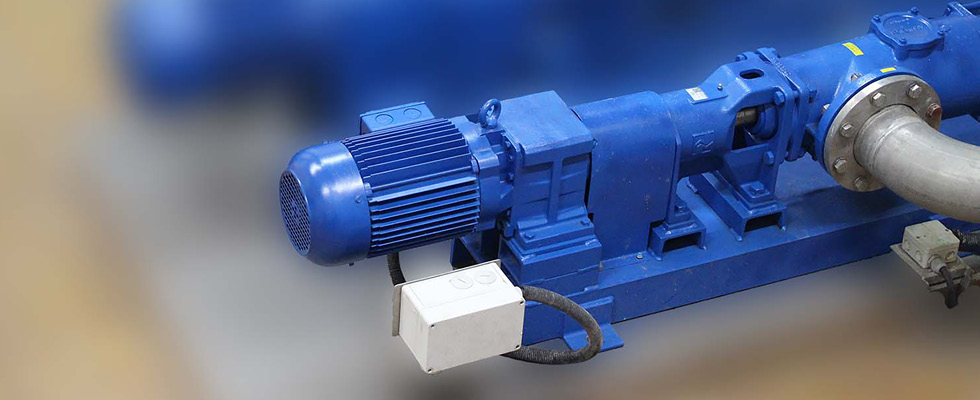
Municipalities across the globe are looking to reduce their energy consumption and minimize their carbon footprint to keep up with changing industry regulations and meet their own sustainability goals.
In wastewater treatment facilities, producing biogas from the treatment process is one way for these operations to become energy self-sufficient. However, achieving this goal hinges on using efficient equipment.
One facility was able to significantly reduce energy consumption with a move to more efficient technology, including permanent magnet synchronous motors (PMSMs).
Energy Self-Sufficiency by 2025
A wastewater treatment plant in Stendal, Germany, set a goal to be entirely energy self-sufficient by 2025. The location has a biogas production facility that provides low carbon energy from waste. Sludge produced from treating wastewater is pumped into storage tanks and then transferred to the biogas plant.
Plant operators began assessing equipment improvements in an effort to reduce reliance on the grid and grow the percentage of operations supported by low carbon energy. They quickly identified one area for improvement: the eccentric screw pumps used in the treatment process.
Eccentric screw pumps, also known as progressive cavity pumps, are used to transport the large amounts of sludge generated during wastewater treatment. This pump design is preferred in wastewater treatment plants, as it is resistant to clogging and can accommodate fluids containing solids.
These pumps must run 24/7, and the large amount of energy required by this continuous operation was a key challenge for the facility. In addition, these pumps often work at low speeds, which can result in the motors that power them operating inefficiently. To help move toward their stated goal of achieving energy self-sufficiency, the Stendal wastewater treatment plant operators wanted to improve the efficiency of these pumps as one way to help reduce the facility’s overall energy demands.
A Move to PMSM Technology
One solution available to the Stendal plant operators was PMSM, which offers efficiency across a wide range of applications and environments. These motors are especially well-suited for facilities requiring continuous operations that also want to reduce their energy consumption and optimize cost-effectiveness.
In PMSMs, the rotating magnetic field is produced in the stator from the 3-phase alternating mains current. In a standard 3-phase motor, a corresponding field is induced in the rotor, which follows the stator field and creates rotational movement. In using permanent magnets in the rotor, no magnetic field must be induced there. This means there is less heat loss, which results in increased efficiency.
A key advantage for PMSMs in eccentric screw pump applications is they deliver high torque at low speeds with increased efficiency. At the Stendal facility, the pumps typically run at about 25 hertz (Hz) to reduce wear and provide a performance reserve for high volumes of water. At this frequency, an asynchronous motor would have to be oversized to deliver the desired torque figure, resulting in energy inefficiency.
Due to inherent characteristics under partial load, PMSMs can deliver full torque at this speed with a smaller motor size. And because this high torque is available from startup, the design is ideal for pumping applications. Operations can expect energy savings of more than 30% with PMSMs when under partial load compared to asynchronous motors.
Another benefit of the PMSM design is that it is power dense. This allows facilities to downsize motors without any loss in performance while also improving efficiency. At the Stendal wastewater treatment plant, the operation was able to downsize from the original 5.5 kilowatts (kW) asynchronous motor to a 3 kW PMSM.
And because PMSMs have low heat characteristics, facilities can eliminate the use of forced cooling fans, which offers another opportunity for cost savings.
The Results
The Stendal facility saw significant results after their switch to pumps powered by PMSM geared motors. To compare electricity demand and primary sludge pumping, they operated two identical pumps alternately with a PMSM and an IE3 asynchronous motor for a month each. They found that the pump with the PMSM consumed 24% less energy.
Their data showed that the pump with the PMSM consumed 495.3 kW of energy to pump 2,410 cubic meters (m3) of primary sludge. The IE3 asynchronous motor required 729.3 kW to pump 2,699.5 m3 of sludge. This equates to 4.866 m3 per kW for the PMSM and 3.7 m3 per kW for the IE3 motor. At Stendal, the eccentric screw pumps can pump almost a third more sludge at the same output. In addition to this increased power efficiency, the updated gear motors also delivered improved performance.
The low power consumption of the drives at Stendal provided a return on investment after just three months, while also reducing power consumption, enhancing performance and taking a large step forward in the move toward low carbon energy at the site.
Considering a PMSM Solution
For facilities considering similar equipment updates to improve efficiency, it is important to work with an equipment partner with expertise in these applications. Look for PMSM solutions that use an efficient rotor design matched to optimized permanent magnets, which provide performance and efficiency advantages.
In many applications, a move to permanent magnet synchronous motors can deliver significant improvements in energy efficiency to help operations meet their sustainability goals without compromising reliability or performance. PMSMs help minimize energy losses, enhance operational efficiency and reduce overall power consumption across a wide range of industries.