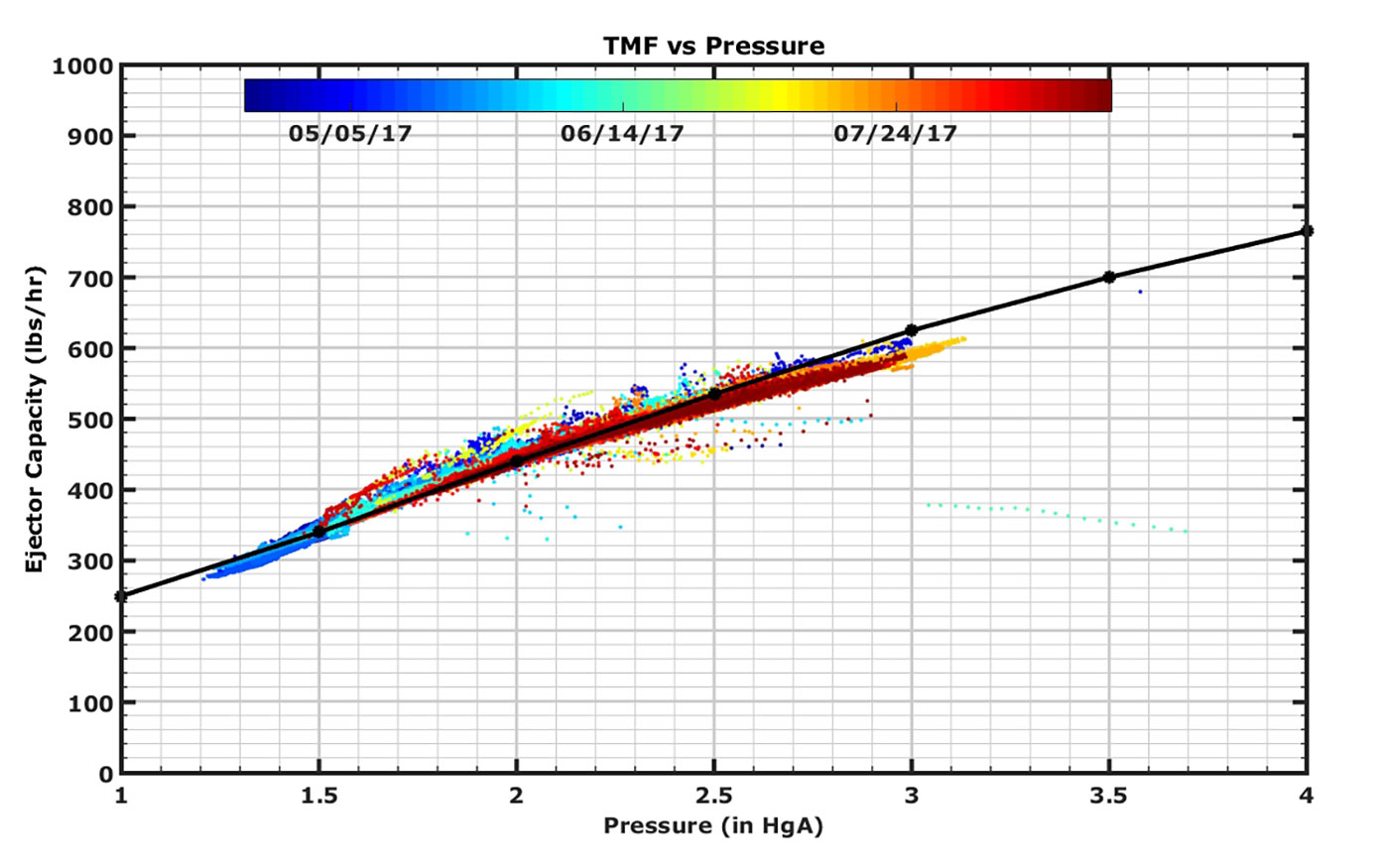
Large surface condensers are used in power plants to recycle exhaust steam and maintain proper vacuum for optimal turbine operation. Vacuum leaks within the condenser increase the operating pressure (referred to as turbine backpressure), thereby reducing turbine output and efficiency.
Vacuum pump systems are used to remove the accumulation of air and noncondensable gases within the condenser caused by leaks (also known as air in-leakage). Degraded condenser vacuum system capacity will have the same detrimental effect on condenser performance as excessive air in-leakage.
Both result in increased condenser pressure due to a regional buildup of air and noncondensable gases extending beyond the air removal section surrounding the tubes carrying the coolant used to condense the steam from the turbine. This buildup, referred to as air storage, degrades heat transfer within the area.
Typically, the design performance curve of the condenser dictates the inlet pressure to the vacuum system. As air storage occurs due to high air in-leak or low vacuum pump system performance, the vacuum system will dictate condenser pressure. This means that the condenser is no longer operating on its design performance curve, which may result in decreased plant operating efficiency leading to lower electricity production.
This relationship highlights the importance of monitoring both air in-leakage and vacuum system operating capacity. A multisensor instrument located in the air extraction line between the condenser and the vacuum system inlet can differentiate between these two conditions by providing a direct measurement of air in-leak and operating capacity of the vacuum system. The measurements provided by this instrument can be used to perform an analysis of the vacuum system performance.
Design Performance Verification
The two primary components used to generate the vacuum within the vacuum system are steam jet air ejectors (SJAE) and liquid ring vacuum pumps (LRVP). The performance of an SJAE is defined by mass flow versus absolute pressure at the suction inlet. The manufacturer provides a design performance curve showing the expected relationship between these two parameters. Actual operating performance is determined by evaluating measured total mass flow versus absolute pressure over time. LRVPs are volumetric pumps, and their performance is defined by volumetric flow versus absolute pressure. The relationship between these parameters is shown on the design performance curve provided by the manufacturer. The actual operating performance of an LRVP is determined by evaluating actual volumetric flow versus absolute pressure at the suction inlet over time.
Image 1 shows a steam jet ejector performance evaluation. This evaluation shows the measured operating capacity of an SJAE as colored data points with the manufacturer’s performance curve overlaid in black. The measured data points are colored based on a time scale revealing a performance influence from seasonal variations of temperature. The vacuum system output moves up and down along the manufacturer’s performance curve as condenser pressure changes. The measured SJAE capacity in this example agrees closely with the design curve.
Pump Set Capacity Comparison
Vacuum pump systems are typically installed as a 100% spare capacity set, where one of the SJAEs or LRVPs is intended to be in service while the other is out of service as an isolated stand-by spare. With this configuration, a quick and simple performance evaluation can be achieved by conducting a side-by-side comparison of operating capacity to identify a degraded pump. The pump capacity comparison test is performed by running one pump at a time then comparing the capacities to each other and the manufacturer’s performance curve. This can be done for SJAEs jets by observing mass flow (pounds per hour [lbs/hr]) versus pressure, and for LRVPs by observing volumetric flow (actual cubic feet per minute [ACFM]) versus pressure.
While performing the test, the generating unit load should be steady within ±2% for the duration of the test so at least one hour of steady load can be scheduled for testing. Steady conditions are maintained for at least 30 minutes to allow sufficient time for the process parameters to stabilize. Actual volume flow (or mass flow for steam jets) and pressure readings for each pump are compared to each other and the manufacturer’s performance curves to establish pump performance and to evaluate if it is degraded.
Image 2 illustrates actual operating data measured during a side-by-side comparison of two LRVPs. Measured operating parameters are shown for volumetric flow (ACFM) and pump inlet pressure (“Hga). A 0.2 ”Hga difference in pressure was noticed when operating the different pumps, which led to the belief that one of the pumps needed maintenance. By performing a pump capacity comparison test, and observing the measured parameters, it is immediately evident that Pump A is pulling less than one-third of the volumetric flow (ACFM) of Pump B.
capacity comparison test
Continuous Online Monitoring of Pump Performance
Water-to-air mass ratio is an intrinsic parameter that can be used to monitor the capacity of a pump relative to the amount of the air in-leak. The value of the mass ratio is determined by dividing the mass of the water vapor flow by the mass of the air in-leak. A low mass ratio value results when pump capacity is low relative to air in-leak. Pump capacity as measured in mass flow rate for SJAEs, or volumetric flow rate for LRVPs, is dependent on the pump’s inlet pressure. Thus, lower condenser pressure will result in low pump capacity.
For this reason, a given air in-leak may result in more air storage and lower condenser performance under low absolute pressure conditions, such as during low load operation or winter when cooling water temperatures are low. For example, a 20 standard cubic feet per minute (SCFM) leak may not cause excess backpressure at 80 F inlet water temperature but may do so at 60 F. In other words, the water-to-air mass ratio will decrease for a given amount of air in-leak as condenser pressure decreases due to lower exhauster capacity during periods when circulating inlet water temperatures are low. Degraded vacuum pump capacity will also result in a low water-to-air mass ratio.
Image 3 shows air in-leak, mass flow and water-to-air mass ratio for the previously discussed pump set used in the capacity comparison test. With the poor performing Pump A in service, the water-to-air mass ratio is ~1. When Pump B is placed in service, the air in-leak does not change but the increased pump capacity causes a higher flow of water vapor.
The increased water vapor mass flow results in a higher value (i.e., improved) for the water-to-air mass ratio. These values, and thereby the performance of the vacuum system, can be monitored in real time using the data provided by the previously mentioned the multisensor instrument.
Historically, SJAE and LRVP capacity testing required a scheduled test during a unit maintenance outage and support from a manufacturer’s service provider with specially assembled exhauster inlet structures, such as orifice trees, which can be costly and time consuming. The ability to perform continuous, online evaluation of SJAE and LRVP capacity and performance provides benefits in cost savings and improved overall plant performance.