Pumps and Systems, July 2009
Within the personal care products industry, changing formulations on a frequent basis to meet marketing requirements can be costly and time consuming in terms of material use and production downtime. When personal care products have essentially the same basic ingredients, the most cost efficient production method may be to manufacture a base material (a master batch), add the various differentiating ingredients and customize the finished products as required.
Batch production is the typical processing approach for personal care products. A large percentage of all existing production plants for liquid detergents, household cleaners and personal care items operate as batch systems. All the raw materials necessary for the formulation and volume are transferred to a mixing tank, which has the advantage of high formulation flexibility for even supplementary components not included in the original formulation.
Batch production of personal care products also has disadvantages. The main disadvantages are high space requirements (the main constraint if the production capacity needs to be increased) and high energy consumption (heating/cooling) associated with treating large batches. In addition, further processing (intermediate storage/packing) may be required at the end of one batch before a new batch can be started, which restricts flexibility. Finally, monitoring and controlling temperature, viscosity and pH levels is time consuming.
Continuous production, however, opens possibilities for just-in-time strategies and in-line, continuous quality control. Step-by-step automation options, up to and including fully automated formulation management, simplify the processes for the operator, and optimal SIP/CIP procedures mean less cleaning and less waste water. With advantages including substantial cost reductions, stable quality and handling benefits, manufacturers should consider changing to continuous production methods that employ pump packages incorporating pumps, mixers, valves, tanks and control systems.
Manufacturing personal care products, household detergents and fabric softeners is similar as nearly all the products concerned have a basic formulation. Various finishing components (e.g., pigment, active matter, perfume) must be added to make a product that is distinguishable from others on the market.
Process pump packages are available that address the key issues of surfactant dilution, the production of the base material and the dosing and blending of additives needed to create the finished product. Accommodating CIP cleaning and the handling of biological materials, process pump packages can be built to a user's individual specifications from standard products or appropriate fluid handling technologies specific to the application and product range.
Employing a master batch processing system and finishing unit provides manufacturers with the ability to optimize materials and production. With a master batch system, high concentration raw materials can be used directly from tank facilities to produce the base recipe on demand and with reduced bacterial risks. The finishing unit, positioned immediately downstream, enables the manufacturer to vary production quickly and efficiently according to demand and fully optimizes all the base material.
The Art of Dilution
Whether natural or synthetic, surfactants represent a considerable percentage of the price of the finished product. Formulators and users regard the dilution of high active surfactants as desirable, not merely to maintain costs, but also to satisfy the growing demand for milder, more environmentally friendly products. For the manufacturer of several products, buying or producing a constant and varied supply of diluted active can be expensive. One major factor contributing to the high cost of buying diluted high active is the cost of transportation because the high active contains a large proportion of water. For many years, the accepted method of diluting high active to the strength required for the finished product has been to combine the raw material and water in a mixing tank. There are several problems with this method, however, such as high foaming and accurate control of the temperature to ensure that the raw material does not gel. The mixing equipment requires a high level of energy. The master batch system for toiletries and detergents addresses these issues by diluting raw 70 percent high active down to below 30 percent low active in line and on demand. The principle components of the systems are a high active storage tank, three-head metering pump, preservative holding tank, Pentax mixer, suction and discharge lines, pressure relief valve and a control panel. This equipment is mounted on a base frame with optional components such as refractometers, flowmeters or pH meters. Trace heating and lagging can also be provided to control the temperature of the high active material. The central element of the system is the metering pump, which pumps the high active, preservative and water accurately in their correct proportions. Each pump head has its own stroke length setting that allows the individual adjustment of the flow rate of any one of the liquids. If required, a separate preservative pump can be supplied to allow the preservative to be switched on or off independently of the main unit. This is significant should the user need to employ a variety of preservatives or wants to use hazardous chemicals. In operation, the water and high active are brought together by the metering pump and meet in the Pentax mixer where instant dilution occurs. This high-shear dynamic mixer takes the active down through the thick 'm-phase' at 30 to 60 percent and then below 30 percent. This requires consistently accurate raw material feeding from the pump heads and a high performance dynamic mixing system. A variety of add-on components for these packaged systems are readily available. Should the user's high active bulk storage tank not be adjacent to the dilutor unit, a force fed system can be supplied. This ensures good pump efficiency throughout any level changes in the high active tank or changes in raw material temperature/viscosity, which maintains a high accuracy solution and prevents cavitation. Systems can also be provided with a refractometer in the final discharge line for active percentage monitoring and alarm, together with active closed-loop control. Percentage monitoring and alarm allows the user to alter the stroke length of the high active pump head manually and provides automatic system shutdown in case of an emergency. For closed loop control, the active percent signal is linked to a PLC, which monitors the level accurate to +/-0.1 active percent. The final product is maintained within preset error bands via an electric stroke adjustment on the pump. Low and high active percent alarms are activated should there be a deviation from these limits, with shut down being automatic. Where required, a flowmeter is placed in the final discharge of the diluted active, reporting the flow rate of the unit at all times and allowing preset batch quantities of the active to be discharged by the unit if required.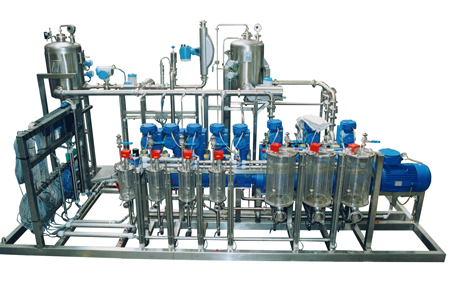