Wastewater collection systems are difficult to monitor, control and operate, but solutions are available.
Endress+Hauser
10/05/2016
Ideally, the flow of wastewater from collection points at residences, offices and commercial establishments to wastewater treatment plants would be completely gravity-powered. This is rarely possible because of economic or physical limitations. The most common challenge is flat terrain, which cannot easily be graded to promote wastewater flows. As a result, lift stations must be employed to move wastewater to a higher elevation and eventually to a wastewater treatment plant (see Image 1). A typical wastewater collection system in a county or large city will have hundreds of lift stations, with smaller lift stations feeding into larger master lift stations. These, in turn, feed wastewater to the treatment plant.
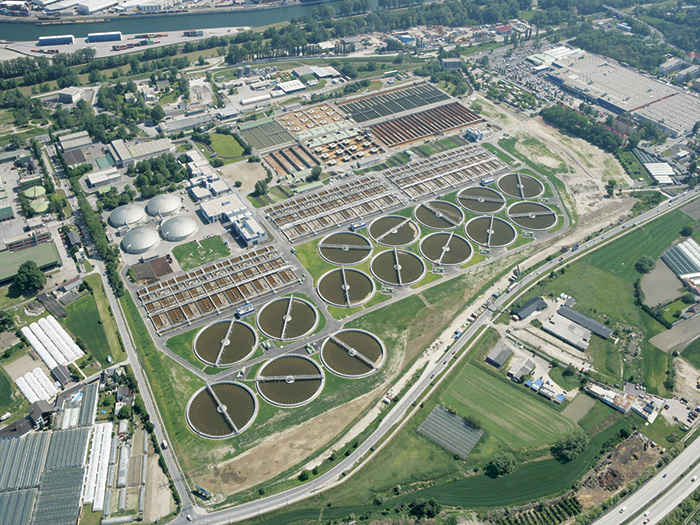
Lift Stations Controls
As shown in Figure 1, pumps are typically installed below the lowest point of the incoming wastewater feed pipe. Smaller lift stations might have a single 4-inch feed pipe, while larger stations can have multiple feed pipes, each up to 36 inches in diameter.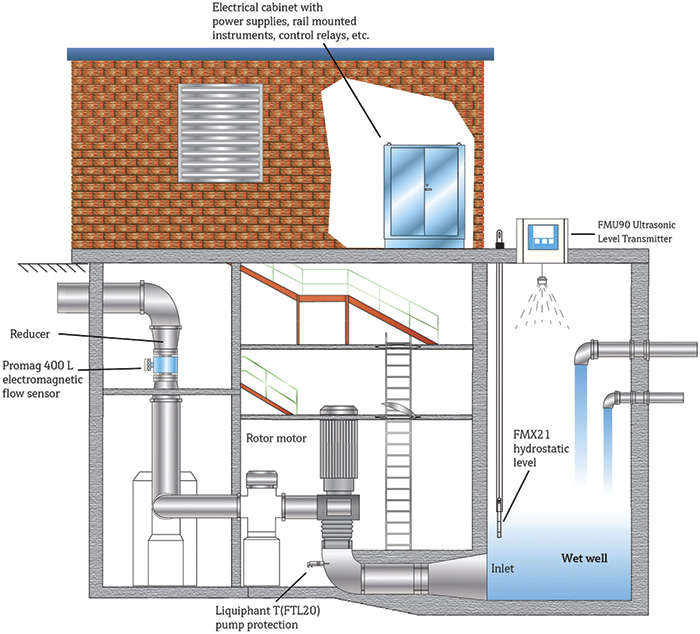
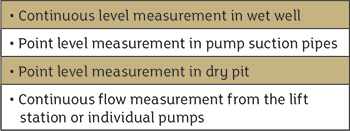
Level Measurements
Wet well level is the most critical measurement parameter in a lift station because level information is used to start and stop the pumps. Older lift stations often use a simple float switch to start and stop a single pump. But this technology is often insufficient because grease buildup and accumulation of debris can cause the switches to stick. Even when working correctly, a float switch only provides a single-point measurement, as opposed to a transmitter that gives a more informative continuous indication of wet well level. Bubbler level transmitters are an older technology used for this continuous level measurement, but they require a constant air supply and use tubes that can become easily clogged. Instead, modern lift stations use float switches for emergency backup and employ newer continuous level measurement technologies—namely hydrostatic and ultrasonic instruments. Hydrostatic level transmitters can be safely submersed in wet wells and effectively avoid float switch and bubbler issues. Hydrostatic level transmitters measure water pressure within the wet well and infer level from changes in the head pressure. Because it can resist abrasion, scratching and denting, a ceramic pressure-measurement cell is typically used with a hydrostatic level transmitter. Ceramic cells are sensitive enough to perform properly in the harsh environment of a wet well and provide accurate measurements even with the buildup that can occur on the cell. Ultrasonic level measurement instruments are non-contact devices that measure level by sending an ultrasonic signal from the top of the wet well to the surface of the wastewater.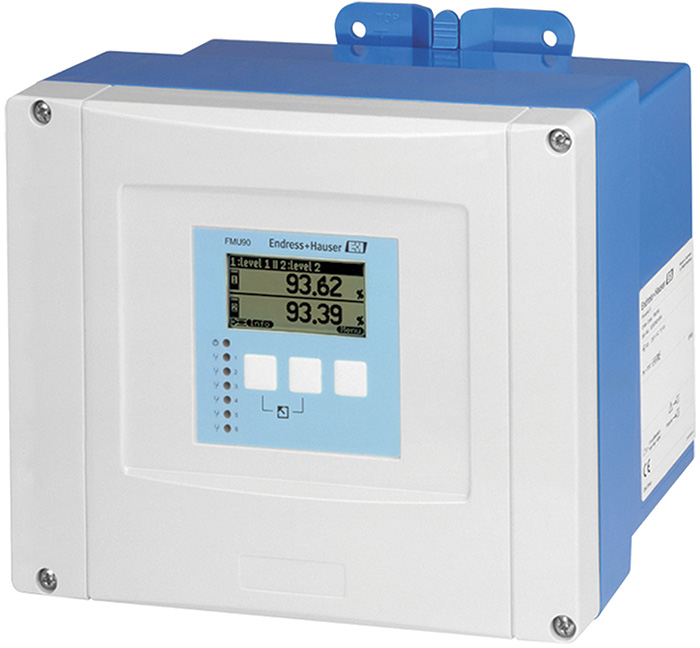