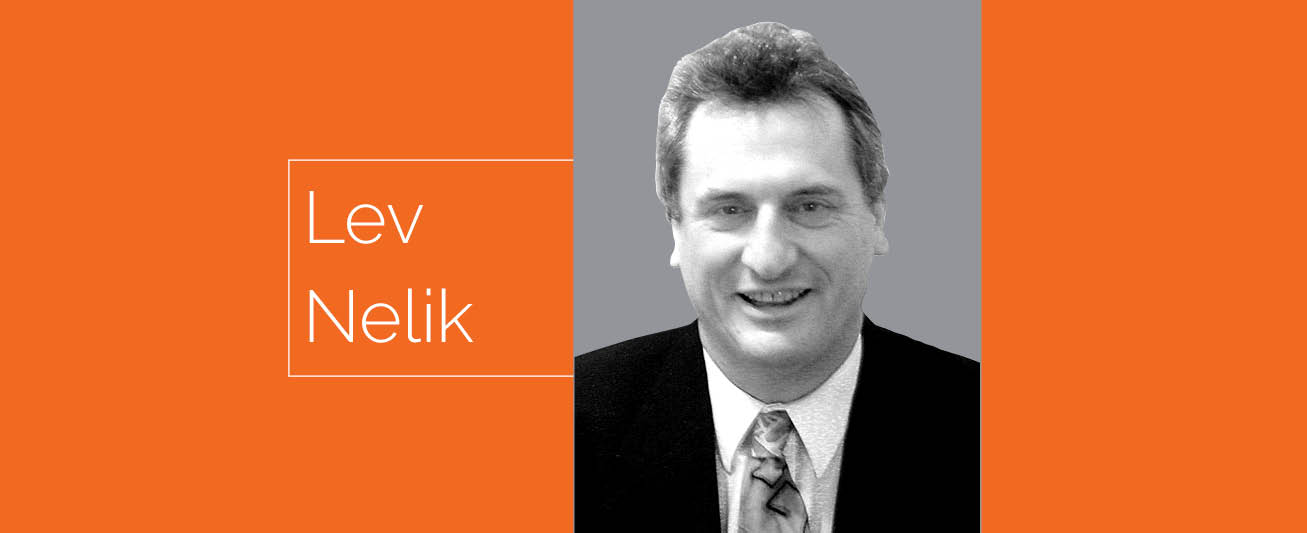
Over the years, most of my articles have focused on user-oriented aspects of pumps, i.e., real-life aspects of pumps’ performance, reliability, costs, structural integrity, vibrations and so on. On some occasions, I also published a few pump designer-oriented articles, which reflect the experiences of my own younger days as a pump hydraulic design engineer. In this article, I will touch on both—the intricacies of the “hydraulics magic” and the impact on the pump performance as a result of some “tricks” pump designers perform.
As any pump engineer who has worked at a pump company knows, no matter how hard you try, occasionally a new pump you just designed fails the performance test by being lower on expected efficiency or generating less hydraulic head. It obviously cannot be shipped to the user, so what to do?
There are two relatively simple fixes hydraulic designers know that don’t involve resorting to a major redesign, and as long as the deviation is relatively small, these fixes can save the day and meet the touch inspector’s review. These tricks are called “underfiling” and “overfiling” the impeller blades (or vanes).
Image 1 shows an example of an impeller where the exit passage (ha) is as designed (Channel 1). Note that the inlet and exit edges of the blade are rather blunt, reflecting a mass production approach to most relatively small pumps (perhaps under 500 horsepower [hp]). The blades of the impeller look similar in shape to an airplane wing, although the wings are usually designed with much greater precision via NASA airfoil shapes.
Channel 2 shows overfiling: The opening between the blades can be seen unchanged, as the removed metal is beyond the point of opening (a perpendicular line from the tip of one blade to the surface of the adjacent blade).
Channel 3 shows underfiling: Now the opening between the blades is greater (hb), as can be seen from a perpendicular taken from the (moved) tip point to the adjacent blade.
As noted, these modifications are simple and quick but produce only modest changes to efficiency and head—perhaps no more than 2%-5% depending on the specific design (for those interested in details as to why, let me know). However, for larger pump sizes, it can be a substantial economic gain. For example, a typical 1,000 hp pump, operating nonstop, would save approximately $6,000 for every point of “inefficiency” per year.
A Parting Quiz:

(H-Q) curve and efficiency (Eff-Q) curve.
1. Show (calculate) why 1,000 hp wastes the dollar amount shown above for every percentage point of “inefficiency.”
2. Make a rough plot of a modified performance curve for each case—underfiling and overfiling.
Each correct answer gives you a free, one-hour consulting on your specific similar case of performance/efficiency improvement need.