Gold fever has returned to the Yukon. The miners of the late 19th-century gold rush were drawn by tales of “easy pickings,” but they soon learned that only the best equipment survived the rigors of the Yukon’s brutal environment. More than a century later, that knowledge still holds true. In 2013, the U.S. Geological Survey reported that 231,000 kilograms of gold were mined in the U.S., with nearly 15 percent of the supply from Alaska. At $1,400 per troy ounce, large and small mining companies have returned to the Great White North. Effective and efficient water management leads to big success—and big profits—for gold mining operations. Large or small, the most successful operations rely on comprehensive plans to address ground and surface water predictions, public supply and external factors such as evaporation, precipitation and melting snow. Todd Hoffman, owner of 316 Mining and founder of the Discovery Channel series Gold Rush, said, “The right pump is probably the single most important piece of equipment for gold sluicing. You cannot find gold without water.”
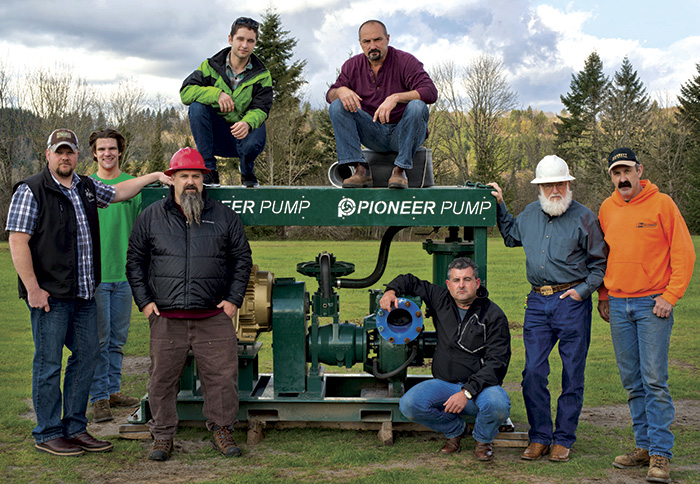
Sitting on a Gold Mine
Based in Sandy, Oregon, 316 Mining has invested recent success into process and equipment improvement, but initially, the Hoffmans spent too much capital on too little pump. Labor-intensive 3-inch portable gas pumps did not do the job. “Managing the pumps was a two-man project that was 24/7,” said Jim Thruber, processing plant manager who is responsible for separating dirt and rock from the gold. “It was challenging because we were in bear country. We had guys running out in the dark with flashlights to add fuel to the pumps and provide maintenance. It was tough. We constantly had problems with the belts slipping and breaking, fuel management and plugging.” One night while watching a Gold Rush episode with his son, a pump manufacturer employee observed the struggles that dominated the 316 Mining operation. At the end of the show, his son said, “Daddy, these guys need a good pump.” He agreed, so the next day he contacted the Hoffmans.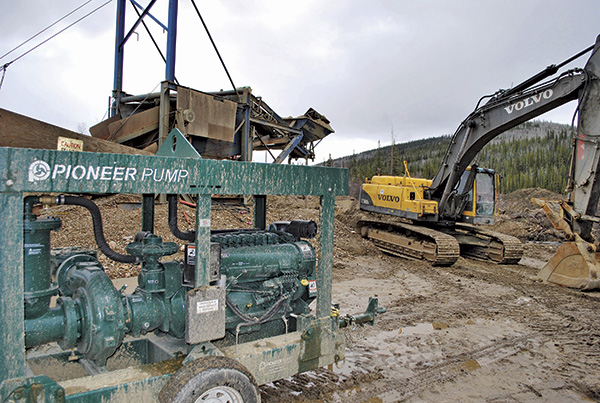
Complex Features, Simple Design
A pump with a wide band of stable operating flows was needed. The mining project made passing both large, discrete solids and suspended, abrasive fines a priority. Difficulty getting the pump close to the water source resulted in a high net positive suction head required. All these features must be combined in a durable and simple design that offered long maintenance intervals with simple maintenance procedures requiring little to no specialized tools. Some pumps are designed for rental markets in which wide operating ranges and high suction lift capabilities are required. Accommodating the passage of large solids and optimum hydraulic passage and vane profiles is a significant design challenge. Solids passage size is not simply based on measuring the outlet width of the impeller. It also includes the vane-to-vane-to-shroud clearances from the leading edges to the outlet. A key element of durability in the field is the rigidity of the pump shaft. For some pump manufacturers, raw materials do not make up a great portion of the cost of production relative to machining costs. Large-diameter, rigid shafts build in great durability for the shaft and sealing system without making the equipment prohibitively expensive. The same philosophy guides the selection of bearing sizes while ensuring that the bearings are not under-loaded, often an overlooked cause of bearing failure.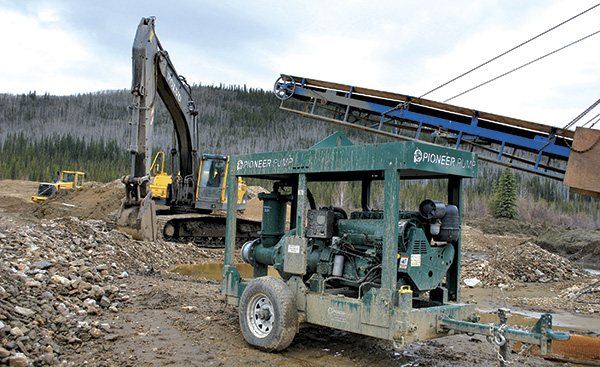