Technicians recently received and disassembled a progressing cavity (PC) sludge pump that fed centrifuges in a wastewater treatment plant for eight years without repair. The pump was still durable, but it was time for an upgrade. The Oakwood Beach Wastewater Treatment Plant on Staten Island, New York, is one of 14 wastewater treatment plants managed by the New York City Department of Environmental Protection. The plant was built in 1956 and has the capacity to treat 40 million gallons per day (mgd) of wastewater. The city has been using several PC pumps feeding sludge at 300 gallons per minute (gpm) at 35 pounds per square inch (psi) to a centrifuge for dewatering. The city had the budget to replace the pumps and moved forward with the upgrade. Eight years later, the original pumps that had operated reliably for 26,000 documented hours without even a rotor change were removed. The pumps were sent to the service center at their facility in the Midwest for full inspection and assessment.
Inspection & Assessment
The pump arrived at the facility early on a Monday morning. The pressure branch was removed, and then the stator. The rotor was noticeably worn. The rotor was measured with a caliper to determine residual stator and rotor interference. It measured 2.67 millimeters (mm), which is considered acceptable and normal wear. The high demands for performance, efficiency and resistance to erosion placed on rotors require surfaces of the highest quality. State-of-the-art machining, cutting and coating processes created the optimum surfaces. The rotor on the tested pump was made of air-hardened grade D6 tool steel with ductile coating. Only the ideal interface between the rotor and the stator guaranteed high efficiency and long life. An even compression between the two main pump elements was crucial as well.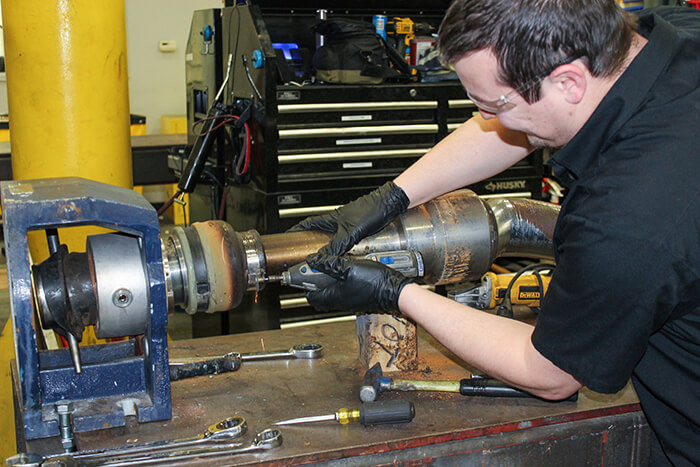
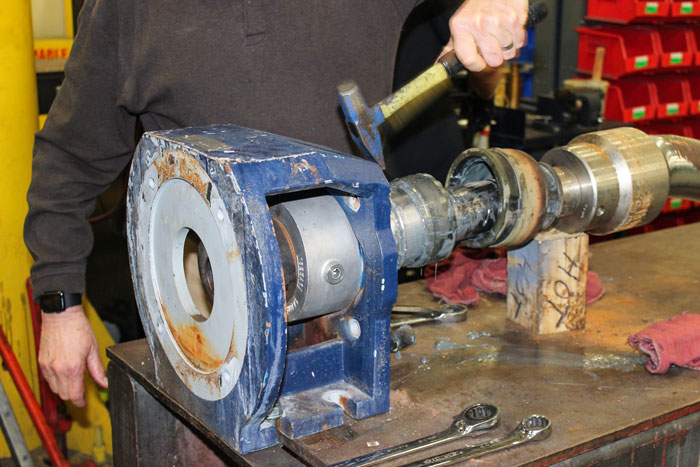