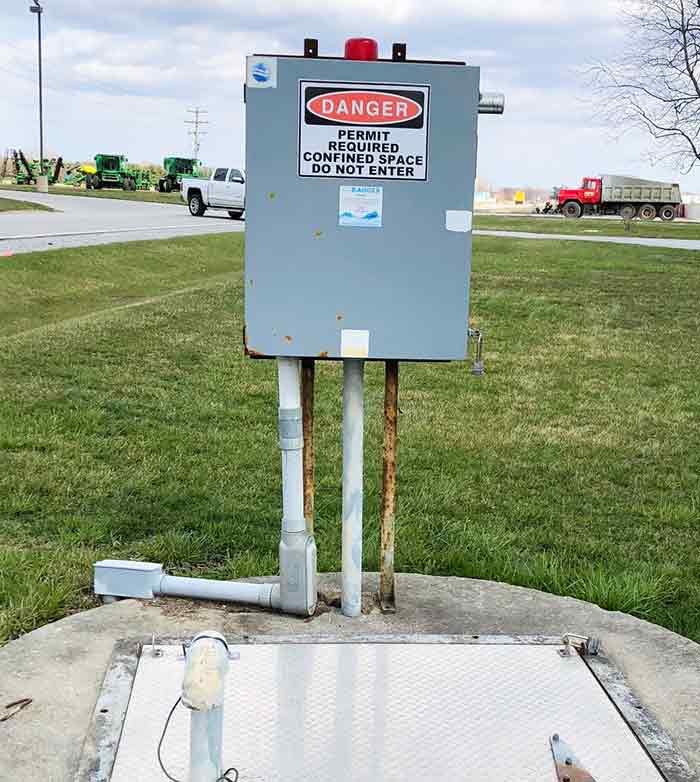